South Korea Industrial Robot Sensors Market size was valued at US$ 132.8 million in 2024 and is projected to reach US$ 201.50 million by 2030, at a CAGR of 7.20% during the forecast period 2024-2030.
Sensors specifically designed for use in industrial robotic systems, including vision systems, force sensors, and proximity sensors, enabling precise control and interaction in manufacturing environments.
The South Korean Industrial Robot Sensors market is experiencing strong growth, driven by the country’s highly automated manufacturing sector. South Korea’s industrial robot market, valued at $5.4 billion in 2023, creates substantial demand for specialized sensors. Key trends include the development of high-precision vision sensors for small parts assembly, integration of force-torque sensors for delicate material handling, and adoption of LiDAR sensors for mobile industrial robots. The market faces challenges from the cyclical nature of manufacturing investment and the need for sensors to meet strict reliability standards in 24/7 production environments. Opportunities exist in creating sensor systems for human-robot collaboration and developing industry-specific sensor packages for key sectors like automotive and electronics. With South Korea aiming to have 1 million industrial robots in operation by 2025, there’s growing demand for advanced sensing technologies to enhance robot capabilities. The market benefits from South Korea’s strong position in the semiconductor industry, with companies like Samsung and SK Hynix driving innovation in sensor technologies that can be applied to industrial robotics.
This report contains market size and forecasts of Industrial Robot Sensors in South Korea, including the following market information:
• South Korea Industrial Robot Sensors Market Revenue, 2019-2024, 2024-2030, ($ millions)
• South Korea Industrial Robot Sensors Market Sales, 2019-2024, 2024-2030,
• South Korea Top five Industrial Robot Sensors companies in 2023 (%)
Report Includes
This report presents an overview of South Korea market for Industrial Robot Sensors , sales, revenue and price. Analyses of the South Korea market trends, with historic market revenue/sales data for 2019 – 2023, estimates for 2024, and projections of CAGR through 2030.
This report focuses on the Industrial Robot Sensors sales, revenue, market share and industry ranking of main manufacturers, data from 2019 to 2024. Identification of the major stakeholders in the South Korea Industrial Robot Sensors market, and analysis of their competitive landscape and market positioning based on recent developments and segmental revenues.
This report will help stakeholders to understand the competitive landscape and gain more insights and position their businesses and market strategies in a better way.
This report analyzes the segments data by Type, and by Sales Channels, sales, revenue, and price, from 2019 to 2030. Evaluation and forecast the market size for Humidifier sales, projected growth trends, production technology, sales channels and end-user industry.
Segment by Type
• Proximity Sensor
• Vision Sensor
• Position Sensor
• Temperature Sensor
• Force & Torque Sensor
Segment by Applications
• Manufacturing
• Automotive
• Logistics
• Healthcare
• Aerospace and Defense
Key Companies covered in this report:
• Hyundai Robotics
• Samsung Electronics
• LG Electronics
• Hankook Robotics
• Yujin Robot
• Robotis
• Das Technology
• Doosan Robotics
• Neubility
• Blue Ocean Robotics Korea
Including or excluding key companies relevant to your analysis.
Competitor Analysis
The report also provides analysis of leading market participants including:
• Key companies Industrial Robot Sensors revenues in South Korean market, 2019-2024 (Estimated), ($ millions)
• Key companies Industrial Robot Sensors revenues share in South Korean market, 2023 (%)
• Key companies Industrial Robot Sensors sales in South Korean market, 2019-2024 (Estimated),
• Key companies Industrial Robot Sensors sales share in South Korean market, 2023 (%)
1. Drivers:
- Rising Adoption of Automation and Industry 4.0: South Korea is one of the most advanced industrialized nations globally and a leader in adopting Industry 4.0 technologies. As South Korean industries, including automotive, electronics, and manufacturing, integrate robotics into production lines, the demand for industrial robot sensors is growing. These sensors, such as force torque, proximity, and vision sensors, are critical for robots to perform complex tasks like material handling, welding, and quality control. The country’s focus on smart factories is driving substantial investments in automation technologies, fueling growth in the industrial robot sensors market.
- Advancement in Robotics Technology: South Korea is at the forefront of robotics innovation, with leading companies and academic institutions developing cutting-edge robotic solutions. The advancement in robotics technology, particularly in areas like artificial intelligence (AI), machine learning, and real-time data processing, is pushing the need for more sophisticated and high-precision sensors. Industrial robots in South Korea require advanced sensors to ensure accuracy in operations like precision assembly, defect detection, and real-time decision-making. This technological progress is a major driver of the market as it demands sensor systems capable of supporting next-generation industrial robots.
- Government Initiatives Supporting Robotics and AI: The South Korean government has been proactive in promoting robotics and AI as key industries of the future. Significant government funding has been allocated to support research and development (R&D) in robotics, including industrial applications. The government’s “Manufacturing Innovation 3.0” and “Robot Industry Development Plan” initiatives are designed to encourage the adoption of industrial robots across various sectors, such as electronics, automotive, and shipbuilding. These initiatives include tax incentives, grants, and policy support, which are creating a favorable environment for sensor manufacturers to capitalize on the increasing demand for robot sensors.
- Labor Shortage and Aging Workforce: South Korea faces a growing labor shortage, especially in manufacturing and other labor-intensive industries, due to an aging population and low birth rates. This demographic challenge is pushing companies to adopt more automation to maintain productivity and competitiveness. Industrial robots, equipped with a range of sensors, are being used to fill the gap left by the declining workforce. As industries shift toward automation to combat the labor shortage, the demand for industrial robot sensors is expected to see a significant rise. Robots equipped with advanced sensors are capable of performing tasks that would otherwise require skilled labor, driving market growth.
- High Demand in Automotive and Electronics Industries: South Korea is home to some of the largest global automotive and electronics companies, such as Hyundai, Kia, Samsung, and LG. These industries are highly automated and rely on industrial robots equipped with sophisticated sensors to improve manufacturing precision and efficiency. In automotive manufacturing, for example, robots with force torque and vision sensors are used for welding, painting, and quality control. The electronics sector, known for producing semiconductors, displays, and consumer electronics, also relies on sensor-equipped robots for delicate tasks such as component assembly and inspection. This strong demand from key industries is a major driver of the industrial robot sensors market in South Korea.
2. Restraints:
- High Initial Cost of Implementation: One of the major restraints in the South Korean industrial robot sensors market is the high upfront cost associated with implementing advanced robotics and sensor technologies. Industrial robots equipped with sophisticated sensors, such as vision systems, force torque sensors, and proximity sensors, are expensive to purchase and install. Additionally, the integration of these robots into existing production lines requires significant investment in infrastructure and system upgrades. For many small and medium-sized enterprises (SMEs), the high initial costs present a barrier to adopting robotic systems, limiting the growth of the industrial robot sensors market in certain segments.
- Complexity in Integration and Maintenance: The integration of sensors into industrial robots is technically complex, requiring precise calibration and programming to ensure the sensors function optimally within the robotic system. Sensors such as force torque sensors or vision systems must be carefully calibrated to avoid errors or malfunction during operation. Furthermore, maintaining and servicing sensor-equipped robots is challenging, as it requires specialized knowledge and expertise. In the case of sensor failure, production lines may experience downtime, which can be costly for businesses. This complexity in integration and maintenance is a significant restraint, particularly for industries with limited technical expertise.
- Slow Adoption Among SMEs: While large-scale manufacturers in South Korea have been quick to adopt industrial robots and sensor technologies, the same cannot be said for many SMEs. Smaller businesses often face budget constraints and lack the technical resources needed to implement and maintain sensor-equipped robots. Moreover, the benefits of sensor technology, such as improved precision and efficiency, may not be immediately apparent to SMEs, leading to slower adoption rates. This slow uptake among SMEs limits the overall growth potential of the industrial robot sensors market, as a significant portion of the South Korean industrial base consists of small and medium-sized enterprises.
3. Opportunities:
- Emerging Applications in Collaborative Robots (Cobots): The growing trend of collaborative robots (cobots) in South Korea presents a significant opportunity for the industrial robot sensors market. Cobots are designed to work alongside humans in manufacturing environments, assisting with tasks that require a combination of human dexterity and robotic precision. For cobots to safely interact with human workers, they need sensors such as force torque sensors, proximity sensors, and vision systems to detect human presence and respond to external stimuli. As more industries in South Korea adopt cobots to enhance productivity and ensure worker safety, the demand for advanced sensors to enable these robots’ functionality is expected to increase.
- Expansion of Smart Manufacturing: Smart manufacturing, which involves the use of connected devices, sensors, and real-time data to optimize production processes, is gaining momentum in South Korea. Industrial robots equipped with sensors play a crucial role in smart factories by providing real-time feedback on force, position, and environmental conditions. These sensors help optimize robotic operations, improve quality control, and reduce downtime through predictive maintenance. As South Korean manufacturers continue to invest in smart factory initiatives to improve competitiveness, there is a growing opportunity for sensor manufacturers to supply advanced sensor systems for industrial robots.
- Growth in Semiconductor and Display Manufacturing: South Korea is a global leader in semiconductor and display manufacturing, and these industries require highly precise robots for tasks such as wafer handling, chip assembly, and inspection. Industrial robots in these sectors are equipped with various sensors to ensure the accuracy and cleanliness required in semiconductor fabrication. As the demand for semiconductors and displays continues to grow, driven by global trends in 5G, IoT, and electric vehicles, the need for sensor-equipped industrial robots in these production lines is also increasing. This presents a lucrative opportunity for sensor manufacturers to cater to the semiconductor and display industries’ needs.
- Adoption of AI and Machine Learning in Robotics: The integration of artificial intelligence (AI) and machine learning (ML) into industrial robots is creating new opportunities for the industrial robot sensors market. AI-powered robots can process vast amounts of data collected from sensors in real-time, allowing them to learn, adapt, and optimize their operations based on their environment. Sensors such as vision systems and force torque sensors provide the data needed for AI algorithms to improve robot performance. As AI and ML technologies become more prevalent in South Korean industries, the demand for sensor systems that enable intelligent robotics is expected to rise, creating growth opportunities for sensor manufacturers.
4. Challenges:
- Intense Global Competition: South Korean manufacturers of industrial robot sensors face stiff competition from global companies, particularly from countries like Japan, Germany, and the United States. These countries have well-established sensor industries with extensive R&D capabilities and a strong focus on innovation. Competing against these global players is challenging for South Korean companies, especially in terms of price, technology, and market reach. Local sensor manufacturers must invest heavily in research and innovation to keep pace with international competitors, which can be financially challenging, especially for smaller companies.
- Supply Chain Disruptions: Global supply chain disruptions, such as those caused by the COVID-19 pandemic, have impacted the availability of critical components needed for the production of industrial robot sensors. Shortages of semiconductors and other electronic components have led to delays in the manufacturing and delivery of sensor systems. South Korean companies, which rely on a complex global supply chain for parts and materials, must navigate these disruptions and ensure a stable supply of components to meet market demand. Ensuring supply chain resilience and managing inventory shortages pose a significant challenge for the industrial robot sensors market.
- Evolving Safety and Regulatory Standards: Industrial robot sensors are used in applications where safety is a critical concern, especially in collaborative robotics and human-robot interaction. Meeting stringent safety regulations and standards, both in South Korea and internationally, is a key challenge for sensor manufacturers. Sensors must comply with various certifications to ensure they perform reliably and safely in industrial environments. As safety standards evolve, sensor manufacturers must keep pace with regulatory changes, which can involve costly testing and certification processes. Failing to meet these standards can limit market access, particularly in sectors like automotive, healthcare, and aerospace.
- Need for Continuous Technological Advancements: The industrial robot sensors market is driven by rapid technological advancements, with industries demanding higher precision, faster processing, and more robust sensor systems. To stay competitive, sensor manufacturers must continuously innovate and develop new sensor technologies that can meet the growing demands of robotics applications. However, balancing the need for innovation with the high costs associated with R&D, manufacturing, and product testing is a challenge. Companies that fail to innovate risk being outpaced by competitors in the fast-evolving robotics market.
Key Indicators Analysed
• Market Players & Competitor Analysis: The report covers the key players of the industry including Company Profile, Product Specifications, Production Capacity/Sales, Revenue, Price and Gross Margin 2019-2030 & Sales with a thorough analysis of the market’s competitive landscape and detailed information on vendors and comprehensive details of factors that will challenge the growth of major market vendors.
• South Korean Market Analysis: The report includes South Korean market status and outlook 2019-2030. Further the report provides break down details about each region & countries covered in the report. Identifying its sales, sales volume & revenue forecast. With detailed analysis by types and applications.
• Market Trends: Market key trends which include Increased Competition and Continuous Innovations.
• Opportunities and Drivers: Identifying the Growing Demands and New Technology
• Porters Five Force Analysis: The report provides with the state of competition in industry depending on five basic forces: threat of new entrants, bargaining power of suppliers, bargaining power of buyers, threat of substitute products or services, and existing industry rivalry.
Key Benefits of This Market Research:
• Industry drivers, restraints, and opportunities covered in the study
• Neutral perspective on the market performance
• Recent industry trends and developments
• Competitive landscape & strategies of key players
• Potential & niche segments and regions exhibiting promising growth covered
• Historical, current, and projected market size, in terms of value
• In-depth analysis of the Industrial Robot Sensors Market
• Overview of the regional outlook of the Industrial Robot Sensors Market
Key Reasons to Buy this Report:
• Access to date statistics compiled by our researchers. These provide you with historical and forecast data, which is analyzed to tell you why your market is set to change
• This enables you to anticipate market changes to remain ahead of your competitors
• You will be able to copy data from the Excel spreadsheet straight into your marketing plans, business presentations or other strategic documents
• The concise analysis, clear graph, and table format will enable you to pinpoint the information you require quickly
• Provision of market value (USD Billion) data for each segment and sub-segment
• Indicates the region and segment that is expected to witness the fastest growth as well as to dominate the market
• Analysis by geography highlighting the consumption of the product/service in the region as well as indicating the factors that are affecting the market within each region
• Competitive landscape which incorporates the market ranking of the major players, along with new service/product launches, partnerships, business expansions, and acquisitions in the past five years of companies profiled
• Extensive company profiles comprising of company overview, company insights, product benchmarking, and SWOT analysis for the major market players
• The current as well as the future market outlook of the industry concerning recent developments which involve growth opportunities and drivers as well as challenges and restraints of both emerging as well as developed regions
• Includes in-depth analysis of the market from various perspectives through Porter’s five forces analysis
• Provides insight into the market through Value Chain
• Market dynamics scenario, along with growth opportunities of the market in the years to come
• 6-month post-sales analyst support
We offer additional regional and global reports that are similar:
• Global Industrial Robot Sensors Market
• United States Industrial Robot Sensors Market
• Japan Industrial Robot Sensors Market
• Germany Industrial Robot Sensors Market
• South Korea Industrial Robot Sensors Market
• Indonesia Industrial Robot Sensors Market
• Brazil Industrial Robot Sensors Market
Customization of the Report: In case of any queries or customization requirements, please connect with our sales team, who will ensure that your requirements are meet.

Get Sample Report PDF for Exclusive Insights
Report Sample Includes
- Table of Contents
- List of Tables & Figures
- Charts, Research Methodology, and more...
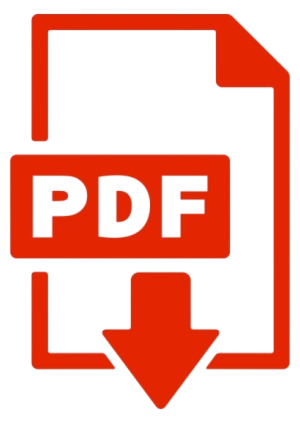