MARKET INSIGHTS
The global Wet Process Equipment Market size was valued at US$ 6,730 million in 2024 and is projected to reach US$ 10,240 million by 2032, at a CAGR of 5.87% during the forecast period 2025-2032.
Wet Process Equipment refers to specialized machinery used in semiconductor manufacturing for cleaning, etching, and surface treatment processes. These systems utilize liquid chemicals or solvents to remove contaminants, deposit thin films, or pattern semiconductor wafers. Key equipment types include wafer cleaning systems, spin rinse dryers, wet etch stations, and plating tools.
The market growth is driven by increasing semiconductor demand across consumer electronics, automotive, and IoT applications. While 300mm wafer processing dominates current demand, the transition to advanced nodes below 7nm is creating new equipment requirements. Recent developments include Tokyo Electron’s 2024 launch of a next-generation single-wafer cleaning system with 30% reduced chemical consumption. Leading players like SCREEN Holdings and ACM Research continue to innovate in edge bead removal and copper plating technologies to meet evolving industry needs.
MARKET DYNAMICS
MARKET DRIVERS
Semiconductor Industry Expansion Fueling Wet Process Equipment Demand
The global semiconductor industry is experiencing unprecedented growth, with wafer production volumes projected to increase by over 35% between 2024 and 2030. This expansion is directly driving demand for wet process equipment, which plays a critical role in cleaning, etching, and surface preparation during chip manufacturing. The transition to smaller node sizes below 5nm requires increasingly sophisticated wet processing solutions to maintain yield rates, creating sustained demand for advanced equipment. Major foundries are announcing capacity expansions, with over twenty new fabrication facilities planned worldwide, each requiring complete wet bench installations worth millions.
Advancements in 3D NAND and DRAM Technologies Accelerating Market Growth
The memory sector is undergoing significant technological transitions, with 3D NAND layer counts exceeding 200 layers and DRAM moving beyond the 1-alpha node. These developments necessitate wet process equipment capable of handling high-aspect ratio structures with nanometer-level precision. Front-end wet stations now integrate advanced megasonic cleaning and selective etching capabilities to address challenges in high-layer-count memory production. The memory segment alone accounts for approximately 45% of total wet process equipment sales, with this share expected to grow as stacking technologies become more complex.
Furthermore, the increasing adoption of novel materials like cobalt interconnects and high-k dielectrics requires specialized wet processing solutions that can safely handle these materials while maintaining process uniformity. Equipment manufacturers are responding with closed-system designs that prevent cross-contamination while enabling precise chemistry control.
MARKET RESTRAINTS
High Capital Costs and Long ROI Periods Limiting Market Expansion
While demand for wet process equipment is strong, the substantial capital investment required presents a significant barrier for many semiconductor manufacturers. A single automated wet station for 300mm wafer processing can exceed $2 million, with full production lines requiring dozens of such systems. The return on investment period for these systems typically spans three to five years, making purchase decisions highly sensitive to economic conditions and fab utilization rates.
Additionally, the specialized nature of wet process equipment creates challenges for smaller semiconductor firms and research institutions. Maintenance contracts and spare parts inventories represent ongoing costs that can account for 15-20% of the total cost of ownership over a five-year period. These financial considerations are particularly impactful in price-sensitive markets and emerging semiconductor regions.
Chemical Management and Environmental Regulations Increasing Operational Complexity
Wet process equipment must comply with increasingly stringent environmental regulations regarding chemical usage and waste disposal. The semiconductor industry’s transition toward more aggressive chemistries for advanced nodes has triggered regulatory scrutiny in multiple regions. Compliance with regulations such as REACH in Europe and similar frameworks in Asia and North America adds substantial overhead to equipment operation.
Chemical consumption per wafer has increased by approximately 40% for advanced nodes compared to legacy processes, driving up operational costs. Equipment manufacturers are responding with closed-loop chemical management systems and point-of-use treatment capabilities, but these solutions increase both capital and operational expenses.
MARKET CHALLENGES
Yield Optimization Pressures in Advanced Node Manufacturing
As semiconductor geometries shrink below 5nm, maintaining process yield becomes increasingly challenging for wet processing steps. Particle control requirements have tightened to below 20nm for critical cleaning processes, demanding equipment capable of achieving single-digit particle adders per wafer. Surface roughness specifications have become equally stringent, with allowable variation measured in angstroms rather than nanometers.
These technical challenges are compounded by the growing complexity of 3D device architectures. Gate-all-around transistors and other advanced structures introduce new cleaning and surface preparation challenges that existing wet process technologies struggle to address. Equipment manufacturers must continuously innovate to keep pace with these demands while maintaining reasonable cost structures.
MARKET OPPORTUNITIES
Emerging Applications in Compound Semiconductors and Advanced Packaging
The rapid growth of compound semiconductor manufacturing for 5G, electric vehicles, and power electronics presents significant opportunities for wet process equipment providers. Gallium nitride and silicon carbide devices require specialized wet processing solutions that differ from traditional silicon processing. The compound semiconductor market is projected to grow at a compound annual rate exceeding 15%, creating a parallel demand stream for customized wet process tools.
Similarly, advanced packaging technologies like fan-out wafer-level packaging and chiplet integration are driving demand for specialized wet process equipment. These applications often require precise selective etching and cleaning capabilities tailored to specific packaging architectures. Equipment capable of handling panel-level processing as well as traditional wafer formats is becoming increasingly valuable in this evolving market segment.
Major equipment suppliers are responding to these opportunities through strategic partnerships with materials science firms and packaging specialists. Collaborative development programs are yielding new wet processing solutions optimized for emerging applications beyond conventional CMOS manufacturing.
WET PROCESS EQUIPMENT MARKET TRENDS
Automation and Industry 4.0 Integration Drive Market Growth
The Wet Process Equipment market is experiencing significant transformation due to the adoption of automation and Industry 4.0 technologies. Fully automatic systems now account for over 35% of the market share, with projections indicating a compound annual growth rate (CAGR) of 7.2% through 2032. This shift is driven by semiconductor manufacturers’ need for precision, repeatability, and reduced human intervention in critical etching, cleaning, and deposition processes. Smart sensors and IoT-enabled wet stations now provide real-time process monitoring, reducing defect rates by up to 40% compared to traditional methods. The integration of AI-driven predictive maintenance further enhances equipment uptime, creating a compelling value proposition for fabrication facilities.
Other Trends
Wafer Size Transition Accelerates Equipment Upgrades
Market dynamics are being reshaped by the industry-wide transition to larger wafer sizes, with 300mm wafer equipment demand growing at 8.4% annually. While 200mm systems still dominate with 52% market penetration, foundries are aggressively retrofitting lines to accommodate next-generation nodes. This transition creates dual demand streams: new installations for advanced logic/memory production and refurbished systems for specialty applications. The compound effect of yield improvements (typically 15-20% on 300mm platforms) and throughput gains makes capital expenditures justifiable despite recent semiconductor market fluctuations.
Geopolitical Factors Reshape Supply Chains
The wet process equipment landscape faces mounting pressure from global trade realignments and technology export controls. While China’s domestic equipment manufacturers currently hold just 12% market share, government subsidies and local content requirements are projected to triple domestic adoption rates by 2030. Concurrently, Western suppliers are establishing secondary manufacturing hubs in Southeast Asia, with Malaysia and Vietnam emerging as preferred locations for back-end equipment assembly. This geographic diversification adds 8-12% to production costs but significantly mitigates supply chain risks exposed during recent chip shortages. The changing landscape presents both challenges for incumbent players and opportunities for agile mid-market equipment providers.
COMPETITIVE LANDSCAPE
Key Industry Players
Leading Manufacturers Expand Technological Capabilities to Maintain Market Leadership
The global Wet Process Equipment market demonstrates a moderately consolidated structure with dominant players controlling approximately 45-50% of the total market share as of 2024. The competitive environment remains intense as semiconductor manufacturers increasingly demand advanced wafer processing solutions with higher precision and automation capabilities.
Shibaura Mechatronics and Tokyo Electron currently lead the market, leveraging their extensive R&D investments and established supply networks across key semiconductor manufacturing hubs. These Japanese manufacturers have particularly strengthened their position through strategic collaborations with foundry operators and integrated device manufacturers.
While mature markets like North America and Europe show preference for high-end automated systems from established players, emerging APAC manufacturers such as NAURA Technology Group and Kingsemi are gaining traction through cost-competitive offerings. The Chinese suppliers have grown their collective market share from 12% in 2020 to nearly 18% in 2024 by catering to domestic semiconductor expansion projects.
Meanwhile, European specialists including RENA and AP&S International GmbH maintain strong positions in niche segments like photovoltaic and MEMS applications through continuous process innovation. Their focus on sustainable chemistry management systems has become particularly valuable as environmental regulations tighten globally.
List of Major Wet Process Equipment Manufacturers
- Shibaura Mechatronics (Japan)
- SCREEN (Japan)
- Tokyo Electron (Japan)
- Veeco Instruments (U.S.)
- RENA (Germany)
- AP&S International GmbH (Germany)
- Modutek (U.S.)
- Wafer Process Systems (U.S.)
- Chemical Art Technology (Japan)
- Solstice (U.S.)
- SiSTEM Technology (Singapore)
- Amerimade Technology (U.S.)
- PNC Process Systems (U.S.)
- ACM Research (China)
- NAURA Technology Group (China)
- Asia Electronics (China)
- Kingsemi (China)
Segment Analysis:
By Type
Fully Automatic Segment Dominates Due to Increasing Demand for High-Precision Semiconductor Manufacturing
The market is segmented based on type into:
- Fully Automatic
- Subtypes: Single-chamber systems, Multi-chamber systems
- Semi-automatic
- Manual
By Application
300 mm Wafer Processing Leads as Semiconductor Industry Shifts to Larger Wafer Sizes
The market is segmented based on application into:
- 150 mm Wafer
- 200 mm Wafer
- 300 mm Wafer
- Other specialized applications
By Technology
Advanced Cleaning Technologies Gain Traction with Increasing Complexity in Semiconductor Fabrication
The market is segmented based on technology into:
- Batch Spray Processing
- Single Wafer Processing
- Immersion Processing
- Other specialized technologies
By End-User
Foundries Account for Major Share Due to Increasing Outsourcing of Semiconductor Manufacturing
The market is segmented based on end-user into:
- Integrated Device Manufacturers (IDMs)
- Foundries
- Outsourced Semiconductor Assembly and Test (OSAT) providers
- Research Institutes
Regional Analysis: Wet Process Equipment Market
North America
The North American wet process equipment market is driven by strong semiconductor and electronics manufacturing demand, particularly in the United States, where major foundries and IDMs (Integrated Device Manufacturers) are investing heavily in advanced fabrication facilities. The U.S. CHIPS Act, which allocates $52 billion to bolster domestic semiconductor production, is accelerating demand for precision wet processing equipment. Environmental regulations on chemical usage in wafer fabrication are pushing manufacturers toward automated, resource-efficient systems. The region shows a preference for fully automated equipment to ensure high throughput and minimal defects in advanced-node wafer processing (below 7nm). Key industry players like Veeco Instruments and Modutek maintain strong footholds here, leveraging their expertise in contamination control and process automation.
Europe
Europe’s wet process equipment market benefits from concentrated semiconductor R&D activities in Germany and the Benelux region, where companies like ASML and Infineon drive demand for specialized etching and cleaning solutions. The EU’s strict REACH regulations compel equipment manufacturers to develop closed-loop chemical handling systems with reduced wastewater generation. There’s growing emphasis on equipment capable of processing compound semiconductors (GaN, SiC) for automotive and renewable energy applications. While the region accounts for a smaller share of global volume compared to Asia, it maintains technological leadership in niche segments like MEMS manufacturing equipment. Collaborative initiatives between academia and manufacturers, such as the European Nanoelectronics Initiative Advisory Council (ENIAC), further stimulate innovation.
Asia-Pacific
Dominating over 65% of global wet process equipment consumption, the Asia-Pacific region thrives on massive semiconductor investments in Taiwan (TSMC), South Korea (Samsung), and China (SMIC). China’s push for semiconductor self-sufficiency has created parallel demand for both imported and domestically-produced equipment, with NAURA Technology Group gaining market share in mid-range wet benches. The region shows particularly strong growth in 300mm wafer processing equipment due to ongoing fab expansions, although price sensitivity remains a challenge for premium European and American suppliers. Japan retains technological leadership in precision cleaning systems through companies like SCREEN and Tokyo Electron, while Southeast Asia emerges as an important market for backend packaging-related wet processes.
South America
The South American market remains nascent for wet process equipment, primarily serving localized PCB and basic semiconductor packaging needs. Limited semiconductor manufacturing infrastructure and dependence on imported electronic components constrain market growth. However, Brazil shows gradual progress in developing its microelectronics industry through government-academia partnerships, creating pockets of demand for basic wet processing solutions. Economic instability and import restrictions pose persistent challenges for equipment suppliers trying to establish footholds in the region. Most demand comes from research institutions and small-scale electronics manufacturers rather than high-volume fabs.
Middle East & Africa
This region represents an emerging opportunity as countries like Saudi Arabia (through the NEOM project) and UAE invest in technology diversification beyond oil. Initial demand focuses on solar PV manufacturing equipment rather than advanced semiconductor processing. Israel constitutes an exception with its strong semiconductor design ecosystem, though local wafer fabrication remains limited. The lack of established semiconductor manufacturing clusters and skilled workforce currently restrain the wet process equipment market’s growth. Nonetheless, multinational equipment suppliers are monitoring the region’s potential, particularly for mid-range wet stations that could serve anticipated MEMS and power electronics fabrication plants in the next decade.
Report Scope
This market research report provides a comprehensive analysis of the global and regional Wet Process Equipment markets, covering the forecast period 2025–2032. It offers detailed insights into market dynamics, technological advancements, competitive landscape, and key trends shaping the semiconductor fabrication equipment industry.
Key focus areas of the report include:
- Market Size & Forecast: Historical data and future projections for revenue, unit shipments, and market value across major regions and segments. The global Wet Process Equipment market was valued at USD 1.84 billion in 2024 and is projected to reach USD 2.76 billion by 2032, growing at a CAGR of 5.2% during the forecast period.
- Segmentation Analysis: Detailed breakdown by product type (Fully Automatic, Semi-automatic, Manual), wafer size (150mm, 200mm, 300mm), and application to identify high-growth segments and investment opportunities.
- Regional Outlook: Insights into market performance across North America (32% market share), Asia-Pacific (45% market share), Europe (18% market share), and other regions, including country-level analysis of key markets like the U.S., China, Japan, and South Korea.
- Competitive Landscape: Profiles of 17 leading market participants including Shibaura Mechatronics (12.3% market share), SCREEN (10.8%), Tokyo Electron (9.5%), and Veeco Instruments (7.2%), covering their product portfolios, R&D investments, and strategic developments.
- Technology Trends & Innovation: Assessment of emerging technologies in wafer cleaning, etching, and deposition processes, including advancements in single-wafer processing and environmental sustainability.
- Market Drivers & Restraints: Evaluation of factors driving market growth such as semiconductor industry expansion (global semiconductor market expected to reach USD 1 trillion by 2030) along with challenges like geopolitical tensions and supply chain constraints.
- Stakeholder Analysis: Insights for equipment manufacturers, foundries, IDMs, investors, and policymakers regarding the evolving semiconductor fabrication ecosystem and strategic opportunities.
Primary and secondary research methods are employed, including interviews with industry experts from top 20 semiconductor companies, data from verified financial reports, and real-time market intelligence to ensure the accuracy and reliability of the insights presented.
FREQUENTLY ASKED QUESTIONS:
What is the current market size of Global Wet Process Equipment Market?
-> Wet Process Equipment Market size was valued at US$ 6,730 million in 2024 and is projected to reach US$ 10,240 million by 2032, at a CAGR of 5.87% during the forecast period 2025-2032.
Which key companies operate in Global Wet Process Equipment Market?
-> Key players include Shibaura Mechatronics, SCREEN, Tokyo Electron, Veeco Instruments, RENA, AP&S International GmbH, and ACM Research, among others.
What are the key growth drivers?
-> Key growth drivers include increasing semiconductor demand, miniaturization of chips, and expansion of 300mm wafer fabs.
Which region dominates the market?
-> Asia-Pacific dominates with 45% market share, led by China, Taiwan, and South Korea.
What are the emerging trends?
-> Emerging trends include automation in wet benches, water recycling systems, and advanced single-wafer processing.

Get Sample Report PDF for Exclusive Insights
Report Sample Includes
- Table of Contents
- List of Tables & Figures
- Charts, Research Methodology, and more...
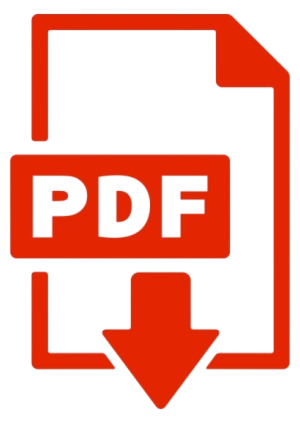