MARKET INSIGHTS
The global Semiconductor O-Rings and Seals Market size was valued at US$ 234 million in 2024 and is projected to reach US$ 321 million by 2032, at a CAGR of 4.6% during the forecast period 2025-2032. This growth aligns with the broader semiconductor industry expansion, which was valued at USD 579 billion in 2022 and is expected to reach USD 790 billion by 2029 at 6% CAGR.
Semiconductor O-Rings and Seals are specialized elastomeric components designed to maintain ultra-high purity environments in semiconductor manufacturing equipment. These critical sealing solutions prevent contamination in processes like wafer fabrication, etching, and deposition, where even microscopic particles can ruin entire production batches. The market offers two primary product types: O-rings (circular cross-section seals) and custom profile seals, each engineered to withstand extreme temperatures, aggressive chemicals, and vacuum conditions.
The market growth is primarily driven by increasing semiconductor production capacity globally, particularly in Asia where foundries are expanding to meet demand for chips used in 5G, AI, and electric vehicles. Furthermore, the transition to smaller node sizes (below 7nm) requires even more stringent contamination control, boosting demand for high-performance sealing solutions. Key players like DuPont and Trelleborg are innovating with advanced materials like perfluoroelastomers (FFKM) to meet these evolving requirements, while regional expansions in semiconductor hubs like Taiwan and South Korea are creating new growth opportunities.
MARKET DYNAMICS
MARKET DRIVERS
Accelerated Semiconductor Manufacturing Expansion Fueling Demand for High-Performance Sealing Solutions
The global semiconductor industry’s rapid growth, projected to reach $790 billion by 2029 with a 6% CAGR, is driving unprecedented demand for specialized O-rings and seals. These components play critical roles in maintaining ultra-clean environments during wafer fabrication, where even nanometer-scale contaminants can ruin entire production batches. The transition to smaller process nodes (5nm and below) requires seals with exceptional chemical resistance and particulate control, creating premium opportunities for advanced materials like perfluoroelastomer (FFKM) seals capable of withstanding aggressive etchants and plasma environments.
Government Investments in Domestic Chip Production Creating New Demand Centers
Major geopolitical initiatives like the U.S. CHIPS Act ($52 billion in funding) and EU Chips Act (€43 billion) are stimulating local semiconductor manufacturing capacity. This will require thousands of new seal installations across planned fabrication facilities worldwide. Industry analysts confirm that each new 300mm wafer fab requires approximately 25,000-30,000 specialized O-rings and seals during initial setup, with annual replacement needs accounting for 15-20% of installed base. The current wave of fab construction represents a $750+ million opportunity for sealing solutions through 2030.
Advanced Packaging Technologies Elevating Seal Performance Requirements
The industry’s shift toward 3D IC packaging and heterogenous integration demands seals that can maintain integrity under extreme thermal cycling (from -55°C to 300°C) while preventing outgassing that could compromise bond strength. Market leaders have introduced new multi-layer seal designs incorporating metal-embedded elastomers to address these challenges. Recent testing shows these advanced seals reduce particulate generation by 78% compared to traditional designs while extending mean time between failures from 1,500 to over 15,000 operational hours in high-vacuum deposition systems.
MARKET RESTRAINTS
Material Supply Chain Constraints Limiting Market Growth
The semiconductor-grade elastomer market faces significant supply challenges, with lead times for critical raw materials like high-purity fluoropolymers extending to 9-12 months in some cases. This bottleneck stems from concentration of production capacity among few specialty chemical manufacturers and stringent purity requirements that eliminate >85% of commercial polymer stock from consideration. Semiconductor seal makers report that supply chain disruptions have caused 20-25% production delays for high-end FFKM components, forcing fabricators to extend maintenance cycles beyond recommended intervals.
Cost Pressures from Chipmakers Restricting Component Pricing Power
While semiconductor manufacturers demand increasingly sophisticated seals, they simultaneously pressure suppliers to reduce component costs by 3-5% annually. This creates profitability challenges for seal manufacturers investing in advanced material R&D. Data indicates that developing a new semiconductor-grade elastomer formulation requires $12-18 million in R&D and 24-36 months of qualification testing before commercialization. The compression between rising development costs and customer pricing expectations has led several mid-tier suppliers to exit the semiconductor sealing market entirely.
MARKET CHALLENGES
Increasing Process Complexity Raising Seal Qualification Barriers
Each new semiconductor process node introduces unique compatibility challenges for sealing materials. Extreme ultraviolet (EUV) lithography systems require seals that can withstand continuous exposure to 13.5nm wavelength radiation without degradation – a property not previously required in the industry. Process equipment OEMs report that seal qualification cycles have extended from 3-6 months to 12-18 months for advanced nodes, reflecting more rigorous testing protocols and multiple iterative design improvements. This extended development timeline creates cash flow pressure for smaller suppliers lacking diversified product portfolios.
Skill Shortages Impacting Specialty Manufacturing Capabilities
The specialized nature of semiconductor seal production requires technicians with expertise in cleanroom molding, precision metrology, and ultra-clean handling protocols. Industry surveys reveal that 45% of manufacturers report critical staffing shortages in these niche skill areas, exacerbated by competition from adjacent high-tech industries. This labor constraint comes as demand for Class 1 cleanroom-certified seals (particle counts <1 per ft³ at 0.1μm) grows by 18% annually. Without adequate workforce development initiatives, production capacity may struggle to keep pace with projected market needs.
MARKET OPPORTUNITIES
Smart Seal Technologies Enabling Predictive Maintenance Solutions
The integration of embedded sensors in critical seals presents a $300+ million revenue opportunity by 2030. Next-generation designs incorporate microsensors to monitor parameters like compression set, temperature extremes, and outgassing potential in real-time. Field trials demonstrate these intelligent seals can predict failure with 92% accuracy 50-100 hours before occurrence, potentially reducing unplanned tool downtime by 40% in deposition and etch systems. This aligns with the industry’s broader Industry 4.0 transition, where equipment connectivity and predictive analytics are becoming standard requirements.
Emerging Materials Addressing Sustainability Requirements
Growing emphasis on environmental sustainability is driving demand for seals using recycled fluoropolymers and bio-based elastomers. Recent advancements allow up to 30% recycled content in semiconductor seals without compromising performance characteristics, reducing the carbon footprint per unit by 22-25%. Over 60% of major chipmakers now include sustainable material requirements in their supplier scorecards, creating competitive advantage for early adopters of green chemistry solutions. The market for eco-friendly semiconductor seals is projected to grow at 28% CAGR through 2030, outpacing conventional product segments.
SEMICONDUCTOR O-RINGS AND SEALS MARKET TRENDS
Advanced Material Innovations Driving Growth in Semiconductor Sealing Solutions
The semiconductor o-rings and seals market is experiencing significant transformation due to advances in high-performance elastomers capable of withstanding extreme conditions. Perfluoroelastomers (FFKM) have emerged as a preferred material for semiconductor fabrication, offering superior resistance to corrosive chemicals, high temperatures exceeding 300°C, and aggressive plasma environments in etching processes. Leading manufacturers are investing heavily in developing compound formulations with enhanced purity levels below 1ppb particulate contamination, critical for next-gen 3nm and 2nm chip manufacturing nodes. The market for specialized semiconductor seals is projected to grow at approximately 7.2% CAGR through 2032, fueled by increasing fab investments exceeding $100 billion annually worldwide.
Other Trends
Miniaturization and Precision Requirements
The relentless drive toward smaller semiconductor geometries below 5nm is creating unprecedented demands for micron-level sealing precision. Manufacturers are developing sub-millimeter o-rings with tolerances under ±0.025mm to prevent particulate generation in EUV lithography systems. This trend is particularly evident in advanced packaging applications where seal performance directly impacts yield rates in chiplet-based architectures. The cleaning segment accounts for over 28% of total seal demand as wafer fabrication processes require increasingly contamination-free environments.
Geographic Expansion of Semiconductor Manufacturing
The global semiconductor fab construction boom is creating regional hotspots for seal manufacturers. While Asia Pacific currently dominates with over 60% market share, the U.S. CHIPS Act and European Chips Act are driving substantial capacity expansions in Western markets. This geographic diversification is prompting seal suppliers to establish localized production facilities near major semiconductor clusters, reducing lead times for critical replacement components. Over 42 new 300mm fabs are planned worldwide through 2030, each requiring thousands of specialized seals across deposition, etching and lithography equipment.
COMPETITIVE LANDSCAPE
Key Industry Players
Leading Manufacturers Focus on High-Performance Material Innovations to Address Semiconductor Demands
The competitive landscape of the semiconductor O-rings and seals market features a mix of multinational corporations and specialized manufacturers. The market remains semi-consolidated, but increasing demand for high-purity materials in semiconductor fabrication processes is driving technology investments among key players. DuPont maintains a dominant position with approximately 18% revenue share in 2024, owing to its proprietary perfluoroelastomer (FFKM) technology that meets stringent semiconductor processing requirements.
Trelleborg Sealing Solutions and Parker Hannifin collectively hold nearly 25% market share, benefiting from their extensive distribution networks and vertically integrated manufacturing capabilities. Both companies have accelerated R&D spending by 12-15% annually since 2022 to develop seals resistant to extreme temperatures and aggressive chemicals used in advanced node semiconductor manufacturing.
Meanwhile, Precision Polymer Engineering (PPE) has emerged as a technology leader in custom-engineered sealing solutions, particularly for EUV lithography applications. The company’s recent capacity expansion in Asia-Pacific positions it well to serve the region’s booming semiconductor fabrication plant construction. Regional players like Eagle Industry and GMORS are gaining traction through competitive pricing strategies, though material certifications remain a barrier for full market penetration.
The market’s competitive intensity continues rising as semiconductor manufacturers demand longer component lifespans with tighter tolerances. Industry leaders are responding through strategic acquisitions – notably Trelleborg’s 2023 purchase of a specialty polymers manufacturer to strengthen its material science capabilities for 3D NAND production environments.
List of Key Semiconductor O-Ring and Seal Manufacturers
- DuPont (U.S.)
- Trelleborg Sealing Solutions (Sweden)
- Parker Hannifin Corporation (U.S.)
- GMORS (U.S.)
- Eagle Industry Co., Ltd. (Japan)
- Marco Rubber & Plastics (U.S.)
- Advanced EMC Technologies (U.S.)
- Precision Polymer Engineering (UK)
Semiconductor O-Rings and Seals Market – Segment Analysis
By Type
O-Ring Segment Dominates Due to Higher Demand in Vacuum and High-Purity Applications
The market is segmented based on type into:
- O-Rings
- Subtypes: Fluorocarbon (FKM), Perfluoroelastomer (FFKM), Silicone (VMQ), and others
- Seals
- Subtypes: Mechanical seals, gasket seals, lip seals, and others
By Application
Crystal Growth (Pulling) Segment Leads Due to Increasing Semiconductor Production
The market is segmented based on application into:
- Crystal Growth (Pulling)
- Thermal (LPCVD) Nitride, Oxide
- Track & Lithography
- Dry Etch and Wet Etch
- Others
By Material
FFKM Gains Traction for Superior Chemical Resistance in Harsh Semiconductor Environments
The market is segmented based on material into:
- Fluorocarbon (FKM)
- Perfluoroelastomer (FFKM)
- Silicone (VMQ)
- Ethylene Propylene Diene Monomer (EPDM)
- Others
By End User
Foundries Account for Largest Share Due to Massive Semiconductor Manufacturing Activities
The market is segmented based on end user into:
- Foundries
- IDMs (Integrated Device Manufacturers)
- OSAT (Outsourced Semiconductor Assembly and Test)
- Others
Regional Analysis: Semiconductor O-Rings and Seals Market
North America
The North American semiconductor O-rings and seals market is driven by strong demand from advanced semiconductor manufacturing facilities, particularly in the United States. With major chipmakers like Intel and Texas Instruments investing heavily in domestic semiconductor production—including Intel’s $20 billion Ohio fab expansion—the region demands high-purity sealing solutions that meet stringent contamination control standards. The U.S. CHIPS and Science Act’s $52.7 billion funding for semiconductor R&D and manufacturing further accelerates market growth. These applications prioritize materials like perfluoroelastomers (FFKM) and fluoroelastomers (FKM) that withstand extreme chemical exposure in processes like etching and deposition. Local suppliers maintain competitive advantages through close collaboration with semiconductor equipment manufacturers (SEMs).
Europe
Europe’s mature semiconductor industry, led by ASML, STMicroelectronics, and Bosch, maintains steady demand for precision sealing solutions with an emphasis on environmental compliance. EU regulations such as REACH and RoHS drive material innovation toward low-outgassing, chemically resistant elastomers. The €43 billion European Chips Act boosts local semiconductor production capabilities, particularly for automotive and industrial applications requiring robust seals for harsh operating conditions. Germany remains the largest regional market due to its concentration of semiconductor equipment manufacturers, while France sees growing investments in power semiconductor fabrication. Market challenges include higher material costs and complex certification requirements compared to Asian competitors.
Asia-Pacific
As the global semiconductor manufacturing hub, Asia-Pacific dominates the O-rings and seals market both in volume and growth potential. Taiwan, South Korea, and China collectively account for over 60% of global semiconductor production capacity, creating massive demand for high-performance sealing components. Taiwan’s TSMC alone consumes significant sealing products for its advanced nodes below 7nm. China’s push for semiconductor self-sufficiency drives domestic seal manufacturers to improve quality, though many fabs still prefer international brands for critical applications. Japan maintains leadership in specialty materials like Kalrez® alternatives, while Southeast Asian nations see growing demand for legacy node production. Price sensitivity remains a key consideration across the region.
South America
The South American market for semiconductor seals remains nascent but shows potential as countries like Brazil develop local electronics manufacturing capabilities. Most demand comes from semiconductor packaging and test facilities rather than front-end fabs. Import dependency on sealing solutions creates supply chain challenges, and economic instability limits capital expenditures on premium materials. However, developing automotive and industrial electronics sectors provide opportunities for basic sealing products. Brazil’s 2023 semiconductor incentive program signals gradual market development, though it lags behind other emerging regions in technology adoption.
Middle East & Africa
This emerging market shows pockets of demand primarily around semiconductor packaging and discrete device manufacturing. The UAE and Saudi Arabia are investing in technology ecosystems that indirectly drive seal demand, while South Africa’s electronics manufacturing sector requires basic sealing components. Market growth is constrained by limited local semiconductor production and reliance on imported sealing solutions. However, the region’s growing focus on renewable energy and smart infrastructure creates long-term opportunities for power semiconductor applications requiring durable seals. Many global suppliers serve the region through distributors rather than direct operations.
Report Scope
This market research report provides a comprehensive analysis of the Global Semiconductor O-Rings and Seals Market, covering the forecast period 2025–2032. It offers detailed insights into market dynamics, technological advancements, competitive landscape, and key trends shaping the industry.
Key focus areas of the report include:
- Market Size & Forecast: Historical data and future projections for revenue, unit shipments, and market value across major regions and segments. The Global Semiconductor O-Rings and Seals market was valued at USD XX million in 2024 and is projected to reach USD XX million by 2032, growing at a CAGR of X% during the forecast period.
- Segmentation Analysis: Detailed breakdown by product type (O-rings and seals), application (Crystal Growth, CVD and PVD, Ion Implant, etc.), and end-user industry to identify high-growth segments and investment opportunities.
- Regional Outlook: Insights into market performance across North America, Europe, Asia-Pacific, Latin America, and the Middle East & Africa, with Asia-Pacific currently dominating the market share.
- Competitive Landscape: Profiles of leading market participants including DuPont, Trelleborg Sealing Solutions, Parker, and Eagle Industry, covering their product offerings, R&D focus, and recent developments.
- Technology Trends & Innovation: Assessment of emerging materials and manufacturing techniques for high-performance sealing solutions in semiconductor fabrication processes.
- Market Drivers & Restraints: Evaluation of factors driving market growth such as increasing semiconductor production and challenges including material costs and supply chain constraints.
- Stakeholder Analysis: Insights for component suppliers, OEMs, system integrators, and investors regarding the evolving semiconductor equipment ecosystem.
Primary and secondary research methods are employed, including interviews with industry experts and data from verified sources to ensure the accuracy and reliability of the insights presented.
FREQUENTLY ASKED QUESTIONS:
What is the current market size of Global Semiconductor O-Rings and Seals Market?
-> The global Semiconductor O-Rings and Seals size was valued at US$ 234 million in 2024 and is projected to reach US$ 321 million by 2032, at a CAGR of 4.6% during the forecast period 2025-2032.
Which key companies operate in Global Semiconductor O-Rings and Seals Market?
-> Key players include DuPont, Trelleborg Sealing Solutions, Parker, Eagle Industry, GMORS, Marco Rubber, and Advanced EMC Technologies, among others.
What are the key growth drivers?
-> Key growth drivers include increasing semiconductor production, demand for advanced fabrication equipment, and stringent requirements for contamination control in cleanroom environments.
Which region dominates the market?
-> Asia-Pacific dominates the market, driven by semiconductor manufacturing hubs in China, Taiwan, South Korea, and Japan.
What are the emerging trends?
-> Emerging trends include development of ultra-clean materials, adoption of perfluoroelastomers, and integration of smart sealing solutions with sensor technology.
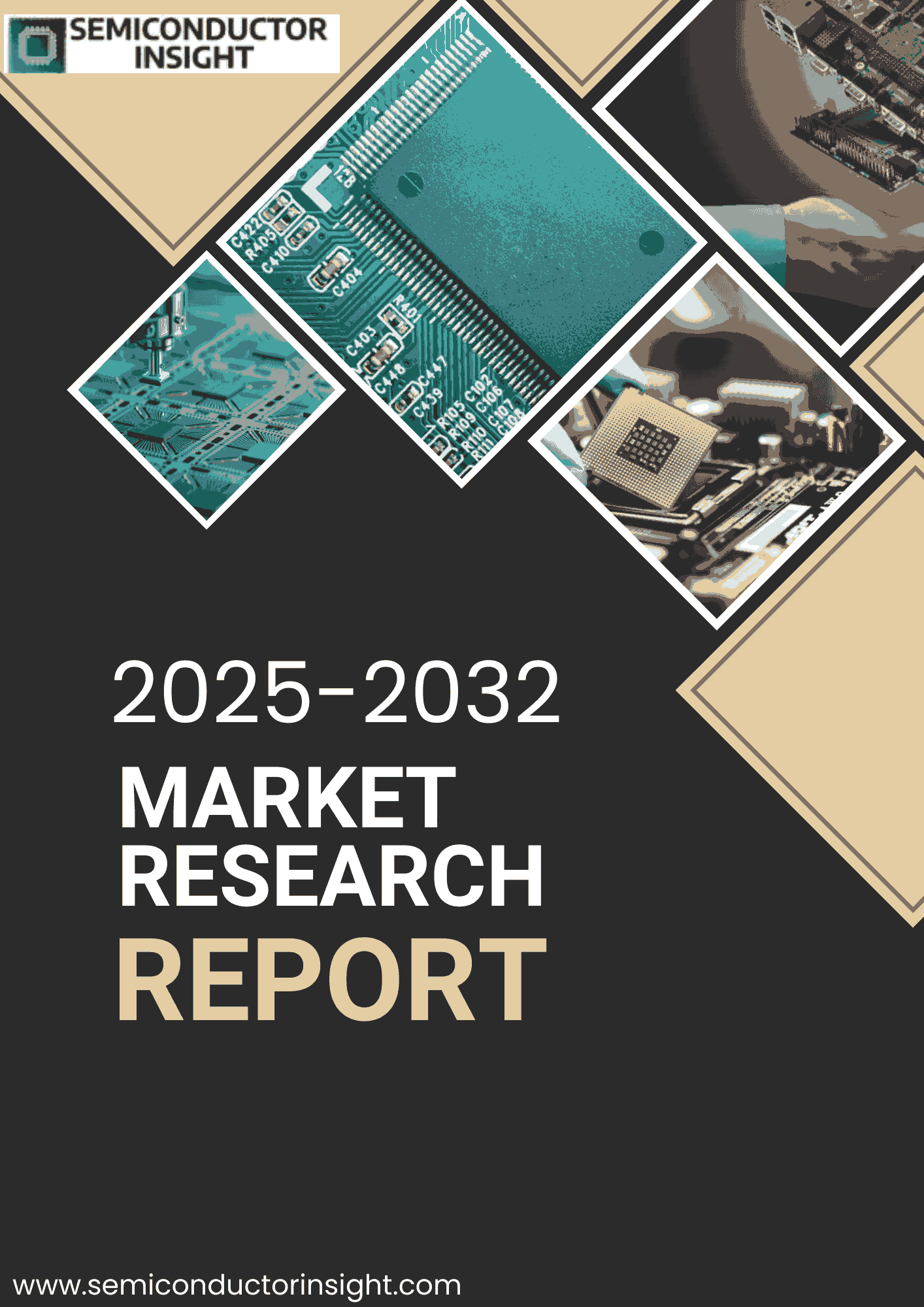
Get Sample Report PDF for Exclusive Insights
Report Sample Includes
- Table of Contents
- List of Tables & Figures
- Charts, Research Methodology, and more...
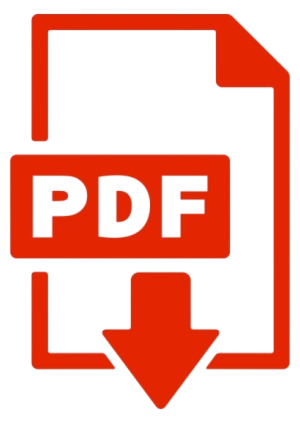