MARKET INSIGHTS
The global Polysilicon Wafer Market size was valued at US$ 8.34 billion in 2024 and is projected to reach US$ 12.87 billion by 2032, at a CAGR of 6.4% during the forecast period 2025-2032. The broader semiconductor industry, valued at USD 579 billion in 2022, is expected to expand to USD 790 billion by 2029, growing at a 6% CAGR, further driving demand for polysilicon wafers.
Polysilicon wafers are thin slices of polycrystalline silicon, a critical raw material for manufacturing solar cells and semiconductor devices. These wafers serve as substrates for integrated circuits (ICs) and photovoltaic modules, facilitating applications in electronics, energy, and automotive sectors. The market is segmented into P-type and N-type wafers, with the latter gaining traction due to higher efficiency in solar applications.
The market growth is fueled by rising demand for renewable energy solutions, particularly solar power, and the expansion of the IoT ecosystem requiring advanced semiconductor components. However, supply chain constraints and fluctuating silicon prices pose challenges. Key players like Zhonghuan Semiconductor and GCL TECH are investing in产能 expansion to meet growing demand, while innovations in wafer thinning and doping technologies enhance performance.
MARKET DYNAMICS
MARKET DRIVERS
Growing Semiconductor Industry to Elevate Demand for Polysilicon Wafers
The global semiconductor market, valued at $579 billion in 2022, is projected to reach $790 billion by 2029, registering a CAGR of 6%. This rapid expansion is directly fueling demand for polysilicon wafers, the fundamental building blocks of integrated circuits and microchips. Analog devices have shown particularly strong growth at 20.76%, followed by sensors (16.31%) and logic chips (14.46%), all requiring high-purity polysilicon wafers as their substrate material. The proliferation of IoT devices, which grew by 21% in 2023 alone, is creating unprecedented demand for the specialized wafers used in microcontroller units (MCUs) and memory chips. Market indicators suggest this trend will continue as 5G networks and smart technologies become ubiquitous.
Renewable Energy Expansion Boosts Photovoltaic Applications
The photovoltaic sector is emerging as a major growth driver, accounting for approximately 35% of polysilicon wafer consumption. Solar panel installations reached a record 220 GW globally in 2023, with projections of 350 GW annually by 2030. This surge is largely driven by government mandates for clean energy and the declining levelized cost of solar electricity, which has fallen below $0.05 per kWh in many markets. Monocrystalline silicon wafers, with their higher efficiency rates approaching 23%, are particularly sought after by solar manufacturers. The industry’s shift toward n-type wafers, which offer better performance though at higher costs, is creating new revenue streams for wafer producers able to meet these technical specifications.
Automotive Electronics Revolution Creates New Demand Channels
The automotive sector is increasingly becoming a key consumer of polysilicon wafers, with semiconductor content per vehicle expected to double from $500 in 2022 to $1,000 by 2026. This radical increase stems from the electrification of vehicles, advanced driver assistance systems (ADAS), and in-vehicle connectivity solutions. Power electronics, which manage battery systems in electric vehicles, require specialized wafers that can handle high voltages and temperatures. With electric vehicle sales projected to grow at 30% CAGR through 2030, manufacturers are investing heavily in wafer production facilities to secure supply chains. Recent capacity expansions in Asia and Europe reflect this strategic shift toward automotive-grade wafer production.
MARKET RESTRAINTS
High Production Costs and Energy Intensive Manufacturing
The polysilicon wafer manufacturing process is exceptionally energy intensive, consuming approximately 100-150 kWh per kilogram of polysilicon produced. These energy requirements, coupled with recent spikes in electricity prices (up 40% in Europe during 2022-2023), have significantly squeezed profit margins. The purification process alone, which requires temperatures exceeding 1,000°C, accounts for 60% of total energy consumption. While some producers have shifted operations to regions with cheaper energy costs, geopolitical considerations and supply chain risks complicate this strategy. The capital expenditure required for a new 50,000 MT polysilicon plant can exceed $1 billion, creating substantial barriers to entry and limiting market responsiveness to demand surges.
Supply Chain Fragility and Geopolitical Risks
The polysilicon supply chain has demonstrated significant vulnerability to geopolitical tensions and trade restrictions. When one major producing country restricted exports in 2023, prices surged by 300% within six months for certain wafer specifications. Over 80% of solar-grade polysilicon production is concentrated in just three countries, creating severe supply risks. The semiconductor industry’s just-in-time inventory models exacerbate these vulnerabilities, as wafer shortages can halt entire production lines. Recent efforts to diversify supply chains through projects in North America and Europe face challenges including higher production costs, longer lead times for facility approvals, and competition for skilled labor.
MARKET OPPORTUNITIES
Emerging Applications in AI and Quantum Computing
Next-generation computing technologies are creating unprecedented opportunities for specialty wafer manufacturers. The artificial intelligence chip market, projected to grow at 38% CAGR through 2030, requires wafers with exceptional purity and defect control. Quantum computing applications demand silicon wafers with isotopic purity levels exceeding 99.9999%, opening a premium market segment with ASPs up to 100x conventional wafers. Several leading cloud providers have announced multi-billion dollar investments in these technologies, with wafer procurement strategies already impacting spot market availability. The unique thermal and electrical properties of advanced polysilicon wafers position them as critical enablers of these transformative technologies.
Technological Advancements in Wafer Production
Innovations in wafer manufacturing processes are creating new competitive advantages. Continuous Czochralski (CCz) crystal growth techniques can increase throughput by 30% while reducing energy consumption. Emerging technologies like direct wafering from molten silicon could potentially reduce material waste by 50% compared to traditional wire sawing methods. Several manufacturers have announced breakthrough advances in diamond wire sawing that improve yield rates from 60% to over 85%. These operational improvements, combined with smart manufacturing systems utilizing AI for quality control, are enabling producers to meet the exacting specifications required for cutting-edge applications while maintaining profitability.
MARKET CHALLENGES
Technical Barriers in Advanced Node Manufacturing
As semiconductor nodes shrink below 5nm, wafer specifications become exponentially more demanding. Current leading-edge processes require wafer bow and warp specifications below 25 microns, surface roughness under 0.2nm, and impurity levels measured in parts per trillion. Few manufacturers can consistently meet these parameters at volume production scales. The shift to 300mm and 450mm wafer sizes introduces additional challenges in maintaining uniformity across larger surface areas. Process control becomes especially critical for emerging memory technologies like 3D NAND, where hundreds of layers must be perfectly aligned across the entire wafer surface. These technical hurdles contribute to yield rates sometimes below 50% for the most advanced processes.
Environmental Regulations and Sustainability Pressures
The wafer manufacturing industry faces increasing scrutiny regarding its environmental footprint. Traditional production methods generate significant amounts of silicon tetrachloride, a hazardous byproduct requiring careful disposal. New regulations in multiple jurisdictions mandate reductions in perfluorocarbon emissions, which have a global warming potential 6,500-9,000 times greater than CO2. Water consumption is another critical issue, with a single wafer requiring up to 2,500 gallons of ultra-pure water during processing. These sustainability challenges are driving R&D investments in closed-loop systems and alternative production methods, but the technical and financial barriers to implementation remain substantial for many producers.
POLYSILICON WAFER MARKET TRENDS
Rising Demand for Solar Energy Driving Market Expansion
The global polysilicon wafer market is experiencing significant growth due to the increasing adoption of solar energy solutions. With solar photovoltaic (PV) installations projected to exceed 250 GW annually by 2025, demand for high-purity polysilicon wafers has surged. Governments worldwide are implementing renewable energy policies, with China aiming for 1,200 GW of solar and wind capacity by 2030, creating substantial market opportunities. Furthermore, technological advancements in wafer production have reduced thickness while maintaining efficiency, enabling cost reductions of 8-10% annually in solar module manufacturing. This trend is particularly evident in the widespread adoption of monocrystalline silicon wafers, which now command over 75% market share in solar applications due to their superior efficiency.
Other Trends
Semiconductor Industry Growth
The semiconductor sector’s relentless expansion continues to fuel polysilicon wafer demand. With the global semiconductor market expected to reach $790 billion by 2029, compound annual growth remains steady at 6%. The shift toward smaller node sizes, particularly below 7nm, requires higher purity polysilicon, creating specialized market segments. Advanced packaging technologies like chiplets further increase wafer consumption, as each package may incorporate multiple silicon die. Simultaneously, the burgeoning IoT market demands more power-efficient chips, driving innovation in wafer manufacturing techniques that reduce defects and improve yield rates.
Supply Chain Diversification and Regional Manufacturing
Recent global supply chain disruptions have accelerated regional polysilicon wafer production initiatives. While China currently dominates manufacturing with over 80% market share, the U.S. and Europe are investing heavily in domestic capabilities through initiatives like the CHIPS Act and European Chips Act. This strategic repositioning has led to $50 billion in announced wafer fab investments across North America and Europe. Concurrently, environmental concerns are reshaping production methods, with leading manufacturers adopting energy-efficient processes that reduce carbon emissions by 30-40% compared to traditional methods. These developments are creating new competitive dynamics in the market while ensuring more stable supply chains for critical industries.
COMPETITIVE LANDSCAPE
Key Industry Players
Innovation and Capacity Expansion Drive Competition in the Polysilicon Wafer Market
The global polysilicon wafer market exhibits a semi-consolidated competitive landscape, dominated by established manufacturers while witnessing emerging players making strategic moves. China-based Zhonghuan Semiconductor and Xinjiang Daqo New Energy currently lead the market, collectively accounting for over 30% of global production capacity as of 2024. Their dominance stems from vertical integration strategies and government-backed expansion projects in the photovoltaic sector.
Meanwhile, GCL TECH has emerged as a formidable competitor through technological advancements in high-purity polysilicon production, reducing manufacturing costs by approximately 18% since 2022. The company’s focus on N-type wafer technology has positioned it strongly in the premium solar wafer segment.
Established semiconductor wafer specialists like WaferPro and TRINITY maintain strong positions in the 300mm wafer segment, catering to advanced logic and memory chip manufacturers. These companies are investing heavily in defect reduction technologies, achieving zero dislocation rates in their prime-grade wafers.
The competitive intensity is further heightened by regional players like JYT Corporation and Danen Technology pursuing aggressive capacity expansions. JYT Corporation recently announced a $2.1 billion investment to establish a new production facility in Vietnam, aiming to capitalize on Southeast Asia’s growing semiconductor ecosystem.
List of Key Polysilicon Wafer Manufacturers Profiled
- Zhonghuan Semiconductor (China)
- Xinjiang Daqo New Energy (China)
- GCL TECH (China)
- WaferPro (U.S.)
- TRINITY (Germany)
- JYT Corporation (Japan)
- SUNWIN ENERGY (China)
- SN Materials (South Korea)
- Huita Optoelectronic Material (China)
- Danen Technology (Taiwan)
- SUNTRO (China)
Segment Analysis:
By Type
N-Type Segment Dominates Due to Higher Efficiency in Solar Cells and Semiconductor Applications
The market is segmented based on type into:
- P Type
- Widely used in power devices due to stable performance
- N Type
By Application
Semiconductor Segment Leads the Market Owing to Increasing Electronic Device Production
The market is segmented based on application into:
- Semiconductor
- Photovoltaic
- Other
By Diameter
300mm Wafers Dominate Production Due to Higher Cost Efficiency in Semiconductor Fabrication
The market is segmented based on diameter into:
- 150mm
- 200mm
- 300mm
- Others
By End-User Industry
Consumer Electronics Sector Shows Strong Growth Due to Expanding Smart Device Market
The market is segmented based on end-user industry into:
- Consumer Electronics
- Automotive
- Industrial
- Energy
- Others
Regional Analysis: Polysilicon Wafer Market
North America
The North American polysilicon wafer market is driven by strong semiconductor manufacturing capabilities and renewable energy initiatives. The United States alone accounts for over 35% of global semiconductor production, creating consistent demand for high-quality N-type and P-type polysilicon wafers. While the CHIPS Act provides $52 billion in subsidies for domestic semiconductor manufacturing, supply chain disruptions and trade tensions with China pose challenges. Solar energy adoption is accelerating, particularly in California and Texas, further boosting photovoltaic-grade wafer demand. However, higher production costs compared to Asian manufacturers limit local wafer suppliers’ competitiveness in global markets.
Europe
Europe’s polysilicon wafer landscape balances semiconductor innovation with green energy ambitions. Germany leads in semiconductor-grade wafer consumption due to its automotive and industrial electronics industries. The EU’s 2030 Climate Target Plan, mandating 40% renewable energy usage, is driving photovoltaic wafer adoption despite reliance on imports. Recent investments in carbon-neutral polysilicon production (like Norway’s REC Silicon plant restart) signal commitment to sustainable wafer manufacturing. However, energy price volatility from geopolitical tensions threatens cost-sensitive wafer producers. Research partnerships between IMEC and wafer manufacturers aim to develop thinner, more efficient wafers for next-gen chips.
Asia-Pacific
Dominating over 75% of global polysilicon wafer production, Asia-Pacific remains the undisputed market leader. China’s integrated solar supply chain and semiconductor expansion projects position it as both largest consumer and producer. Japan and South Korea maintain technological leadership in high-purity semiconductor wafers, while Southeast Asian nations emerge as cost-effective alternatives. Regional dynamics reveal contrasts: China’s Xinjiang province produces 45% of global solar-grade polysilicon, facing trade restrictions, whereas Taiwan’s wafer suppliers thrive through advanced semiconductor partnerships like TSMC. The region faces overcapacity risks in solar wafers but benefits from government subsidies and vertically integrated supply chains.
South America
South America presents niche opportunities in polysilicon wafers, primarily serving the renewable energy sector. Brazil’s solar capacity expansion (projected 24GW by 2031) stimulates demand for photovoltaic wafers, though the region lacks local production capabilities. Chile’s mining industry drives specialized semiconductor wafer needs for industrial electronics. Economic instability and import dependency constrain market growth, with most polysilicon wafers sourced from China. Emerging policies promoting local renewable manufacturing could gradually reshape the supply landscape, though infrastructure limitations persist for high-tech wafer production.
Middle East & Africa
The MEA polysilicon wafer market remains in developmental stages, with growth concentrated in Gulf Cooperation Council countries. Saudi Arabia’s $6.4 billion semiconductor manufacturing initiative and UAE’s renewable energy targets create new wafer demand channels. Africa’s solar electrification projects increasingly require photovoltaic wafers, though price sensitivity favors lower-cost Chinese imports. The region benefits from energy cost advantages for polysilicon production but lacks technical expertise and supporting industries. Strategic partnerships, like Egypt’s collaboration with European solar firms, may catalyze localized wafer supply chains over the next decade.
Report Scope
This market research report provides a comprehensive analysis of the global and regional Polysilicon Wafer markets, covering the forecast period 2025–2032. It offers detailed insights into market dynamics, technological advancements, competitive landscape, and key trends shaping the industry.
Key focus areas of the report include:
- Market Size & Forecast: Historical data and future projections for revenue, unit shipments, and market value across major regions and segments. The global Polysilicon Wafer market was valued at USD million in 2024 and is projected to reach USD million by 2032, growing at a CAGR of % during the forecast period.
- Segmentation Analysis: Detailed breakdown by product type (P Type, N Type), technology, application (Semiconductor, Photovoltaic, Others), and end-user industry to identify high-growth segments and investment opportunities.
- Regional Outlook: Insights into market performance across North America, Europe, Asia-Pacific, Latin America, and the Middle East & Africa, with Asia-Pacific accounting for the largest market share in 2024.
- Competitive Landscape: Profiles of leading market participants including SN Materials, TRINITY, WaferPro, SUNWIN ENERGY, Zhonghuan Semiconductor, and Xinjiang Daqo New Energy, covering their product portfolios, manufacturing capabilities, and strategic initiatives.
- Technology Trends & Innovation: Assessment of emerging wafer fabrication technologies, integration with semiconductor manufacturing processes, and advancements in photovoltaic applications.
- Market Drivers & Restraints: Evaluation of factors such as growing semiconductor demand, renewable energy adoption, and supply chain challenges impacting market growth.
- Stakeholder Analysis: Strategic insights for wafer manufacturers, semiconductor companies, solar panel producers, and investors regarding market opportunities and competitive positioning.
The analysis incorporates both primary and secondary research methodologies, including interviews with industry leaders, verified market data, and proprietary forecasting models to ensure accuracy and reliability.
FREQUENTLY ASKED QUESTIONS:
What is the current market size of Global Polysilicon Wafer Market?
-> Polysilicon Wafer Market size was valued at US$ 8.34 billion in 2024 and is projected to reach US$ 12.87 billion by 2032, at a CAGR of 6.4% during the forecast period 2025-2032.
Which key companies operate in Global Polysilicon Wafer Market?
-> Key players include SN Materials, TRINITY, WaferPro, Zhonghuan Semiconductor, Xinjiang Daqo New Energy, and GCL TECH, among others.
What are the key growth drivers?
-> Key growth drivers include increasing semiconductor demand, expansion of solar energy capacity, and technological advancements in wafer fabrication.
Which region dominates the market?
-> Asia-Pacific dominates the market, accounting for over 60% of global production, driven by strong semiconductor and solar industries in China, Japan, and South Korea.
What are the emerging trends?
-> Emerging trends include larger wafer sizes (300mm+), thinner wafers for advanced applications, and integration with next-generation semiconductor technologies.
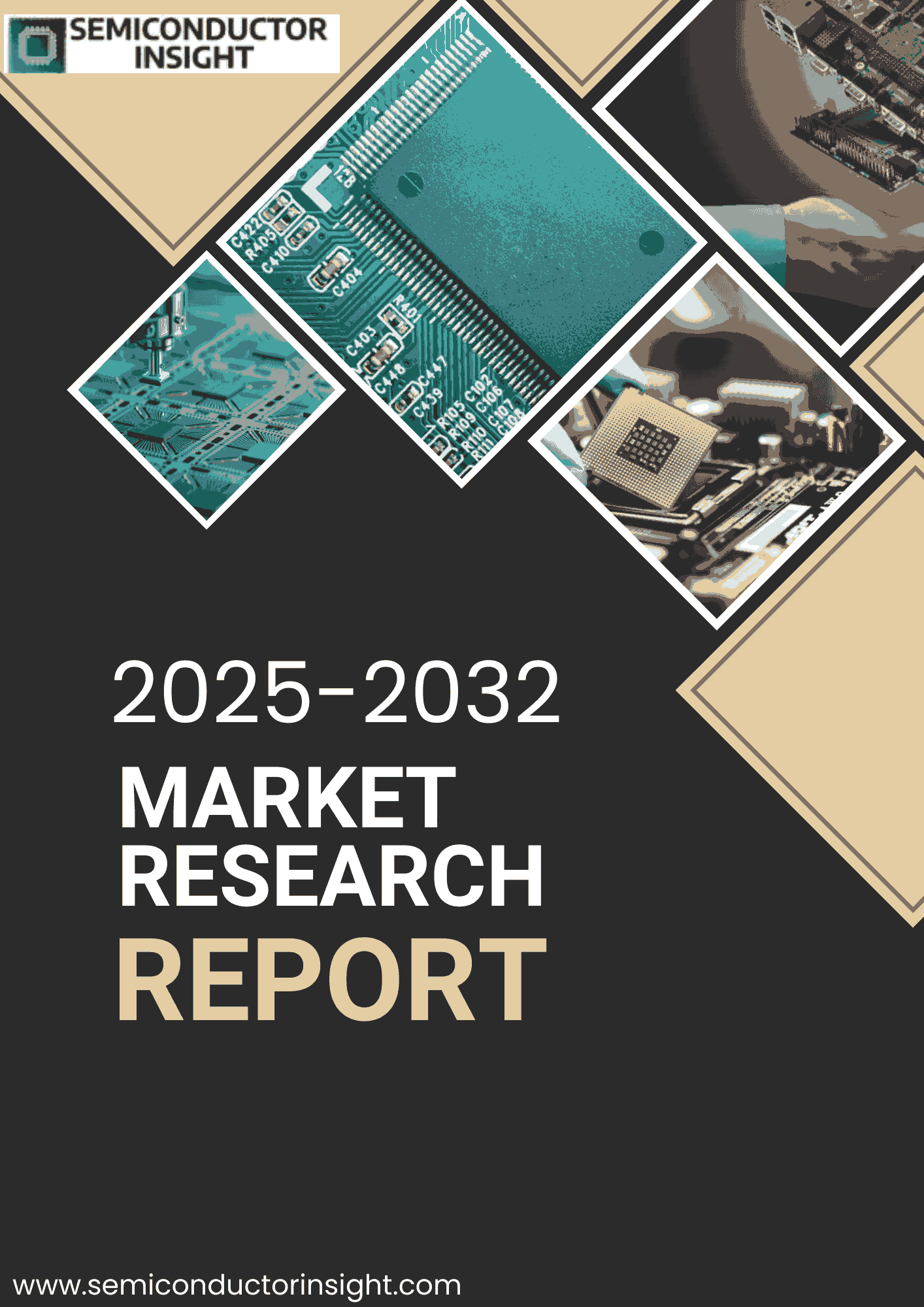
Get Sample Report PDF for Exclusive Insights
Report Sample Includes
- Table of Contents
- List of Tables & Figures
- Charts, Research Methodology, and more...
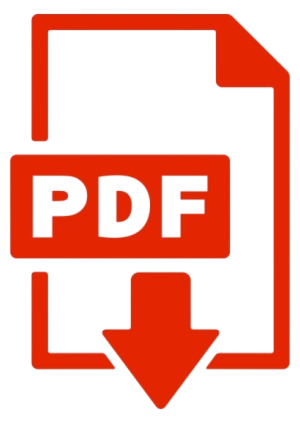