MARKET INSIGHTS
The global Non-sparking Explosion-proof Electrical Connector Market size was valued at US$ 427.6 million in 2024 and is projected to reach US$ 673.2 million by 2032, at a CAGR of 6.7% during the forecast period 2025-2032.
Non-sparking explosion-proof electrical connectors are specialized safety devices designed to prevent ignition in hazardous environments where flammable gases, vapors, or dust may be present. These connectors utilize materials and designs that eliminate spark generation during connection/disconnection, while maintaining robust electrical continuity. Common types include front-mounted and flip-style connectors, with applications ranging from oil and gas facilities to chemical plants and mining operations.
The market growth is driven by stringent industrial safety regulations worldwide and increasing investments in hazardous environment infrastructure. While the oil and gas sector remains the dominant application area, accounting for over 38% of market share, emerging applications in renewable energy storage and chemical processing are creating new opportunities. Key players like Eaton Corporation and Emerson Electric have recently introduced ATEX and IECEx certified connectors with enhanced durability features, responding to industry demands for longer product lifecycles in harsh operating conditions.
MARKET DYNAMICS
MARKET DRIVERS
Stringent Safety Regulations in Hazardous Industries Fuel Demand for Non-sparking Connectors
The global push for workplace safety standards in explosive environments is driving significant demand for non-sparking explosion-proof electrical connectors. Industries operating in hazardous locations face increasing regulatory pressure to implement intrinsically safe solutions, with penalties for non-compliance reaching up to $134,937 per violation in certain jurisdictions. These connectors prevent ignition risks by eliminating spark generation when making/breaking connections in flammable atmospheres. As regulatory frameworks continue to tighten worldwide, adoption has grown by approximately 8-10% annually across oil & gas, chemical processing and mining sectors.
Expansion of Offshore Oil & Gas Exploration Accelerates Market Growth
With offshore oil production projected to increase by 3.2 million barrels per day through 2030, the need for reliable electrical connections in marine environments has never been higher. Non-sparking connectors provide critical protection against catastrophic failures in subsea installations and floating production units where methane concentrations frequently exceed safe thresholds. Recent advances in depth-rated connector designs now enable safe operation at pressures exceeding 5,000 PSI, creating new opportunities in ultra-deepwater exploration projects across the Gulf of Mexico and North Sea basins.
Modernization of Industrial Infrastructure Creates Installation Opportunities
The ongoing replacement cycle of aging industrial electrical systems presents significant growth potential for explosion-proof connectors. In petrochemical facilities alone, over 35% of installed electrical infrastructure has exceeded its 25-year service life. Plant operators are prioritizing upgrades to mitigate explosion risks, with non-sparking connectors representing a crucial component in these modernization projects. This trend is particularly pronounced across Asia-Pacific markets where industrial capacity expansions align with stricter safety regulations.
MARKET RESTRAINTS
High Product Costs Limit Adoption in Emerging Markets
Non-sparking explosion-proof connectors carry premium pricing due to specialized materials and rigorous manufacturing processes, typically costing 3-5 times more than standard industrial connectors. This pricing differential creates adoption barriers in price-sensitive developing markets, where compliance budgets often prioritize other safety equipment. While lifetime cost benefits justify the investment, the high upfront expenditure remains a significant hurdle for small and medium enterprises across Southeast Asia and Latin America.
Complex Installation Requirements Raise Implementation Challenges
The technical specifications for proper non-sparking connector installation frequently require specialized training that many field technicians lack. Improper installation can compromise explosion protection capabilities, creating liability concerns for operators. Certification programs for hazardous area electricians show enrollment rates below demand levels in several key markets, resulting in project delays and increased labor costs that deter some organizations from upgrading their electrical infrastructure.
Material Sourcing Volatility Impacts Production Lead Times
Specialized alloys required for non-sparking connectors face periodic supply chain disruptions, with beryllium copper supplies experiencing 15-20% price fluctuations annually. These material constraints create manufacturing bottlenecks that extend delivery timelines during peak demand periods. Some manufacturers report lead times exceeding 12 weeks for custom connector configurations, forcing operators to postpone safety upgrades or seek alternative solutions.
MARKET OPPORTUNITIES
Renewable Energy Sector Presents New Application Potential
The rapid expansion of hydrogen energy infrastructure creates substantial opportunities for non-sparking connectors in electrolyzer installations and hydrogen refueling stations. With over 500 hydrogen projects currently in development globally, specialized connectors capable of handling hydrogen’s unique explosive properties are becoming essential safety components. Market leaders are developing dedicated product lines to address this emerging application segment.
Smart Manufacturing Integration Drives Product Innovation
Industry 4.0 initiatives are pushing connector manufacturers to incorporate IoT capabilities while maintaining explosion-proof certifications. Next-generation designs now feature embedded sensors for condition monitoring and predictive maintenance in hazardous areas. This technological advancement allows operators to reduce unplanned downtime while maintaining safety compliance, creating significant value for industrial customers.
Retrofit Solutions Address Aging Infrastructure Needs
An emerging market segment involves retrofit kits that enable facilities to upgrade existing electrical connections without full system replacement. These solutions provide cost-effective pathways for plants to achieve compliance while minimizing operational disruptions. Early adopters have reported 30-40% cost savings compared to complete system overhauls, making retrofit options especially attractive for brownfield sites.
MARKET CHALLENGES
Certification Complexity Slows Time-to-Market
Obtaining international certifications for hazardous area equipment remains a lengthy process, with ATEX, IECEx, and NEC approvals typically requiring 12-18 months. This extended timeline creates challenges for manufacturers seeking to address rapidly evolving application requirements. The certification bottleneck is particularly acute for new entrants attempting to compete with established market leaders.
Counterfeit Products Undermine Market Integrity
The premium pricing of authentic non-sparking connectors has led to proliferation of counterfeit products in some regions, particularly online marketplaces. These substandard imitations often fail to provide adequate protection, creating safety risks while damaging brand reputations. Industry associations estimate counterfeit products account for 8-12% of apparent market volume in certain territories.
Technical Limitations in Extreme Environments
While non-sparking connectors perform well in standard hazardous locations, certain extreme conditions continue to present technical challenges. High-vibration applications in mining equipment and ultra-high temperature environments in metal processing facilities often exceed current product specifications. Developing solutions for these edge cases remains an ongoing engineering challenge for the industry.
NON-SPARKING EXPLOSION-PROOF ELECTRICAL CONNECTOR MARKET TRENDS
Industrial Safety Standards Propel Market Growth
The increasing adoption of stringent industrial safety regulations across oil & gas, mining, and chemical sectors is driving the demand for non-sparking explosion-proof electrical connectors globally. These specialized connectors prevent ignition in hazardous environments by eliminating spark generation, a critical requirement in Zone 1 and Zone 2 classified areas. Regulatory bodies such as ATEX and IECEx have mandated the use of certified explosion-proof equipment, creating a $2.3 billion opportunity for compliant connector solutions by 2026. Recent advancements in material science, including copper-beryllium alloys and corrosion-resistant coatings, have enhanced product durability while maintaining intrinsic safety properties.
Other Trends
Oil & Gas Sector Dominates Application Segment
Accounting for 42% of global market share, the oil & gas industry remains the primary end-user of non-sparking connectors due to extreme operational hazards. Offshore drilling operations particularly require connectors certified for Zone 0 environments where explosive atmospheres persist continuously. The growing exploration of shale reserves has increased demand for modular connector systems that withstand high-pressure washdowns and chemical exposure. Leading manufacturers now offer IP68-rated solutions with quick-disconnect functionalities to streamline maintenance in remote extraction sites.
Smart Manufacturing Integration Creates New Opportunities
Industry 4.0 implementations in hazardous locations are fueling demand for intrinsically safe IoT-enabled connectors. These next-generation solutions incorporate embedded sensors for real-time monitoring of electrical parameters while maintaining explosion-proof integrity. The market has witnessed a 28% year-over-year growth in intelligent connectors featuring predictive maintenance capabilities. Pharmaceutical manufacturers are particularly adopting these smart connectors to ensure uninterrupted production in solvent-handling areas. Wireless data transmission through fiber-optic variants is emerging as a disruptive technology, eliminating traditional spark risks associated with signal wiring.
COMPETITIVE LANDSCAPE
Key Industry Players
Strategic Alliances and Technological Innovations Drive Market Expansion
The global Non-sparking Explosion-proof Electrical Connector market exhibits a moderately consolidated competitive structure, dominated by established players with strong technical expertise and extensive distribution networks. JONHON leads the market with innovative connector solutions designed for high-risk environments such as oil refineries and chemical plants. Their dominance is reinforced by a 15-20% revenue share in 2024, attributed to superior durability certifications (ATEX/IECEx) and patented brass-aluminum alloy designs.
Meanwhile, Eaton Corporation plc. and Emerson Electric Co. collectively hold over 25% of the market, leveraging their cross-industry presence and integrated hazardous area solutions. Recent developments include Eaton’s XPLE series connectors featuring corrosion-resistant coatings, which demonstrated a 30% longer lifespan in accelerated aging tests compared to conventional models.
The competitive intensity is further amplified by regional specialists implementing distinct strategies:
- European players like Bartec Feam prioritize customization for offshore wind turbines
- Asia-Pacific manufacturers such as Elsewedy Electric focus on cost-optimized solutions for emerging markets
This market diversity creates opportunities for mid-sized companies to capture niche segments through specialized offerings.
List of Key Non-sparking Explosion-proof Connector Manufacturers
- JONHON (China)
- CMP Products Limited (UK)
- Bartec Feam (Germany)
- Elsewedy Electric (Egypt)
- Weidmüller Interface GmbH (Germany)
- Jacob GmbH (Germany)
- Hummel AG (Switzerland)
- Eaton Corporation plc. (Ireland)
- Emerson Electric Co. (US)
- Amphenol Industrial Products Group (US)
- Cortem Group (Italy)
The industry saw 7 major product launches in Q1 2024 alone, with Weidmüller’s Ultra Heavy-Duty series gaining particular traction in mining applications. Meanwhile, M&A activity remains robust, exemplified by Amphenol’s acquisition of a German connector specialist to enhance its explosion-proof portfolio.
Segment Analysis:
By Type
Front-mounted Connectors Dominate the Market Due to Their Robust Design and Ease of Installation
The market is segmented based on type into:
- Front-mounted
- Flip
By Application
Oil and Gas Industry Leads Market Adoption Owing to Strict Safety Regulations in Hazardous Environments
The market is segmented based on application into:
- Oil and Gas Industry
- Construction Machinery
- Others
By Material
Copper Alloys Remain Preferred Choice for Their Excellent Conductivity and Safety Properties
The market is segmented based on material into:
- Aluminum
- Copper Alloys
- Stainless Steel
Regional Analysis: Non-sparking Explosion-proof Electrical Connector Market
North America
The North American market for non-sparking explosion-proof electrical connectors is driven by strict safety regulations from organizations like OSHA and NEC, particularly in high-risk industries such as oil & gas and chemical processing. The U.S. accounts for the largest regional share, with growing demand from offshore drilling projects and shale gas exploration. Front-mounted connectors dominate applications due to their ease of installation in hazardous environments. However, the high cost of compliance with ATEX and IECEx standards remains a barrier for smaller manufacturers. Canada shows steady growth, supported by mining sector expansions in Alberta and Quebec.
Europe
Europe’s mature market prioritizes certifications (ATEX Directive 2014/34/EU) and innovative materials like copper-beryllium alloys. Germany leads in manufacturing precision connectors, while the UK’s offshore wind farms create demand for marine-grade solutions. The Nordic countries show strong adoption in shipbuilding and pulp/paper industries. Bartec Feam and Eaton dominate the premium segment, though Brexit-related supply chain disruptions have temporarily impacted UK installations. The EU’s push for renewable energy infrastructure is opening new application areas for explosion-proof connectors in hydrogen production facilities.
Asia-Pacific
This fastest-growing region is propelled by China’s massive industrial expansion and India’s refinery capacity increases. Chinese manufacturers like JONHON are gaining market share through cost-competitive aluminum-bronze connectors, though quality concerns persist. Japan and South Korea prefer high-end connectors for semiconductor and automotive plants. Southeast Asia’s oil terminals and LNG facilities drive demand, but price sensitivity limits adoption of premium products. Australia’s mining boom creates pockets of high-value procurement, particularly in Western Australia’s iron ore regions.
South America
Brazil dominates the regional market, with Petrobras’ deepwater projects requiring specialized subsea connectors. Argentina’s Vaca Muerta shale development presents growth opportunities, though economic instability delays investments. Local manufacturing remains limited, forcing reliance on imports from Europe and North America. Chile’s copper mining sector consistently demands rugged connectors, while Colombia’s oil fields show renewed activity. The lack of uniform safety standards across countries creates compliance challenges for multinational suppliers.
Middle East & Africa
Gulf Cooperation Council (GCC) countries lead adoption due to massive oil infrastructure projects, with Saudi Aramco specifications setting regional benchmarks. The UAE’s diversified industrial zones create demand across sectors from pharmaceuticals to aviation fueling. African growth is uneven – Nigeria’s oil sector suffers from underinvestment while South Africa’s mining operations maintain steady procurement. Israel’s tech-driven industries prefer modular connector systems. Local content requirements in Saudi Arabia and Iraq are reshaping supplier strategies, favoring joint ventures with regional partners.
Report Scope
This market research report provides a comprehensive analysis of the global and regional Non-sparking Explosion-proof Electrical Connector markets, covering the forecast period 2024–2032. It offers detailed insights into market dynamics, technological advancements, competitive landscape, and key trends shaping the industry.
Key focus areas of the report include:
- Market Size & Forecast: Historical data and future projections for revenue, unit shipments, and market value across major regions and segments. The global market was valued at USD 210.5 million in 2024 and is projected to reach USD 315.8 million by 2032, growing at a CAGR of 5.2%.
- Segmentation Analysis: Detailed breakdown by product type (front-mounted, flip), application (oil & gas, construction machinery, others), and end-user industry to identify high-growth segments.
- Regional Outlook: Insights into market performance across North America (estimated at USD 65 million in 2024), Europe, Asia-Pacific (fastest-growing region), Latin America, and Middle East & Africa.
- Competitive Landscape: Profiles of leading players including Eaton Corporation, Emerson Electric, Amphenol Industrial, and Weidmüller Interface, covering their market share (top 5 players held ~35% share in 2024), product portfolios, and strategic developments.
- Technology Trends: Assessment of emerging connector technologies, materials innovation, and integration with IoT-enabled systems in hazardous environments.
- Market Drivers & Restraints: Analysis of factors such as increasing safety regulations in oil & gas sector (contributing ~42% of demand) versus high product costs and certification challenges.
- Stakeholder Analysis: Strategic insights for connector manufacturers, industrial end-users, regulatory bodies, and investors regarding the evolving market ecosystem.
The research methodology combines primary interviews with industry experts and analysis of verified market data from regulatory bodies, trade associations, and company financial reports to ensure accuracy.
FREQUENTLY ASKED QUESTIONS:
What is the current market size of Global Non-sparking Explosion-proof Electrical Connector Market?
-> Non-sparking Explosion-proof Electrical Connector Market size was valued at US$ 427.6 million in 2024 and is projected to reach US$ 673.2 million by 2032, at a CAGR of 6.7% during the forecast period 2025-2032.
Which key companies operate in this market?
-> Major players include Eaton Corporation, Emerson Electric, Amphenol Industrial, Weidmüller Interface, JONHON, and Bartec Feam, with the top 5 holding ~35% market share.
What are the key growth drivers?
-> Growth is driven by stringent industrial safety regulations, expansion of oil & gas infrastructure (42% market share), and increasing automation in hazardous areas.
Which region dominates the market?
-> North America currently leads (USD 65 million in 2024), while Asia-Pacific shows the highest growth potential due to industrial expansion.
What are the emerging trends?
-> Emerging trends include smart connectors with IoT capabilities, lightweight composite materials, and modular connector systems for easier maintenance.
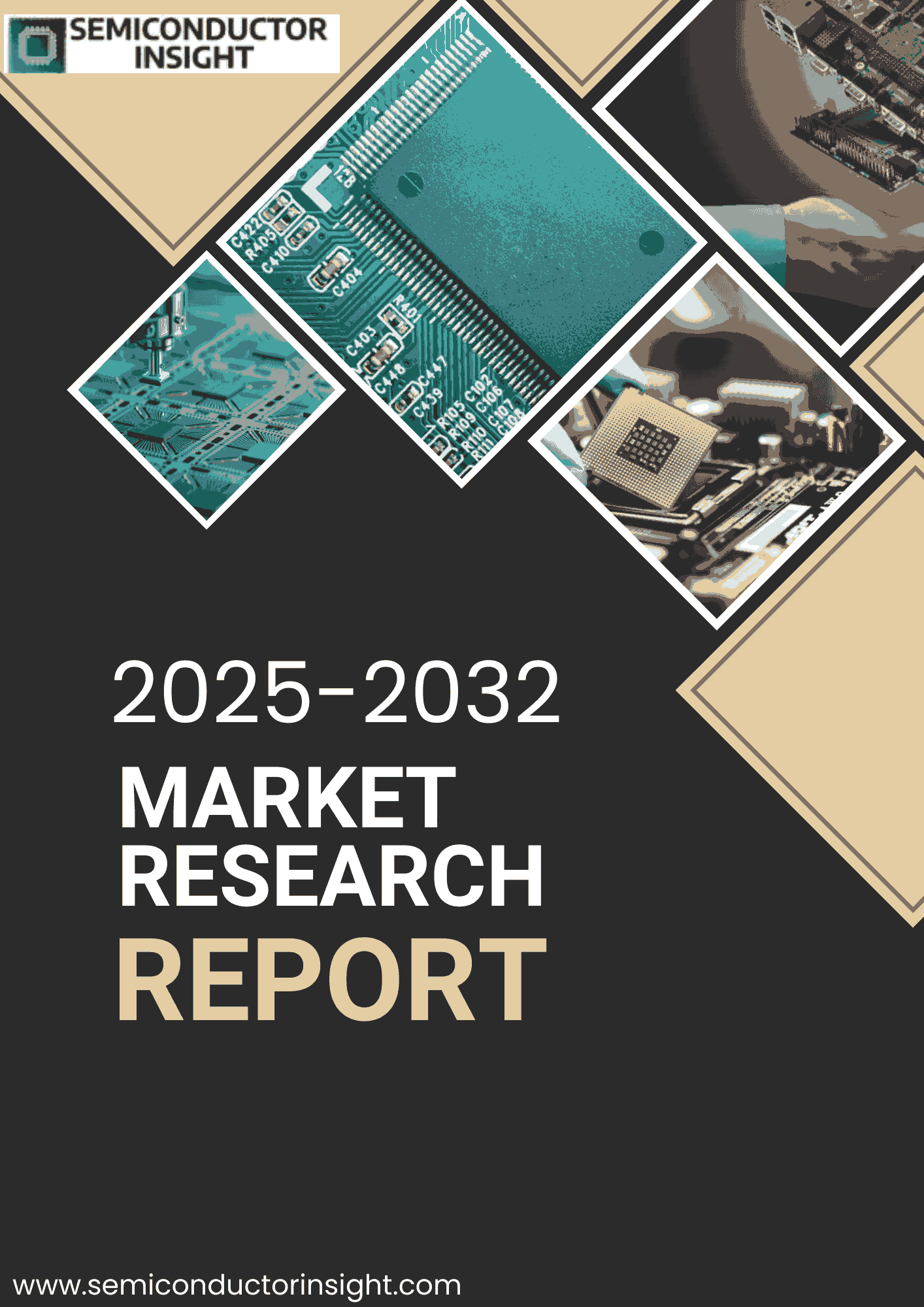
Get Sample Report PDF for Exclusive Insights
Report Sample Includes
- Table of Contents
- List of Tables & Figures
- Charts, Research Methodology, and more...
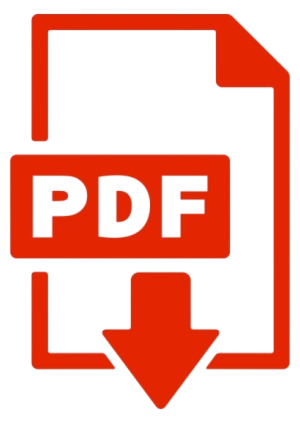