MARKET INSIGHTS
The global Wafer Used PVD Equipment Market size was valued at US$ 7.82 billion in 2024 and is projected to reach US$ 14.67 billion by 2032, at a CAGR of 9.4% during the forecast period 2025-2032.
Wafer used PVD (Physical Vapor Deposition) equipment refers to specialized semiconductor manufacturing systems that deposit thin film materials onto silicon wafers through physical processes like sputtering or evaporation. These systems are critical for creating metal interconnects, barriers, and seed layers in advanced semiconductor fabrication. The equipment includes key variants such as HardMask PVD for dielectric layers, CuBS for copper barrier/seed applications, and AlPAD for aluminum pad deposition.
The market growth is primarily driven by increasing semiconductor demand across consumer electronics, automotive, and IoT applications, coupled with the transition to more advanced nodes requiring complex PVD processes. While the foundry segment dominates current demand due to intensive capacity expansions by major players, the IDM sector is also contributing significantly to market growth. Recent technological advancements in multi-chamber cluster tools and atomic layer deposition (ALD)-PVD hybrid systems are further propelling market expansion. Applied Materials, Ulvac, and KLA Corporation collectively hold over 60% market share, with Chinese manufacturers like NAURA Technology gaining traction through local semiconductor ecosystem development.
MARKET DYNAMICS
MARKET DRIVERS
Surge in Semiconductor Demand Accelerates PVD Equipment Adoption
The global wafer used PVD equipment market is witnessing robust growth, primarily driven by the exponential demand for semiconductors across multiple industries. With the semiconductor market projected to reach over $1 trillion by 2030, manufacturers are aggressively expanding production capacities. The proliferation of 5G networks, IoT devices, and AI applications necessitates advanced chip manufacturing where PVD plays a critical role in deposition processes. As foundries race to meet demand, orders for PVD systems capable of handling 300mm wafers at advanced nodes below 10nm are seeing particular growth.
Technology Node Shrinks Drive Advanced PVD Tool Requirements
As semiconductor manufacturers transition to sub-7nm and below process nodes, traditional deposition methods face physical limitations. This technological imperative is creating demand for next-generation PVD equipment with atomic layer precision. The need for conformal step coverage in high-aspect-ratio structures and precise thickness control below 10 angstroms is pushing equipment vendors to innovate. Major players have recently introduced PVD systems capable of depositing advanced barrier/seed layers for copper interconnects at these cutting-edge nodes, with adoption accelerating across leading foundries.
➤ The transition to extreme ultraviolet (EUV) lithography has further increased the importance of precision PVD processes in back-end-of-line (BEOL) applications.
Government Semiconductor Subsidies Fuel Capital Investments
Government initiatives worldwide are significantly impacting market dynamics. The CHIPS Act in the United States has allocated over $52 billion for domestic semiconductor manufacturing, triggering massive fab construction projects requiring new PVD equipment. Similarly, the European Chips Act and China’s semiconductor self-sufficiency push are driving regional capacity expansions. These geopolitical factors are creating predictable, multi-year demand for wafer processing equipment as new facilities come online and existing fabs undertake capacity upgrades.
MARKET RESTRAINTS
High Capital Costs and Long ROI Periods Deter Smaller Players
The wafer used PVD equipment market faces significant barriers to entry due to the substantial capital investment required. A single advanced PVD system can cost between $5-10 million, with full production clusters reaching $50 million or more. This creates a challenging dynamic for smaller semiconductor manufacturers and research institutions that may lack the financial capacity for such expenditures. The typically long return on investment period of 3-5 years further compounds this challenge, particularly in price-sensitive emerging markets.
Complex Regulatory Landscape Impacts Equipment Deployment
PVD equipment manufacturers navigate a complex web of international regulations governing semiconductor manufacturing. Environmental regulations on chemical usage, safety standards for vacuum systems, and export controls on advanced technologies create deployment challenges. The classification of certain PVD technologies as dual-use items under international trade agreements adds additional compliance burdens, potentially delaying equipment deliveries by several months in some regions.
MARKET CHALLENGES
Materials Innovation Outpaces Equipment Capabilities
The rapid development of new semiconductor materials presents ongoing challenges for PVD equipment vendors. The transition from traditional aluminum and copper interconnects to novel materials like cobalt and ruthenium requires constant equipment adaptation. Each new material system demands extensive process development and qualification, creating bottlenecks in technology adoption cycles. Leading equipment makers must maintain substantial R&D budgets to keep pace with these material innovations while ensuring backward compatibility with existing process flows.
Global Supply Chain Vulnerabilities Impact Delivery Timelines
The PVD equipment market continues to face supply chain disruptions affecting critical components like precision vacuum chambers, power supplies, and wafer handling systems. Lead times for certain specialty components have extended to 12-18 months in some cases, forcing equipment manufacturers to redesign subsystems or seek alternative suppliers. These challenges are particularly acute for cutting-edge systems requiring components with extremely tight specifications that few suppliers can meet.
MARKET OPPORTUNITIES
Emerging Applications in Advanced Packaging Create New Revenue Streams
The growth of heterogeneous integration and advanced packaging technologies presents significant opportunities for PVD equipment vendors. As the semiconductor industry moves toward chiplets and 3D packaging architectures, new deposition requirements are emerging. PVD processes for through-silicon vias (TSVs), redistribution layers, and hybrid bonding interfaces represent a growing market segment. Equipment capable of handling these applications while meeting the stringent particle and uniformity requirements of advanced packaging could capture substantial market share in coming years.
AI-Driven Process Optimization Opens Service Revenue Potential
The integration of artificial intelligence into PVD equipment presents new business model opportunities. Advanced process control systems utilizing machine learning can optimize deposition parameters in real-time, reducing material waste and improving yield. Equipment manufacturers are increasingly offering these capabilities as value-added services, creating recurring revenue streams through predictive maintenance and process optimization subscriptions. This service-oriented approach helps mitigate equipment commoditization while strengthening customer relationships through continuous performance improvement.
GLOBAL WAFER USED PVD EQUIPMENT MARKET TRENDS
Semiconductor Miniaturization and Advanced Node Demand Drive PVD Equipment Adoption
The relentless push toward semiconductor miniaturization, particularly below 7nm nodes, has substantially increased the adoption of wafer used PVD (Physical Vapor Deposition) equipment. As foundries transition to advanced process nodes, the demand for precise thin-film deposition techniques grows exponentially – PVD equipment accounts for nearly 35% of all deposition tools in leading-edge fabrication facilities. The expansion of 3D NAND architectures, where PVD plays a critical role in creating high-aspect-ratio structures, has further amplified equipment sales. Manufacturers are responding with cluster tool configurations that combine multiple process chambers, improving throughput by up to 40% compared to traditional single-chamber systems.
Other Trends
Material Innovations Redefine PVD Requirements
The shift from aluminum to copper interconnects marked just the beginning of material-driven PVD equipment evolution. Emerging applications now demand deposition of novel barrier layers (such as ruthenium and cobalt) and low-resistivity metals, requiring equipment capable of handling high-purity targets and maintaining strict stoichiometric control. The market for advanced HardMask PVD equipment grew by approximately 28% year-over-year, fueled by multi-patterning requirements in logic and memory manufacturing. Equipment capable of depositing ultra-thin films (<10nm) with atomic-level uniformity now captures over 60% of new tool purchases in leading foundries.
Geopolitical Factors Reshape Supply Chain Dynamics
While technological demands drive innovation, geopolitical considerations profoundly impact the wafer PVD equipment landscape. Recent export controls have accelerated domestic equipment development in several regions, with China’s domestic PVD equipment manufacturers capturing nearly 25% of their local market – a five-fold increase from five years prior. This localization trend coincides with increased investment in regional semiconductor ecosystems, with new fab projects driving PVD equipment demand growth projections of 12-15% annually through 2026. However, these dynamics also create supply chain complexities, as equipment manufacturers must now navigate varying regional certification requirements and technology transfer restrictions.
COMPETITIVE LANDSCAPE
Key Industry Players
Technological Innovation and Strategic Investments Drive Market Competition
The global wafer used PVD (Physical Vapor Deposition) equipment market exhibits a moderately consolidated competitive structure, with established semiconductor manufacturing giants dominating revenue shares while emerging players focus on niche applications. Applied Materials leads the sector with an estimated 30% market share in 2024, attributable to its comprehensive Endura® PVD systems portfolio and strong partnerships with leading foundries worldwide. The company’s recent $2.4 billion investment in R&D underscores its commitment to maintaining technological leadership in advanced node wafer processing.
Ulvac and KLA Corporation collectively account for approximately 25% of the market, with their strength lying in specialty PVD solutions for memory and logic applications. Ulvac’s breakthrough in high-power impulse magnetron sputtering (HiPIMS) technology has given it particular advantage in 3D NAND fabrication, while KLA’s acquisition of Orbotech in 2019 significantly expanded its inspection capabilities for PVD processes.
The competitive intensity is increasing as Chinese manufacturers like NAURA Technology capture growing domestic demand, now holding about 15% of the Asia-Pacific market. NAURA’s focus on cost-effective solutions for mature nodes has enabled it to secure contracts with major Chinese foundries, though its technological capabilities still lag behind Western competitors in cutting-edge applications.
Meanwhile, European player Evatec Ltd has differentiated itself through cluster tool architectures for diversified semiconductor applications. Their 2023 partnership with STMicroelectronics to develop specialized PVD solutions for power devices demonstrates how smaller players can compete through application-specific innovation.
List of Key Wafer Used PVD Equipment Companies Profiled
- Applied Materials, Inc. (U.S.)
- Ulvac Technologies, Inc. (Japan)
- KLA Corporation (U.S.)
- NAURA Technology Group Co., Ltd. (China)
- Evatec AG (Switzerland)
- Canon Anelva Corporation (Japan)
- Tokyo Electron Limited (Japan)
- Veeco Instruments Inc. (U.S.)
- Plasma-Therm LLC (U.S.)
Segment Analysis:
By Type
HardMask PVD Equipment Leads the Market Due to High Demand in Advanced Semiconductor Manufacturing
The global wafer used PVD equipment market is segmented based on type into:
- HardMask PVD Equipment
- CuBS PVD Equipment
- AlPAD PVD Equipment
- Others
By Application
Foundry Segment Dominates Owing to Rising Demand for Semiconductor Fabrication Services
The market is segmented based on application into:
- IDM (Integrated Device Manufacturers)
- Foundry
- Others
By Technology
Physical Vapor Deposition Technology Segment Holds Major Share Due to its Superior Film Quality
The market is segmented based on technology into:
- Sputtering
- Evaporation
- Others
By Wafer Size
300mm Wafer Segment Leads with Growing Adoption in High-Volume Production
The market is segmented based on wafer size into:
- 200mm
- 300mm
- Others
Regional Analysis: Global Wafer Used PVD Equipment Market
North America
North America dominates the wafer-used PVD equipment market due to strong semiconductor manufacturing presence and substantial R&D investments. The U.S. hosts major players like Applied Materials, whose advanced PVD systems account for over 30% of the global market share. CHIPS Act funding of $52 billion is accelerating domestic semiconductor production, creating demand for both HardMask and CuBS PVD systems. While the U.S. leads in cutting-edge technology adoption, Canada is emerging as a strategic location for semiconductor packaging facilities, driving demand for AlPAD PVD solutions. Environmental regulations regarding chemical usage in deposition processes pose challenges, but also encourage innovation in eco-friendly PVD technologies.
Europe
Europe maintains a strong position in specialty semiconductor applications, particularly for automotive and industrial IoT chips. The region shows strong preference for precision PVD equipment from EU-based suppliers like Evatec. Germany leads in adoption due to its robust automotive semiconductor sector, while France focuses on research-intensive applications. The EU’s €43 billion Chips Act aims to double Europe’s semiconductor market share by 2030, accelerating PVD equipment investments. However, high operational costs and stringent environmental standards impact equipment pricing structures. Collaborations between academic institutions and equipment manufacturers are driving innovation in low-temperature PVD processes suitable for next-gen flexible electronics.
Asia-Pacific
Asia-Pacific accounts for over 60% of global PVD equipment demand, led by semiconductor powerhouses Taiwan, South Korea, and China. Taiwan’s TSMC and South Korea’s Samsung drive cutting-edge PVD adoption, while China’s rapid expansion in domestic semiconductor production fuels equipment imports. Japan maintains leadership in precision PVD tools through companies like Ulvac. The region’s cost competitiveness has led to increased local manufacturing of PVD components, though core technologies remain imported. Government initiatives like China’s ‘Big Fund’ and India’s semiconductor incentives are creating new growth pockets, though intellectual property concerns persist in certain markets.
South America
South America represents an emerging market with Brazil and Argentina showing gradual semiconductor industry development. Limited local wafer production means most PVD equipment serves packaging and testing applications rather than front-end processes. Economic instability and currency fluctuations hinder large capital investments in advanced PVD systems. However, growing electronics manufacturing in Brazil’s Manaus free trade zone and Argentina’s focus on IoT devices present opportunities for entry-level PVD solutions. The region primarily sources refurbished or older-generation PVD equipment from North American and Asian suppliers due to budget constraints.
Middle East & Africa
The MEA region is witnessing strategic investments in semiconductor infrastructure, particularly in UAE and Saudi Arabia as part of economic diversification plans. While currently a minor market, potential exists for PVD equipment in specialized applications like MEMS sensors and power electronics. Israel’s strong semiconductor design ecosystem creates niche demand for research-grade PVD systems. Africa’s market remains undeveloped outside South Africa’s modest electronics manufacturing base. Regional growth depends on establishing reliable supply chains and developing technical expertise, with most equipment currently imported through partnerships with global distributors.
Report Scope
This market research report provides a comprehensive analysis of the Global and regional Wafer Used PVD Equipment markets, covering the forecast period 2025–2032. It offers detailed insights into market dynamics, technological advancements, competitive landscape, and key trends shaping the industry.
Key focus areas of the report include:
- Market Size & Forecast: Historical data and future projections for revenue, unit shipments, and market value across major regions and segments. The Global Wafer Used PVD Equipment market was valued at USD 3.2 billion in 2024 and is projected to reach USD 5.1 billion by 2032, growing at a CAGR of 6.3%.
- Segmentation Analysis: Detailed breakdown by product type (HardMask PVD, CuBS PVD, AlPAD PVD), technology, application (IDM, Foundry), and end-user industry to identify high-growth segments and investment opportunities.
- Regional Outlook: Insights into market performance across North America, Europe, Asia-Pacific, Latin America, and the Middle East & Africa, including country-level analysis where relevant. Asia-Pacific dominates with 68% market share in 2024.
- Competitive Landscape: Profiles of leading market participants including Applied Materials, Ulvac, KLA Corporation, NAURA Technology, and Evatec, including their product offerings, R&D focus, manufacturing capacity, pricing strategies, and recent developments.
- Technology Trends & Innovation: Assessment of emerging technologies in physical vapor deposition, integration of AI in equipment monitoring, and advancements in thin-film deposition techniques.
- Market Drivers & Restraints: Evaluation of factors driving market growth such as semiconductor industry expansion and increasing wafer sizes, along with challenges like high equipment costs and supply chain constraints.
- Stakeholder Analysis: Insights for semiconductor equipment manufacturers, foundries, IDMs, investors, and policymakers regarding the evolving ecosystem and strategic opportunities.
Primary and secondary research methods are employed, including interviews with industry experts, data from verified sources, and real-time market intelligence to ensure the accuracy and reliability of the insights presented.
FREQUENTLY ASKED QUESTIONS:
What is the current market size of Global Wafer Used PVD Equipment Market?
-> Wafer Used PVD Equipment Market size was valued at US$ 7.82 billion in 2024 and is projected to reach US$ 14.67 billion by 2032, at a CAGR of 9.4% during the forecast period 2025-2032.
Which key companies operate in Global Wafer Used PVD Equipment Market?
-> Key players include Applied Materials, Ulvac, KLA Corporation, NAURA Technology, and Evatec.
What are the key growth drivers?
-> Key growth drivers include expansion of semiconductor manufacturing, transition to larger wafer sizes, and increasing demand for advanced packaging solutions.
Which region dominates the market?
-> Asia-Pacific dominates the market with 68% share, driven by semiconductor manufacturing growth in China, Taiwan, and South Korea.
What are the emerging trends?
-> Emerging trends include development of atomic layer deposition (ALD)-PVD hybrid systems, integration of Industry 4.0 technologies, and increasing automation in wafer processing.
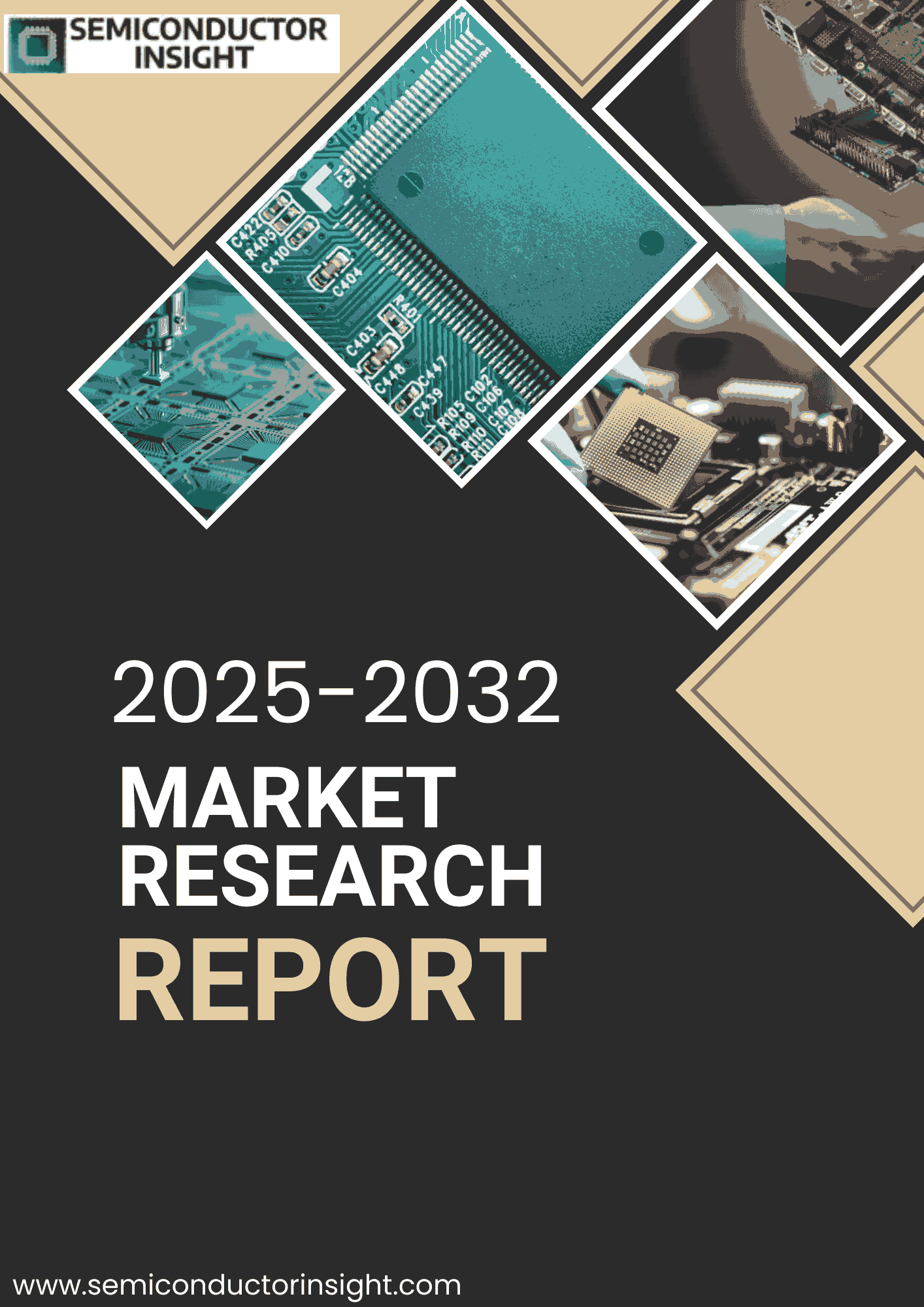
Get Sample Report PDF for Exclusive Insights
Report Sample Includes
- Table of Contents
- List of Tables & Figures
- Charts, Research Methodology, and more...
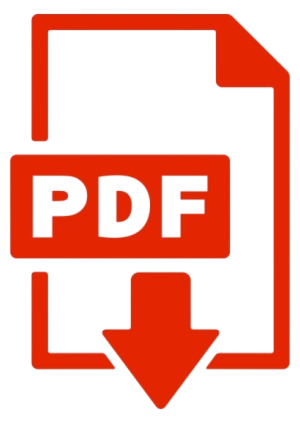