MARKET INSIGHTS
The global Wafer Used Oxidation Equipment Market size was valued at US$ 2.89 billion in 2024 and is projected to reach US$ 5.24 billion by 2032, at a CAGR of 8.8% during the forecast period 2025-2032.
Wafer oxidation equipment is essential for semiconductor manufacturing, creating silicon dioxide layers on silicon wafers through thermal or plasma-enhanced processes. These systems include oxidation/diffusion furnaces, rapid thermal processing (RTP) systems, and gate stack deposition tools. The technology enables precise control over oxide thickness and quality, which is critical for transistor performance in advanced nodes.
Market growth is driven by increasing demand for 5G chips, AI processors, and IoT devices, coupled with expansion of semiconductor fabrication facilities worldwide. Asia-Pacific dominates the market due to concentrated foundry operations, while innovations in high-k dielectric stacks and 3D NAND memory create new opportunities. Key players like Applied Materials and Tokyo Electron are investing in atomic-layer deposition (ALD) capabilities to address scaling challenges below 7nm nodes.
MARKET DYNAMICS
MARKET DRIVERS
Growth in Semiconductor Manufacturing Investments Accelerates Market Demand
The global wafer used oxidation equipment market is experiencing robust growth driven by substantial investments in semiconductor manufacturing facilities worldwide. With the semiconductor industry projected to reach valuations exceeding $1 trillion by 2030, manufacturers are rapidly expanding production capacity. Oxidation remains a critical step in wafer fabrication, creating essential insulating silicon dioxide layers for transistors. Recent developments indicate semiconductor foundries are investing over $200 billion in new fabrication plants across Asia, North America, and Europe between 2021-2025. This unprecedented expansion directly fuels demand for advanced oxidation equipment capable of handling next-generation wafer sizes and tighter process controls.
Transition to Advanced Process Nodes Boosts Equipment Upgrades
The industry’s accelerating transition to sub-7nm process technologies is creating substantial momentum for oxidation equipment replacements. Current industry data shows that approximately 70% of new semiconductor manufacturing capacity being built targets nodes below 10nm. These advanced nodes require oxidation furnaces and rapid thermal processing systems with superior temperature uniformity (±0.1°C) and advanced gas delivery systems to achieve the necessary atomic-level deposition control. Equipment manufacturers are responding with next-generation systems incorporating AI-powered process tuning and self-cleaning mechanisms. For instance, leading foundries have reported oxidation equipment upgrade cycles shrinking from 5-7 years to just 3-4 years to maintain technology leadership.
Government Initiatives Strengthening Domestic Semiconductor Capabilities
National semiconductor self-sufficiency programs are generating significant market uplift across multiple regions. The allocation of over $50 billion in subsidies through programs like the CHIPS Act in manufacturing incentives directly benefits oxidation equipment suppliers. In Asia, similar initiatives have led to the construction of nearly 20 new 300mm wafer fabs in China alone during 2022-2024. These government-backed expansions are prioritizing indigenous equipment procurement where possible, creating opportunities for regional oxidation equipment manufacturers to capture substantial market share previously dominated by international suppliers.
MARKET RESTRAINTS
High Capital Costs Pose Barrier to Market Entry
The wafer used oxidation equipment market faces significant barriers stemming from the specialized nature and substantial capital requirements of these systems. A typical full-configuration vertical oxidation furnace now carries a price tag exceeding $10 million, while advanced RTP systems can reach $15 million. This creates substantial financial hurdles for smaller semiconductor manufacturers considering capacity expansion. Industry analyses indicate that equipment costs have risen approximately 35% since 2018 due to increasing technical complexity and incorporation of advanced automation features.
Other Restraints
Supply Chain Vulnerabilities
The market remains susceptible to extended lead times for critical components like quartz chambers and precision gas delivery systems, with some suppliers reporting lead times stretching to 18 months. This creates operational challenges for equipment manufacturers trying to meet strong foundry demand.
Chip Market Cyclicality
The semiconductor industry’s characteristic boom-bust cycles create uncertainty in capital expenditure planning. Recent downturns have seen foundries delay non-critical equipment purchases by 6-12 months, directly impacting oxidation equipment order flows.
MARKET CHALLENGES
Technical Challenges in Extreme Node Oxidation Processes
The implementation of oxidation processes at advanced nodes below 5nm presents substantial technical hurdles. The need for ultra-thin oxide layers with thickness variation less than 0.05nm across 300mm wafers pushes existing equipment capabilities to their limits. Equipment manufacturers report yield challenges in maintaining process consistency when dealing with novel wafer materials like silicon-germanium and new architectures including gate-all-around transistors. These technical complexities continue to drive extended tool qualification cycles exceeding 9-12 months at leading-edge foundries.
Workforce Shortages Impacting Equipment Innovation
The industry faces growing challenges in attracting and retaining skilled engineers specializing in thermal processing technologies. With semiconductor equipment R&D requiring multidisciplinary expertise in fields ranging from fluid dynamics to advanced materials science, the talent pipeline remains constrained. Several major equipment vendors have reported 30-40% increases in engineering hiring timelines compared to pre-pandemic levels. This talent scarcity directly impacts the pace of next-generation oxidation equipment development and delays commercialization timelines by 6-9 months.
MARKET OPPORTUNITIES
Emerging Memory Technologies Create New Application Frontiers
The rapid development of novel memory architectures presents significant growth opportunities for oxidation equipment manufacturers. Emerging technologies like 3D NAND and MRAM require highly controlled oxidation processes at temperatures ranging from 200-450°C. Market projections indicate demand for specialized low-temperature oxidation systems will grow at 15% CAGR through 2028. Equipment vendors are responding with innovative solutions incorporating atomic layer deposition capabilities to address these emerging applications.
Automation and Industry 4.0 Integration Drives Upgrade Cycle
The integration of advanced automation and Industry 4.0 capabilities into oxidation equipment creates substantial upgrade opportunities. Modern systems incorporating real-time process monitoring and predictive maintenance algorithms can reduce unscheduled downtime by up to 40%. With semiconductor manufacturers prioritizing operational efficiency, over 60% of installed oxidation equipment is expected to undergo automation retrofits or replacements within the next five years. Leading equipment vendors are developing modular upgrade packages specifically targeting legacy system modernization.
Expansion of Specialty Semiconductor Applications
The proliferation of specialty semiconductors for automotive, industrial, and IoT applications creates new growth avenues. These devices often require unique oxidation processes for silicon carbide and gallium nitride substrates that differ substantially from standard silicon processing. Equipment manufacturers developing specialized solutions for these emerging applications are capturing premium pricing and expanded market share in high-growth verticals beyond traditional computing applications.
GLOBAL WAFER USED OXIDATION EQUIPMENT MARKET TRENDS
Semiconductor Industry Expansion Drives Market Growth
The global wafer used oxidation equipment market is experiencing robust growth, primarily fueled by the expanding semiconductor industry which is projected to reach $1.38 trillion by 2029. As chip manufacturers ramp up production to meet demand for advanced electronics, IoT devices, and 5G infrastructure, the need for high-precision oxidation equipment has surged. This equipment plays a critical role in creating silicon dioxide layers essential for semiconductor fabrication. The transition to 300mm and larger wafer sizes across foundries has further amplified the demand for advanced oxidation systems capable of handling these dimensions with superior uniformity and thermal control.
Other Trends
Technology Node Shrink Demands Precision
The semiconductor industry’s relentless pursuit of smaller technology nodes, now moving toward 3nm and below, has necessitated significant advancements in oxidation equipment capabilities. These cutting-edge processes require atomic-level precision in oxide layer formation, driving equipment manufacturers to develop systems with enhanced temperature control and gas flow dynamics. The market has responded with innovations like multi-zone heating and advanced process monitoring, enabling the precise oxide thickness control needed for advanced logic and memory devices.
Alternative Materials and 3D Chip Architectures Create New Demand
The shift toward novel semiconductor materials and 3D chip architectures presents both challenges and opportunities for the oxidation equipment market. As manufacturers adopt high-k dielectric materials and transition to gate-all-around (GAA) transistor structures, oxidation processes must adapt to maintain compatibility with these new material systems. This evolution has led to the development of specialized oxidation equipment capable of handling exotic materials while maintaining the stringent contamination control requirements of modern fabs. Furthermore, the growth of 3D NAND flash memory, which relies heavily on precise oxide-nitride-oxide (ONO) layer deposition, has created additional demand for oxidation systems optimized for high-aspect-ratio structures.
Geopolitical Factors and Supply Chain Diversification
Recent geopolitical tensions and supply chain disruptions have prompted semiconductor manufacturers to rethink their production strategies, leading to increased equipment investments across multiple regions. Governments worldwide are offering substantial subsidies to develop local semiconductor ecosystems, with major investments in new fabrication facilities being announced in North America, Europe, and Asia. This fab expansion wave has created significant opportunities for oxidation equipment vendors, particularly those offering modular, scalable solutions that can support rapid capacity expansion. The market is responding with equipment designs that prioritize ease of installation and quick ramp-up to production volumes, helping manufacturers mitigate supply chain risks while meeting aggressive production timelines.
COMPETITIVE LANDSCAPE
Key Industry Players
Semiconductor Leaders Accelerate Innovation in Wafer Oxidation Technologies
The global wafer used oxidation equipment market features a competitive yet concentrated landscape dominated by established semiconductor capital equipment manufacturers. Applied Materials leads the industry with a significant market share, primarily due to its comprehensive product portfolio in diffusion and thermal processing systems. The company shipped over 1,200 units of oxidation/diffusion furnaces in 2023 alone, reinforcing its dominance in wafer fabrication technology.
Tokyo Electron Limited and ASM International hold robust positions in the market, particularly in rapid thermal processing (RTP) equipment. Their growth stems from continuous R&D investments and strategic collaborations with leading foundries to develop next-generation oxidation solutions. ASM International recently launched its Intrepid Excelis oxidation furnace, achieving 15% better uniformity compared to previous models.
Mid-sized players like Hitachi Kokusai Electric and NAURA Technology are gaining traction through technological differentiation. Hitachi’s vertical batch furnace technology has become particularly popular among Asian semiconductor manufacturers, capturing approximately 18% of the regional market in 2023. Meanwhile, Chinese manufacturer NAURA saw its oxidation equipment revenue grow 27% year-over-year in Q1 2024, benefitting from domestic semiconductor expansion.
Market leaders continue to enhance their positions through:
- Service network expansions in emerging semiconductor hubs
- Development of oxidation solutions for advanced nodes (sub-5nm)
- Integration of AI-driven process control systems
List of Key Wafer Oxidation Equipment Manufacturers
- Applied Materials, Inc. (U.S.)
- Tokyo Electron Limited (Japan)
- Hitachi Kokusai Electric Inc. (Japan)
- ASM International NV (Netherlands)
- Mattson Technology (U.S.)
- SCREEN SPE (Japan)
- NAURA Technology Group Co., Ltd. (China)
- Kokusai Semiconductor Equipment Corporation (Japan)
- Centrotherm International AG (Germany)
Segment Analysis:
By Type
Oxidation/Diffusion Furnace Segment Dominates Due to High Precision in Semiconductor Manufacturing
The wafer oxidation equipment market is segmented based on technology type into:
- Oxidation/Diffusion Furnace
- Rapid Thermal Processing (RTP) Equipment
- Gate Stack Systems
- Others
By Application
Foundry Application Leads Market Due to Expanding Semiconductor Fabrication Demand
The market is segmented based on application into:
- Integrated Device Manufacturers (IDM)
- Foundries
- Research & Development
By Equipment Configuration
Cluster Tool Segment Gains Traction for Multi-Process Integration Capabilities
The market is segmented by equipment configuration into:
- Standalone Systems
- Cluster Tools
- Inline Systems
Regional Analysis: Global Wafer Used Oxidation Equipment Market
North America
The North American wafer used oxidation equipment market is characterized by high technological sophistication and strong semiconductor industry growth. The U.S. accounts for over 60% of regional demand, driven by major semiconductor manufacturers like Intel and GlobalFoundries investing in next-generation fabrication facilities. The CHIPS and Science Act’s $52 billion allocation for domestic semiconductor production is catalyzing equipment upgrades. However, stringent export controls on advanced manufacturing technologies to China are creating supply chain complexities. The region shows preference for advanced oxidation/diffusion furnaces capable of processing 300mm wafers, with foundries representing 68% of equipment demand as of 2023.
Europe
Europe maintains a stable demand for wafer oxidation equipment, supported by the EU’s $46 billion semiconductor subsidy package aimed at doubling the bloc’s global market share to 20% by 2030. Germany dominates equipment procurement, housing essential IDM facilities from Infineon and Bosch. The market prioritizes energy-efficient RTP systems to align with the European Green Deal’s sustainability targets. While Hodgkin’s laws have historically limited wafer production scale, recent easing of state aid rules enables more robust investments in 200mm capacity upgrades. Gate stack oxidation solutions are gaining traction for automotive and industrial IoT applications.
Asia-Pacific
Accounting for 78% of global oxidation equipment installations in 2023, APAC remains the epicenter of wafer fabrication expansion. Taiwan’s TSMC and South Korea’s Samsung drive cutting-edge demand, while China’s SMIC and Hua Hong Semiconductor accelerate mature node capacity. The region consumes 45% of all new Oxidation/Diffusion Furnaces globally. Japan maintains technological leadership in oxidation process control through Tokyo Electron and Hitachi Kokusai innovations. Southeast Asia emerges as a strategic diversification hub, with Malaysia attracting $15 billion in semiconductor investments since 2022. Local equipment makers like NAURA now capture 22% of the domestic Chinese market.
South America
The South American market remains niche but shows gradual growth in 200mm wafer oxidation equipment for analog and power semiconductors. Brazil leads regional demand through CEITEC’s specialized fabrication facility, supplemented by small-scale industrial applications. Economic instability and semiconductor ecosystem fragmentation limit large-scale investments, compelling most foundries to rely on refurbished systems. However, the Argentinian government’s $2.5 billion semiconductor development plan signals growing interest in establishing domestic capabilities.
Middle East & Africa
MEA presents modest but strategic opportunities, primarily through technology transfer partnerships. Saudi Arabia’s Vision 2030 includes semiconductor manufacturing targets, with the $10 billion LEAP development earmarking wafer fab space. Israel’s Tower Semiconductor provides regional technical expertise, though most oxidation equipment serves R&D rather than volume production. Constraints include limited skilled labor and reliance on equipment imports, though Dubai’s silicon oasis initiative aims to build foundational capabilities. The region shows particular interest in legacy node oxidation systems for discrete semiconductors.
Report Scope
This market research report provides a comprehensive analysis of the Global Wafer Used Oxidation Equipment Market, covering the forecast period 2025–2032. It offers detailed insights into market dynamics, technological advancements, competitive landscape, and key trends shaping the semiconductor fabrication equipment industry.
Key focus areas of the report include:
- Market Size & Forecast: Historical data and future projections for revenue, unit shipments, and market value across major regions and segments. The global market was valued at USD 2.8 billion in 2024 with projected CAGR of 6.2% through 2032.
- Segmentation Analysis: Detailed breakdown by equipment type (Oxidation/Diffusion Furnace, RTP, Gate Stack), application (IDM, Foundry), and end-user industry to identify high-growth segments.
- Regional Outlook: Insights into market performance across North America, Europe, Asia-Pacific, Latin America, and Middle East & Africa, with Asia-Pacific accounting for 68% of global demand in 2024.
- Competitive Landscape: Profiles of leading manufacturers including Applied Materials, Tokyo Electron, and ASM International, covering their product portfolios, R&D investments, and strategic partnerships.
- Technology Trends: Analysis of advanced oxidation techniques, integration of Industry 4.0 in semiconductor manufacturing, and emerging materials science applications.
- Market Drivers & Restraints: Evaluation of factors including semiconductor industry growth, wafer size transitions, and geopolitical impacts on equipment supply chains.
- Stakeholder Analysis: Strategic insights for equipment manufacturers, semiconductor foundries, investors, and policymakers regarding technology roadmaps and market opportunities.
The research employs primary interviews with industry leaders and analysis of financial reports from 20+ key players, supplemented by data from semiconductor industry associations and equipment manufacturers’ consortiums.
FREQUENTLY ASKED QUESTIONS:
What is the current market size of Global Wafer Used Oxidation Equipment Market?
-> Wafer Used Oxidation Equipment Market size was valued at US$ 2.89 billion in 2024 and is projected to reach US$ 5.24 billion by 2032, at a CAGR of 8.8% during the forecast period 2025-2032.
Which key companies operate in this market?
-> Dominant players include Applied Materials, Tokyo Electron, Hitachi Kokusai, ASM International, and NAURA Technology.
What are the key growth drivers?
-> Primary drivers are increasing semiconductor demand, transition to 300mm+ wafers, and foundry capacity expansions across Asia.
Which region dominates the market?
-> Asia-Pacific commands 68% market share led by semiconductor hubs in Taiwan, South Korea and China.
What are the emerging technology trends?
-> Key trends include AI-driven process optimization, cluster tool integration, and advanced gate stack technologies for sub-5nm nodes.
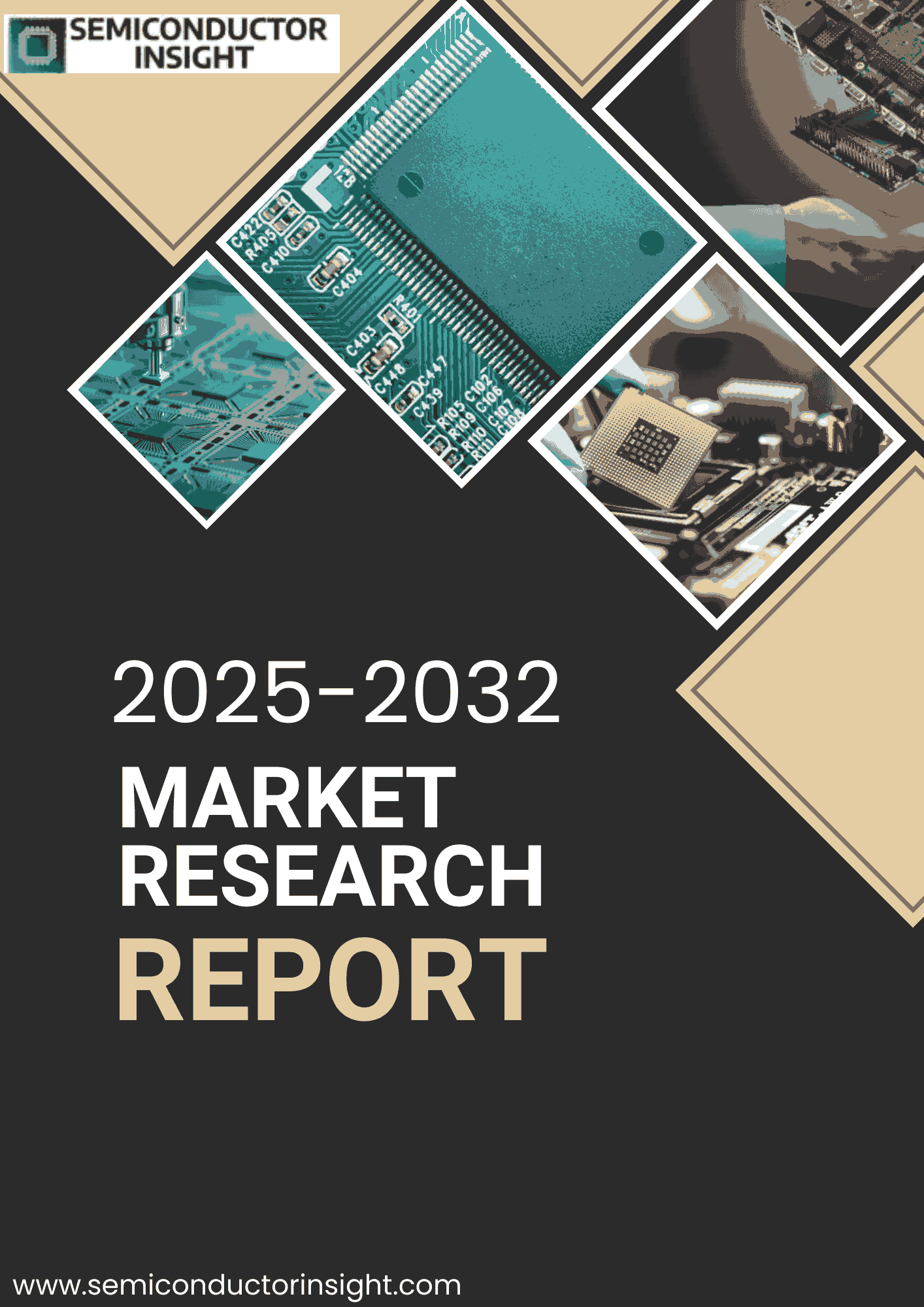
Get Sample Report PDF for Exclusive Insights
Report Sample Includes
- Table of Contents
- List of Tables & Figures
- Charts, Research Methodology, and more...
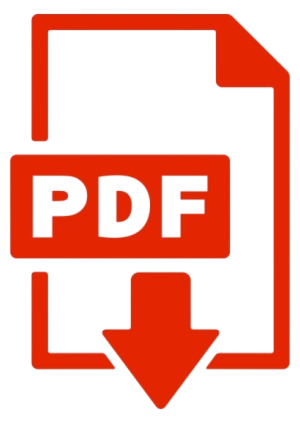