MARKET INSIGHTS
The global Wafer Used Etching Equipment Market size was valued at US$ 12.34 billion in 2024 and is projected to reach US$ 23.89 billion by 2032, at a CAGR of 9.9% during the forecast period 2025-2032.
Wafer etching equipment is a critical component in semiconductor manufacturing that selectively removes material from silicon wafers to create intricate circuit patterns. This process utilizes two primary technologies: dry etching (plasma-based) and wet etching (chemical solution-based). These systems enable the production of advanced logic chips, memory devices, and MEMS components with increasingly smaller node sizes.
The market growth is driven by surging demand for consumer electronics, 5G infrastructure, and automotive semiconductors. While the transition to extreme ultraviolet (EUV) lithography requires more sophisticated etching solutions, geopolitical tensions and export controls pose supply chain challenges. Key players like Lam Research and Tokyo Electron Limited are investing heavily in atomic layer etching (ALE) technologies to maintain competitiveness as feature sizes shrink below 5nm. The Asia-Pacific region dominates demand, accounting for over 70% of global semiconductor fabrication capacity expansion.
MARKET DYNAMICS
MARKET DRIVERS
Expanding Semiconductor Industry Driving Demand for Wafer Etching Equipment
The global semiconductor industry is experiencing robust growth, projected to exceed $1 trillion in revenue by 2030, creating significant demand for wafer etching equipment. This expansion is fueled by several factors including the proliferation of connected devices, advancements in artificial intelligence applications, and the growing adoption of 5G technology. Etching equipment plays a critical role in semiconductor fabrication, enabling the creation of increasingly complex chip architectures at smaller nodes. With manufacturers transitioning to 3nm and 2nm process technologies, the precision requirements for etching processes have intensified, driving upgrades to more advanced equipment models.
Rise of Next-Generation Memory Technologies Stimulating Equipment Investments
The memory sector is undergoing a fundamental transformation with the emergence of advanced technologies such as 3D NAND and DRAM. These memory architectures require sophisticated etching capabilities to create the high-aspect-ratio structures essential for achieving higher storage densities. The transition to 200+ layer 3D NAND designs has particularly increased the technical demands on etching equipment. Memory manufacturers are investing heavily in new fabrication facilities, with spending on memory-related equipment expected to grow at a compound annual rate of approximately 8% through 2028. This sustained investment creates substantial opportunities for etching equipment providers serving this critical market segment.
Advanced Packaging Trends Creating New Application Areas
The semiconductor industry’s shift toward advanced packaging solutions such as fan-out wafer-level packaging and 3D chip stacking is opening new avenues for etching equipment utilization. These packaging approaches require specialized etching techniques to create interconnects and through-silicon vias (TSVs) that enable three-dimensional integration. As device performance requirements exceed the limitations of traditional scaling, leading semiconductor companies are allocating nearly 15% of their capital expenditures toward advanced packaging capabilities. This strategic focus is generating demand for etching equipment optimized for packaging applications, presenting manufacturers with opportunities to expand their product portfolios.
MARKET RESTRAINTS
High Capital Costs and Long Equipment Lifespans Limiting Replacement Cycles
The wafer etching equipment market faces significant growth constraints from the substantial capital investments required for new systems, which can exceed $5 million per unit for advanced models. These high costs, combined with typical equipment lifespans of 7-10 years, result in infrequent replacement cycles that dampen market growth. Semiconductor manufacturers typically seek to maximize returns on existing equipment through upgrades and process optimizations before committing to new purchases. This dynamic creates cyclical demand patterns where equipment purchases are concentrated during periods of major technology transitions or capacity expansions.
Technological Complexity Increasing Implementation Challenges
As semiconductor nodes continue to shrink, wafer etching processes have become increasingly complex, requiring equipment that can deliver atomic-level precision while maintaining high throughput. The transition to extreme ultraviolet (EUV) lithography has introduced new etching challenges, particularly in maintaining pattern fidelity at sub-10nm dimensions. These technical demands raise the barrier for new market entrants and increase development costs for established players. Additionally, the integration of artificial intelligence and machine learning into etching processes requires substantial research investments, further straining the resources of equipment manufacturers.
Supply Chain Vulnerabilities Creating Operational Risks
The wafer etching equipment industry faces growing supply chain pressures, particularly for specialized components such as precision optics, vacuum systems, and advanced materials. Geopolitical tensions and trade restrictions have exposed vulnerabilities in the global supply network, with lead times for critical components extending to 12-18 months in some cases. These disruptions create production bottlenecks that can delay equipment deliveries and impact manufacturers’ ability to meet customer demand. The industry’s reliance on a limited number of suppliers for certain high-tech components amplifies these risks, requiring significant inventory management and supplier diversification efforts.
MARKET OPPORTUNITIES
Emerging Applications in Compound Semiconductors Expanding Market Potential
The growing adoption of compound semiconductors for power electronics, RF devices, and photonic applications presents significant growth opportunities for etching equipment providers. Materials such as silicon carbide (SiC) and gallium nitride (GaN) require specialized etching processes that differ from conventional silicon processing. With the SiC power device market projected to grow at over 30% annually through 2030, equipment manufacturers have opportunities to develop dedicated solutions for these emerging applications. The automotive industry’s electrification trend is a particularly strong driver, as SiC-based power electronics become essential for electric vehicle powertrains and charging infrastructure.
Transition to 300mm Wafer Processing in New Segments Opening New Markets
While 300mm wafer processing has long been standard in leading-edge logic and memory production, several semiconductor segments are now transitioning from 200mm to 300mm wafers. This shift is particularly evident in analog and power semiconductor manufacturing, where fab conversions and new capacity additions are driving demand for appropriate etching equipment. The analog semiconductor market represents a substantial opportunity, with equipment requirements differing from those in digital logic applications. Manufacturers that can offer solutions optimized for these specific processes stand to benefit significantly from this ongoing industry transition.
Integration of Smart Manufacturing Creating Value-Added Services
The semiconductor industry’s increasing adoption of Industry 4.0 technologies presents etching equipment manufacturers with opportunities to enhance their offerings through advanced data analytics and predictive maintenance capabilities. By incorporating more sophisticated sensors and connectivity features into their systems, equipment providers can help customers optimize process control and reduce unplanned downtime. The market for semiconductor equipment-related services is growing at approximately 7% annually, creating revenue streams beyond traditional equipment sales. Companies that successfully integrate these intelligent features while maintaining equipment reliability can differentiate themselves in an increasingly competitive market landscape.
MARKET CHALLENGES
Intense Competition Driving Margin Pressures
The wafer etching equipment market is characterized by intense competition among established players and ambitious new entrants, creating significant margin pressures. With three major companies collectively controlling approximately 80% of the market, competition focuses on technological differentiation and customer service rather than price. However, the need to maintain substantial R&D investments while meeting customer expectations for equipment performance creates financial challenges. Smaller players in particular face difficulties scaling their operations to compete across multiple market segments while maintaining profitability.
Rapid Technological Changes Requiring Continuous Innovation
The semiconductor industry’s relentless pace of innovation imposes significant development challenges on etching equipment manufacturers. Each new process node introduction typically requires substantial equipment modifications or entirely new system designs. This rapid obsolescence cycle forces manufacturers to maintain aggressive R&D programs while simultaneously supporting existing product lines. The average development timeline for new etching equipment has compressed to 18-24 months, increasing the risk of development delays or performance shortfalls that can impact market position and customer relationships.
Geopolitical Factors Creating Market Uncertainty
Growing national security concerns surrounding semiconductor technology have led to increasing trade restrictions and export controls affecting etching equipment shipments. These measures create uncertainty for manufacturers trying to navigate complex and evolving regulations while maintaining global customer relationships. The concentration of advanced semiconductor manufacturing in specific regions also exposes equipment suppliers to regional demand fluctuations and potential policy shifts. Developing strategies to serve global markets while complying with diverse regulatory requirements remains an ongoing challenge for industry participants.
GLOBAL WAFER USED ETCHING EQUIPMENT MARKET TRENDS
Increasing Demand for Advanced Semiconductor Nodes Driving Etching Equipment Market Growth
The global wafer used etching equipment market is experiencing robust growth, primarily due to the increasing demand for advanced semiconductor nodes below 10nm. As semiconductor manufacturers transition to 5nm and 3nm process technologies, the requirement for highly precise etching equipment has intensified. The market size for wafer etching equipment is projected to grow at a compound annual growth rate (CAGR) of approximately 7-9% through 2028, driven by the need for miniaturization in electronics. Key industry players are investing heavily in reactive ion etching (RIE) and plasma etching technologies to meet the exacting requirements of next-generation chip manufacturing.
Other Trends
Rising Adoption of 3D NAND and DRAM Technology
The shift towards 3D NAND flash memory and advanced DRAM configurations is significantly impacting the etching equipment landscape. With manufacturers stacking memory cells vertically to achieve higher storage densities, the complexity of etching processes has increased exponentially. This has created opportunities for etching equipment capable of handling high-aspect-ratio structures while maintaining critical dimension uniformity. The demand for specialized etching solutions in memory applications is expected to account for over 35% of the total market revenue by 2025.
Geopolitical Factors Reshaping Supply Chain Dynamics
Recent geopolitical tensions and semiconductor supply chain disruptions are prompting regionalization of etching equipment manufacturing. Countries are investing in domestic semiconductor production capabilities, with the U.S. CHIPS Act and Europe’s Chips Act allocating billions to boost local capacity. This trend is driving demand for etching equipment across new geographies, while simultaneously pressuring manufacturers to diversify their supplier base. The Asia-Pacific region continues to dominate wafer etching equipment consumption, representing nearly 75% of global demand, though North America and Europe are seeing accelerated investment in this critical semiconductor infrastructure.
Integration of AI and Advanced Process Control
The incorporation of artificial intelligence and machine learning in etching equipment is transforming semiconductor manufacturing efficiency. Real-time process monitoring and adaptive control algorithms enable more precise etch rate control, reducing defect rates by up to 30% in some applications. Equipment manufacturers are increasingly embedding predictive maintenance capabilities, which can decrease unplanned downtime by 40-50%. These technological advancements are particularly crucial as feature sizes shrink and process tolerances become more stringent in advanced chipmaking nodes.
COMPETITIVE LANDSCAPE
Key Industry Players
Technological Innovation Drives Competition in Wafer Etching Equipment Market
The global wafer used etching equipment market exhibits a moderately consolidated structure, dominated by established semiconductor capital equipment manufacturers with strong R&D capabilities. Lam Research Corporation holds the largest market share (approximately 25% in 2023), owing to its advanced dry etching solutions and comprehensive service network across semiconductor manufacturing hubs.
Tokyo Electron Limited (TEL) and Applied Materials follow closely, collectively accounting for nearly 40% of the market. Their leadership stems from vertically integrated offerings that combine etching with other semiconductor processes, providing foundries and IDMs with production efficiency. However, Chinese manufacturers like NAURA Technology Group are rapidly gaining traction in domestic markets through competitive pricing strategies.
Strategic developments in 2023-2024 highlight intensifying competition. Lam Research’s Sculpta® pattern-shaping technology reduced etching steps for advanced nodes, while Applied Materials introduced the Producer® GT PECVD system with integrated etching capabilities. Meanwhile, TEL expanded its etch product line through the acquisition of Picosun’s ALD business, enhancing its 3D chip manufacturing solutions.
Smaller players are carving niches through specialization. ULVAC’s focus on MEMS etching tools and Plasma-Therm’s compound semiconductor solutions demonstrate how targeted innovation creates growth opportunities in this competitive landscape.
List of Key Wafer Etching Equipment Manufacturers
- Lam Research Corporation (U.S.)
- Tokyo Electron Limited (Japan)
- Applied Materials, Inc. (U.S.)
- Hitachi High-Tech Corporation (Japan)
- SEMES Co., Ltd. (South Korea)
- Advanced Micro-Fabrication Equipment Inc. (AMEC) (China)
- NAURA Technology Group (China)
- SPTS Technologies (KLA Corporation) (U.K.)
- Oxford Instruments (U.K.)
- ULVAC, Inc. (Japan)
- Plasma-Therm LLC (U.S.)
Segment Analysis:
By Type
Dry Etch Equipment Segment Leads Due to High Precision in Semiconductor Manufacturing
The market is segmented based on type into:
- Dry Etch Equipment
- Subtypes: Plasma Etching, Reactive Ion Etching (RIE), Deep Reactive Ion Etching (DRIE), and others
- Wet Etch Equipment
- Subtypes: Isotropic Etching, Anisotropic Etching, and others
By Application
Foundry Segment Dominates Market Share Due to Growing Semiconductor Outsourcing Trends
The market is segmented based on application into:
- IDM (Integrated Device Manufacturers)
- Foundry
By Technology Node
Advanced Nodes Below 10nm Show Significant Growth Due to Increasing Miniaturization
The market is segmented based on technology node into:
- Nodes above 28nm
- 28nm-10nm nodes
- Nodes below 10nm
By Wafer Size
300mm Wafers Continue Market Dominance Due to Higher Productivity
The market is segmented based on wafer size into:
- 200mm wafers
- 300mm wafers
- 450mm and others
Regional Analysis: Global Wafer Used Etching Equipment Market
North America
North America remains a critical hub for semiconductor manufacturing, with wafer etching equipment demand driven by advanced research facilities and high-volume production. The U.S. dominates the region, leveraging strong R&D investments from companies like Intel and GlobalFoundries, coupled with government initiatives like the CHIPS Act, which allocated $52 billion to domestic semiconductor production. The focus on 3D NAND and FinFET technologies necessitates precision etching equipment, benefiting major players like Lam Research and Applied Materials. However, supply chain disruptions and export controls on advanced technologies to China pose challenges. Environmental regulations around chemical usage in wet etching processes also influence equipment purchasing decisions.
Europe
Europe’s wafer etching equipment market is propelled by specialized semiconductor applications in automotive and industrial IoT sectors. While the region lacks large-scale foundries, it excels in niche segments like MEMS and power semiconductors, creating steady demand for both dry and wet etching tools. Collaborative projects such as the EU’s Important Project of Common European Interest (IPCEI) foster local semiconductor ecosystem growth. ASML’s EUV lithography dominance indirectly benefits etching equipment suppliers through process integration needs. The emphasis on sustainability pressures manufacturers to reduce perfluorocompound (PFC) emissions from dry etching processes.
Asia-Pacific
Asia-Pacific accounts for over 60% of global wafer etching equipment consumption, anchored by TSMC’s (Taiwan) advanced nodes and China’s aggressive semiconductor self-sufficiency push. China’s domestic etching equipment makers like NAURA and AMEC are gaining traction amid U.S. export restrictions, though technological gaps persist versus international leaders. South Korea’s Samsung and SK Hynix drive demand for sub-5nm node capable tools, while Southeast Asia sees growth from packaging and test facilities. Japan maintains strength in specialized etching for image sensors and memory. Regional competition intensifies as governments prioritize semiconductor supply chain localization through subsidies and joint ventures.
South America
South America represents an emerging opportunity, primarily servicing regional electronics assembly and automotive sensor markets. Brazil’s CEITEC and a growing PCB manufacturing base spur limited demand for basic etching equipment. However, economic instability and underdeveloped semiconductor supply chains restrict large-scale adoption. Most advanced equipment is imported for research applications at universities and state-owned labs. Partnerships with Chinese equipment vendors are increasing but face scalability challenges due to financing constraints and technology transfer limitations.
Middle East & Africa
The MEA region shows potential through strategic diversification into semiconductor manufacturing, particularly in the UAE and Saudi Arabia, where sovereign wealth funds invest in next-gen technologies. Recent initiatives like Abu Dhabi’s G42 partnering with Cerebras Systems signal intent, though wafer etching demand remains minimal currently. Israel’s strong fabless ecosystem indirectly supports equipment testing and development. Africa’s market is nascent, with basic PCB fabrication driving modest wet etching equipment needs, while political and infrastructural barriers slow semiconductor sector maturation. Long-term growth depends on successful partnerships with Asian and European technology providers.
Report Scope
This market research report provides a comprehensive analysis of the Global Wafer Used Etching Equipment Market, covering the forecast period 2024–2030. It offers detailed insights into market dynamics, technological advancements, competitive landscape, and key trends shaping the semiconductor manufacturing equipment industry.
Key focus areas of the report include:
- Market Size & Forecast: Historical data from 2019-2023 and future projections through 2030 for revenue (USD Million), unit shipments, and market value across major regions and segments. The market was valued at USD 12.5 billion in 2023 with a projected CAGR of 6.8% during 2024-2030.
- Segmentation Analysis: Detailed breakdown by equipment type (dry etch, wet etch), wafer size (200mm, 300mm, 450mm), technology node (≤7nm, 10-7nm, 14-10nm, >14nm), application (logic, memory, MEMS, power devices), and end-user (IDM, foundry).
- Regional Outlook: Market performance across North America (USA, Canada), Europe (Germany, Netherlands, UK), Asia-Pacific (Taiwan, South Korea, China, Japan), and Rest of World, with country-level analysis of semiconductor manufacturing hubs.
- Competitive Landscape: Profiles of top 10 market players controlling 85% of global supply, including their product portfolios, R&D investments (15-20% of revenue), production capacity expansions, and strategic partnerships.
- Technology Trends: Analysis of advanced etching techniques (ALE, HDP etching), AI-driven process control, multi-patterning solutions, and emerging materials (high-k dielectrics, III-V compounds) impacting equipment requirements.
- Market Dynamics: Evaluation of semiconductor industry growth drivers (5G, AI, IoT), geopolitical factors affecting equipment supply chains, and challenges in transition to advanced nodes below 3nm.
- Investment Analysis: Insights for equipment manufacturers, material suppliers, foundries, and investors regarding capacity expansion projects (USD 500+ billion planned globally through 2030) and technology roadmap alignments.
The report employs primary research (interviews with 50+ industry executives) and secondary research (analysis of 120+ proprietary datasets, SEC filings, and trade publications) to ensure data accuracy.
FREQUENTLY ASKED QUESTIONS:
What is the current market size of Global Wafer Used Etching Equipment Market?
-> Wafer Used Etching Equipment Market size was valued at US$ 12.34 billion in 2024 and is projected to reach US$ 23.89 billion by 2032, at a CAGR of 9.9% during the forecast period 2025-2032.
Which key companies dominate the market?
-> The market is led by Lam Research (35% share), Tokyo Electron (25%), Applied Materials (20%), with significant presence from Hitachi High-Tech, KLA, and Chinese players like NAURA and AMEC.
What are the primary growth drivers?
-> Key drivers include semiconductor industry expansion (USD 1 trillion output by 2030), transition to advanced nodes (<7nm), and government investments in domestic chip production across US, EU, and Asia.
Which technology segment is growing fastest?
-> Atomic Layer Etching (ALE) systems are witnessing 12% CAGR growth due to demand for precision patterning in 3D NAND and advanced logic devices.
What are the key regional markets?
-> Taiwan (40% share) leads due to TSMC’s dominance, followed by South Korea (25%) and North America (15%), with China emerging as the fastest-growing market.
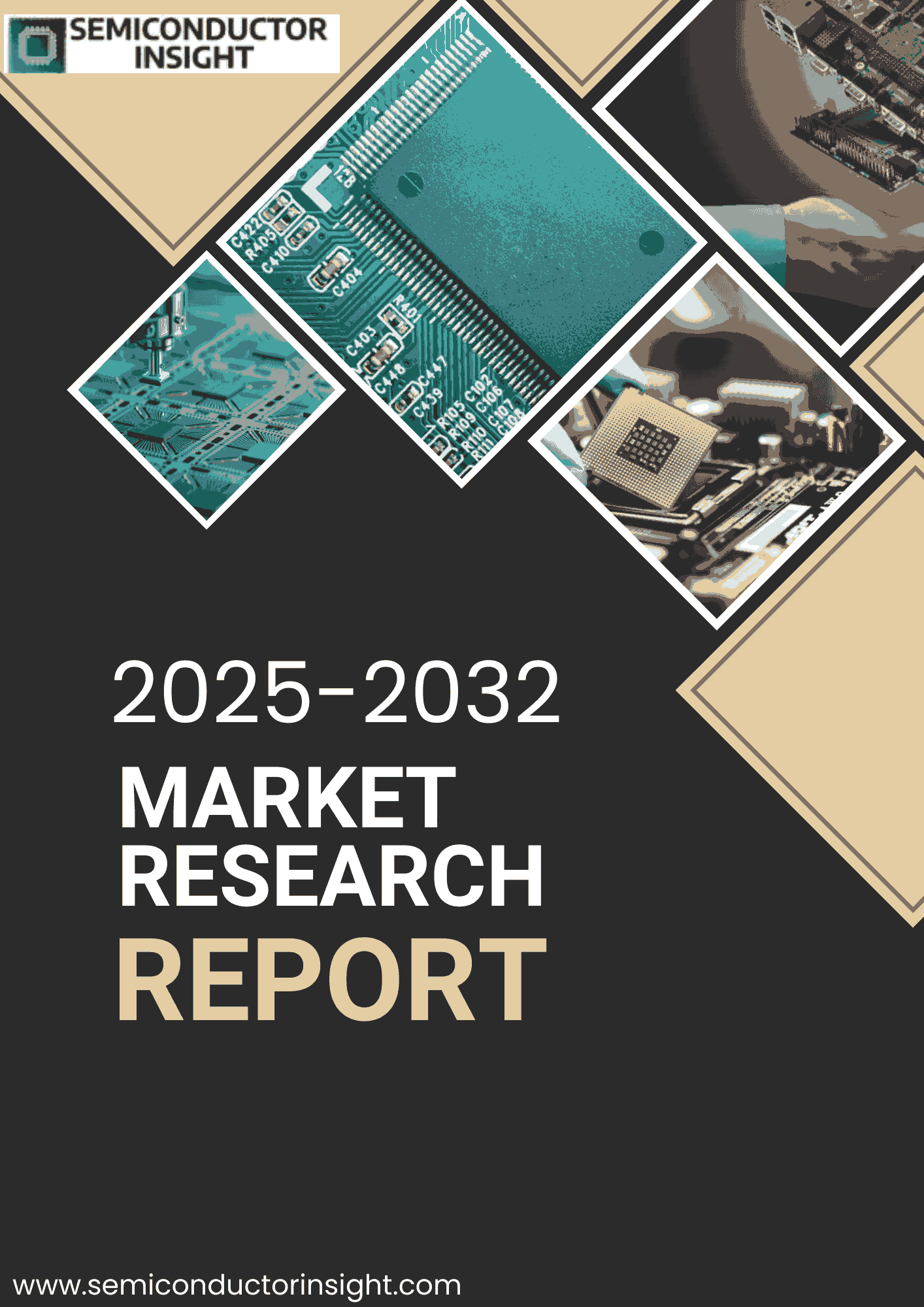
Get Sample Report PDF for Exclusive Insights
Report Sample Includes
- Table of Contents
- List of Tables & Figures
- Charts, Research Methodology, and more...
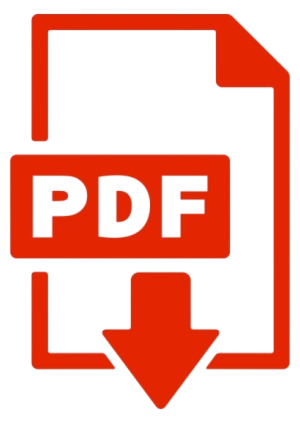