MARKET INSIGHTS
The global Wafer Used Coater and Developer Market size was valued at US$ 4.56 billion in 2024 and is projected to reach US$ 8.17 billion by 2032, at a CAGR of 8.7% during the forecast period 2025-2032. The market growth is primarily driven by increasing semiconductor manufacturing capacity and the rising demand for advanced chip packaging solutions.
Wafer coaters and developers are critical equipment in semiconductor manufacturing that apply photoresist coatings and develop patterns on silicon wafers. These systems are essential for photolithography processes in both front-end (wafer fabrication) and back-end (packaging) semiconductor production. The equipment typically includes spin coaters for uniform resist application, bake plates for curing, and development systems for pattern formation.
While the semiconductor industry continues its expansion, particularly in Asia-Pacific regions, the wafer coater and developer market faces challenges from technological complexities and high capital investment requirements. However, the increasing adoption of 300mm wafer processing and advanced packaging technologies like 3D IC packaging is creating new opportunities. Major players such as Tokyo Electron and SCREEN Semiconductor Solutions are investing in next-generation systems with improved throughput and precision to meet the evolving industry demands.
MARKET DYNAMICS
MARKET DRIVERS
Rising Demand for Advanced Semiconductor Devices Fuels Market Growth
The global wafer used coater and developer market is experiencing significant growth due to escalating demand for advanced semiconductor devices across industries. The semiconductor industry has witnessed a compound annual growth rate exceeding 8% in recent years, driven by the proliferation of IoT devices, 5G technology, and artificial intelligence applications. Coaters and developers play a critical role in photolithography processes, which account for approximately 60% of wafer fabrication stages. As chip manufacturers push for smaller node sizes below 7nm, the precision requirements for coating and developing processes have intensified, creating substantial demand for advanced equipment from leading manufacturers.
Expansion of 300mm Wafer Production Capacity Creates Growth Momentum
300mm wafers now dominate semiconductor manufacturing, representing over 80% of total production capacity, as they offer superior cost efficiency and productivity compared to smaller wafer sizes. Major foundries and IDMs are aggressively expanding their 300mm fabrication facilities, with projected investments surpassing $300 billion globally through 2026. This expansion directly drives demand for 300mm-compatible coaters and developers, as these tools are essential for high-volume manufacturing environments. Recent technological advancements enabling higher throughput and better process control are further accelerating adoption rates across leading semiconductor fabrication plants.
Government Initiatives Supporting Domestic Semiconductor Manufacturing Stimulate Demand
Strategic national policies aimed at strengthening semiconductor supply chains are creating favorable market conditions. Several countries have introduced substantial incentive programs, tax benefits, and funding initiatives to boost local chip production capabilities. These initiatives are leading to the establishment of new wafer fabs and the expansion of existing facilities, which in turn drives investment in critical process equipment like coaters and developers. The combination of geopolitical factors emphasizing supply chain resilience and industry requirements for localized production bases is expected to sustain long-term market growth across multiple regions.
MARKET RESTRAINTS
High Capital Investment Requirements Limit Market Penetration
The wafer coater and developer market faces significant barriers to entry due to the substantial capital investments required for equipment development and manufacturing. Advanced coating systems for cutting-edge nodes can cost upwards of $8 million per unit, while matching developer tools require similar investments. These steep costs create financial hurdles for smaller semiconductor manufacturers and emerging market players, effectively concentrating market opportunities among established foundries and IDMs with substantial capital reserves. The long depreciation cycles of semiconductor equipment, typically spanning 5-7 years, further exacerbate the financial considerations for potential buyers.
Complex Regulatory Environment and Certification Processes Slow Market Expansion
Stringent regulatory requirements and lengthy certification processes pose significant challenges to market participants. Semiconductor manufacturing equipment must meet rigorous standards for process consistency, contamination control, and operational reliability before being certified for production use. The qualification process for new coaters and developers in advanced nodes can extend beyond 12 months, delaying revenue realization for equipment suppliers while increasing their R&D expenditures. Additionally, evolving environmental regulations concerning chemical handling and emissions are forcing manufacturers to implement costly design modifications, further compressing profit margins.
Technical Complexities in Advanced Node Processing Create Adoption Barriers
As semiconductor geometries shrink below 5nm, coating and developing processes face unprecedented technical challenges. Maintaining uniformity across wafers becomes exponentially more difficult at these scales, requiring breakthroughs in fluid dynamics control and chemical formulation compatibility. The industry faces a delicate balance between achieving necessary process precision and maintaining commercially viable throughput rates. These technical hurdles are compounded by the intricate interactions between photoresist chemistries, coating parameters, and developing conditions, often requiring custom solutions for different manufacturers’ process flows.
MARKET CHALLENGES
Supply Chain Disruptions Impact Equipment Production and Delivery Timelines
The wafer coater and developer market continues to grapple with persistent supply chain challenges affecting critical component availability. Specialty materials, precision mechanical components, and advanced sensor systems frequently experience lead time extensions ranging from 6 to 18 months. These disruptions have forced equipment manufacturers to either maintain higher inventory levels, negatively impacting working capital, or delay customer deliveries, potentially risking future orders. The situation is particularly acute for components requiring specialized manufacturing capabilities that cannot be easily duplicated or sourced from alternative suppliers.
Other Challenges
Intellectual Property Protection Concerns
Protracting legal battles over process technology patents have created uncertainty in the marketplace. Several major players have filed infringement claims regarding key coating and developing techniques, leading to prolonged litigation that could ultimately restrict certain process implementations.
Workforce Development and Retention Issues
The industry faces a critical shortage of skilled engineers and technicians capable of designing, operating, and maintaining advanced coaters and developers. This talent gap is further aggravated by intense competition from adjacent technology sectors offering more attractive compensation packages and working conditions.
MARKET OPPORTUNITIES
Emerging Technologies in Advanced Packaging Create New Application Areas
The rapid evolution of advanced packaging techniques presents substantial growth opportunities for coater and developer manufacturers. Heterogeneous integration approaches including chiplet architectures and 3D stacking require novel photolithography solutions that differ from traditional front-end processes. This technological shift is driving demand for specialized coating and developing systems optimized for through-silicon vias (TSVs), redistribution layers, and microbump formation. Market projections indicate that advanced packaging equipment demand could grow at a compound annual rate exceeding 15% through 2030, creating a substantial adjacent market for existing players to explore.
Expansion in Emerging Semiconductor Manufacturing Hubs Offers Geographic Growth Potential
Government-backed initiatives to build semiconductor manufacturing capabilities in new regions are creating fresh market opportunities. Several Southeast Asian countries, Middle Eastern nations, and previously underrepresented markets are making strategic investments to establish domestic chip production capacities. These emerging hubs often prioritize partnerships with experienced equipment suppliers who can provide comprehensive process solutions, presenting established coater and developer manufacturers with avenues for geographic expansion. The ability to offer localized service and support infrastructure will be a key differentiator in securing these new customer relationships.
Integration of AI and Machine Learning Opens Pathways for Equipment Innovation
The incorporation of artificial intelligence into coater and developer systems represents a significant opportunity for product differentiation. Machine learning algorithms can optimize process parameters in real-time, predict maintenance requirements, and detect subtle process variations that might indicate potential yield issues. Early adopters of these intelligent systems have reported improvements in process consistency and equipment uptime exceeding 20%, creating strong value propositions for manufacturers competing in highly demanding fabrication environments. The integration of Industry 4.0 capabilities is increasingly becoming a baseline expectation rather than a premium feature among leading-edge customers.
WAFER USED COATER AND DEVELOPER MARKET TRENDS
Semiconductor Miniaturization Driving Demand for Advanced Coating Technologies
The global wafer used coater and developer market is experiencing significant growth due to the increasing demand for semiconductor miniaturization and higher chip performance. With the semiconductor industry transitioning to 3nm and 2nm process nodes, the precision requirements for photoresist coating and developing equipment have intensified. Leading-edge fabrication facilities now require coaters capable of handling ultrathin uniform resist layers with angstrom-level precision, driving investments in advanced equipment. The market for 300mm wafer processing equipment currently holds over 65% revenue share, reflecting the industry’s focus on cutting-edge manufacturing.
Other Trends
Integration of AI and IoT in Semiconductor Manufacturing
The incorporation of artificial intelligence and IoT technologies in wafer processing equipment is transforming coating and developing systems. Smart coaters now feature real-time viscosity control, predictive maintenance algorithms, and adaptive dispensing systems that optimize chemical usage while minimizing defects. This digital transformation has improved yield rates by approximately 15-20% in advanced packaging applications while reducing photoresist waste. Furthermore, the development of closed-loop systems has enabled tighter process control critical for EUV lithography applications.
Expansion of Compound Semiconductor Manufacturing
Growing adoption of compound semiconductors for 5G, electric vehicles, and photonics is creating new opportunities for specialized coating solutions. While silicon remains dominant, gallium arsenide and silicon carbide wafer processing now accounts for nearly 12-15% of the total coater-developer market. Equipment manufacturers are adapting to the unique requirements of these materials, including higher temperature processing and specialized resist chemistries. The transition to larger 200mm compound semiconductor wafers is particularly driving equipment upgrades across specialty foundries.
Sustainability Initiatives Reshaping Equipment Design
Environmental regulations and corporate sustainability goals are prompting significant changes in coater-developer system designs. New systems now achieve 30-40% reductions in solvent consumption through advanced recycling technologies and water-based resist developments. Equipment manufacturers are also implementing energy recovery systems that capture waste heat from baking processes. These green technologies are becoming critical differentiators, especially in European and North American markets where environmental compliance standards are most stringent.
COMPETITIVE LANDSCAPE
Key Industry Players
Innovation and Precision Drive Market Leadership in Wafer Processing Equipment
The wafer coater and developer market is characterized by a highly consolidated competitive landscape, dominated by a few global semiconductor equipment manufacturers with extensive R&D capabilities. Tokyo Electron Limited (TEL), headquartered in Japan, leads the market with approximately 30% global share in coater/developer systems as of 2023. The company’s dominance stems from its cutting-edge lithography solutions tailored for advanced semiconductor nodes below 7nm.
SCREEN Semiconductor Solutions and SEMES (a subsidiary of Samsung) have significantly strengthened their market positions through technological collaborations with leading foundries. This strategic positioning has allowed them to capture nearly 40% combined market share in the 300mm wafer processing segment. Their growth has been particularly strong in the Asia-Pacific region, where semiconductor manufacturing capacity continues to expand rapidly.
Market leaders are aggressively investing in automation and AI-driven process optimization to maintain their competitive edge. Recent developments include integrated coater-developer-cluster tools that significantly improve throughput for high-volume manufacturing. With the semiconductor industry’s transition to more advanced packaging technologies, companies are also developing specialized coating solutions for wafer-level packaging applications.
Mid-tier players like SUSS MicroTec and Kingsemi are focusing on niche applications and alternative lithography technologies. SUSS has notably gained traction in advanced packaging applications, while Kingsemi has made significant inroads in the Chinese domestic market through competitive pricing and localized service networks.
List of Key Wafer Coater and Developer Companies
- Tokyo Electron Limited (Japan)
- SCREEN Semiconductor Solutions (Japan)
- SEMES (South Korea)
- SUSS MicroTec (Germany)
- Kingsemi (China)
- ASML Holding (Netherlands)
- Applied Materials (U.S.)
- Lam Research (U.S.)
- EV Group (Austria)
Segment Analysis:
By Type
300 mm Wafer Segment Leads Due to High Demand in Advanced Semiconductor Manufacturing
The market is segmented based on type into:
- 300 mm Wafer
- 200 mm Wafer
- Others
By Application
Foundry Segment Dominates with Increased Outsourcing of Semiconductor Production
The market is segmented based on application into:
- IDM (Integrated Device Manufacturers)
- Foundry
By Technology
Photolithography-Compatible Systems Command Majority Share for Precision Patterning
The market is segmented based on technology into:
- Spin Coating
- Spray Coating
- Others
By Automation Level
Semi-Automated Systems Gain Traction in Mid-Scale Fabrication Facilities
The market is segmented based on automation level into:
- Fully Automated
- Semi-Automated
- Manual
Regional Analysis: Global Wafer Used Coater and Developer Market
North America
The North American wafer coater and developer market benefits from strong semiconductor industry investment and technological leadership. With major foundries like Intel expanding production capacity in the U.S. through initiatives like the CHIPS Act, demand for advanced coating and developing equipment remains robust. The region leads in 300mm wafer processing technology adoption, driven by complex chip designs requiring precise photolithography. While labor costs remain high, manufacturers prioritize automation and AI integration in coating/developing systems to maintain competitiveness. Environmental regulations increasingly influence equipment design, particularly around chemical usage and recycling.
Europe
Europe maintains a specialized position in the market, with semiconductor equipment innovation centered in Germany and the Netherlands. The presence of leading lithography companies creates demand for high-precision coaters and developers compatible with EUV systems. European manufacturers emphasize eco-friendly designs aligned with stringent EU regulations on chemical usage and waste management. Though production volumes trail Asia, the region excels in niche applications like MEMS and specialized compound semiconductors. Collaboration between research institutions and equipment suppliers drives continuous process improvements in photoresist application and development.
Asia-Pacific
As the global semiconductor manufacturing hub, Asia-Pacific dominates wafer coater and developer consumption, accounting for over 70% of installations. Taiwan, South Korea, and China lead demand, supported by extensive foundry networks and aggressive capacity expansions. 300mm wafer equipment constitutes the majority of new installations, though 200mm systems still serve legacy applications. Cost competition remains intense, driving equipment innovations that improve yield and throughput. Local manufacturers like Kingsemi continue gaining market share by offering cost-effective solutions tailored for regional foundries. The increasing complexity of advanced packaging technologies creates additional demand for specialized coating/developing systems.
South America
The South American market remains limited but shows potential, primarily serving local electronics assembly needs. Brazil hosts the most significant semiconductor infrastructure, though wafer processing capabilities remain basic. Most coating and developing equipment serves academic and research institutions rather than high-volume production. Economic instability and limited government support for semiconductor manufacturing hinder equipment investment. However, increasing electronics production for automotive and consumer applications may drive future demand for localized wafer processing capabilities.
Middle East & Africa
This region shows nascent development in semiconductor manufacturing equipment adoption. While wafer coaters and developers primarily serve research and small-scale production, strategic investments in technology hubs (particularly in UAE and Saudi Arabia) indicate growing interest in electronics manufacturing. The lack of established semiconductor ecosystems currently limits market penetration by major equipment suppliers. However, partnerships with Asian and European technology providers may accelerate capability development, especially in specialty semiconductor applications relevant to local industries like energy and telecommunications.
Report Scope
This market research report provides a comprehensive analysis of the Global Wafer Used Coater and Developer Market, covering the forecast period 2025–2032. It offers detailed insights into market dynamics, technological advancements, competitive landscape, and key trends shaping the semiconductor equipment industry.
Key focus areas of the report include:
- Market Size & Forecast: Historical data and future projections for revenue, unit shipments, and market value across major regions and segments. The Global Wafer Used Coater and Developer Market was valued at USD 1.2 billion in 2023 and is projected to grow at a CAGR of 6.8% during the forecast period.
- Segmentation Analysis: Detailed breakdown by wafer size (300mm, 200mm, others), application (IDM, Foundry), and technology to identify high-growth segments and investment opportunities.
- Regional Outlook: Insights into market performance across North America, Europe, Asia-Pacific, Latin America, and the Middle East & Africa, with particular focus on semiconductor manufacturing hubs.
- Competitive Landscape: Profiles of leading market participants including Tokyo Electron, SCREEN Semiconductor, SEMES, Suss MicroTec, and Kingsemi, covering their product portfolios, market strategies, and recent developments.
- Technology Trends & Innovation: Assessment of emerging technologies in semiconductor fabrication equipment, including advanced coating techniques, precision development processes, and automation integration.
- Market Drivers & Restraints: Evaluation of factors driving market growth such as semiconductor industry expansion and technological advancements, along with challenges like supply chain constraints and high equipment costs.
- Stakeholder Analysis: Strategic insights for semiconductor equipment manufacturers, foundries, investors, and policymakers regarding market opportunities and competitive positioning.
The report employs both primary and secondary research methodologies, including interviews with industry experts, analysis of financial reports, and validation through multiple data sources to ensure accuracy and reliability.
FREQUENTLY ASKED QUESTIONS:
What is the current market size of Global Wafer Used Coater and Developer Market?
-> Wafer Used Coater and Developer Market size was valued at US$ 4.56 billion in 2024 and is projected to reach US$ 8.17 billion by 2032, at a CAGR of 8.7% during the forecast period 2025-2032.
Which key companies operate in Global Wafer Used Coater and Developer Market?
-> Key players include Tokyo Electron, SCREEN Semiconductor, SEMES, Suss MicroTec, and Kingsemi, with Tokyo Electron holding approximately 35% market share.
What are the key growth drivers?
-> Key growth drivers include increasing semiconductor demand, miniaturization of chips, and expansion of foundry capacity, particularly in advanced nodes below 7nm.
Which region dominates the market?
-> Asia-Pacific dominates the market, accounting for over 70% of global demand, driven by semiconductor manufacturing hubs in Taiwan, South Korea, and China.
What are the emerging trends?
-> Emerging trends include development of multi-layer coating systems, integration of AI for process optimization, and increasing adoption of EUV lithography-compatible coaters/developers.
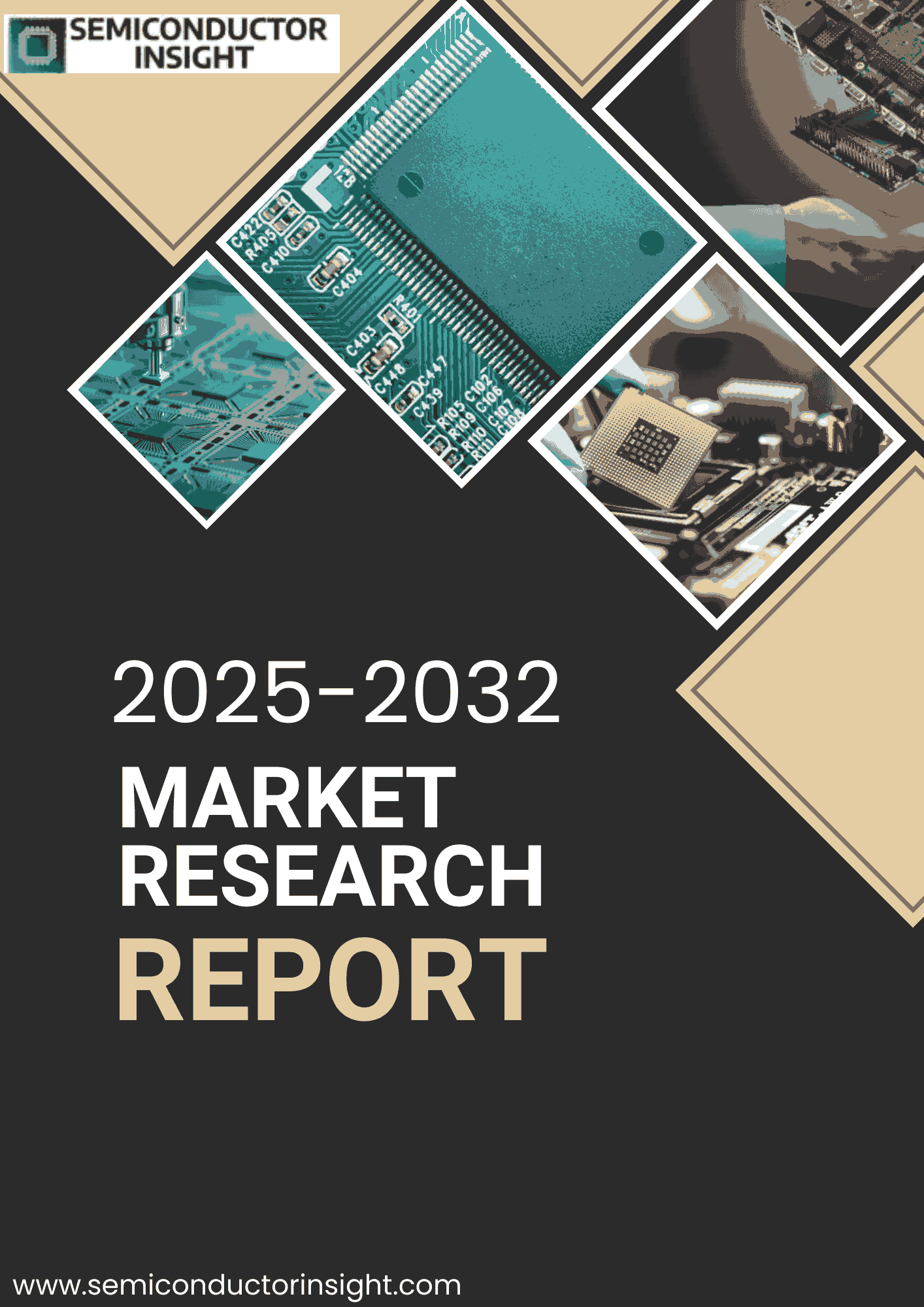
Get Sample Report PDF for Exclusive Insights
Report Sample Includes
- Table of Contents
- List of Tables & Figures
- Charts, Research Methodology, and more...
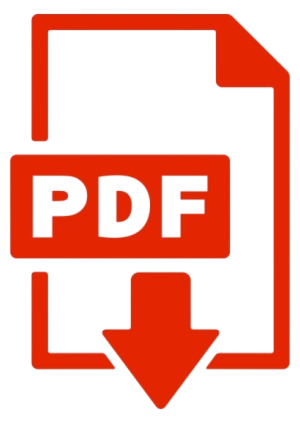