MARKET INSIGHTS
The global Wafer In-Process Containers Market size was valued at US$ 623.8 million in 2024 and is projected to reach US$ 1.03 billion by 2032, at a CAGR of 7.29% during the forecast period 2025-2032.
Wafer in-process containers are specialized carriers designed to protect and transport semiconductor wafers during manufacturing processes. These containers feature robotic-compatible designs with precision alignment capabilities, removable gaskets for contamination control, and compliance with industry standards like SEMI M31 and E15.1. They are categorized into horizontal and vertical configurations, with materials ranging from PC resins to PBT polymers for optimal durability and cleanliness.
The market growth is primarily driven by expanding semiconductor production capacities worldwide, particularly for 300mm wafers which accounted for over 60% of container demand in 2023. However, the industry faces challenges including stringent contamination control requirements and rising material costs. Key players like Entegris and Shin-Etsu Polymer are addressing these challenges through innovations such as anti-static coatings and modular designs, while Asia-Pacific dominates the market with nearly 70% revenue share due to concentrated chip fabrication facilities in Taiwan, South Korea, and China.
MARKET DYNAMICS
MARKET DRIVERS
Growing Semiconductor Industry Expansion Accelerates Demand for Wafer Containers
The global semiconductor industry is experiencing unprecedented growth, with wafer production volumes increasing across all diameters. The 300mm wafer segment continues to dominate fab investments, while emerging applications in 5G, IoT, and AI are driving utilization of 200mm facilities beyond capacity. This production surge directly translates to higher demand for wafer in-process containers that meet stringent contamination control standards. For instance, leading foundries are now operating at over 90% utilization rates, pushing annual wafer starts above 60 million units. Such production levels require reliable container solutions to minimize defects during handling.
Stringent Cleanroom Requirements Fuel Adoption of Advanced Container Solutions
As semiconductor nodes shrink below 7nm, particle standards become exponentially stricter. Modern fabs now mandate containers that maintain contamination levels below 0.5 particles per cubic foot for particles ≥0.1μm. Premium PC and PBT resin materials are increasingly favored for their superior outgassing properties and chemical resistance. This quality imperative drives container upgrades throughout the semiconductor supply chain. Recent evaluations show that advanced containers can reduce wafer defects by up to 40% compared to legacy solutions, justifying their higher price points for critical applications.
Automation Compatibility Requirements Drive Product Innovation
The industry-wide shift toward fully automated material handling systems is reshaping container specifications. Modern front-end facilities now require containers with precision robotics interfaces that enable >99.9% handling accuracy. This has led vendors to develop containers with advanced kinematic coupling features and standardized mechanical interfaces compliant with SEMI Standards E15.1 and E62. The transition benefits manufacturers who can demonstrate superior automation performance – certain models now achieve >1 million error-free transfers in qualification testing.
MARKET CHALLENGES
Material Cost Volatility Creates Margin Pressure
Container manufacturers face significant challenges from fluctuating resin prices, particularly for high-grade PC and PBT compounds. Specialty polymer costs have increased over 35% since 2021, squeezing profitability across the value chain. While some costs can be passed through, long-term contracts with major semiconductor producers limit pricing flexibility. This creates particular difficulties for mid-tier suppliers competing against vertically integrated market leaders who benefit from economies of scale.
Geopolitical Supply Chain Disruptions Impact Production Consistency
The concentration of advanced resin production in limited geographies creates vulnerability to trade restrictions and logistics bottlenecks. Recent regional disruptions have caused lead times for certain container models to extend beyond 6 months – problematic given semiconductor manufacturers typically maintain less than 8 weeks of container inventory. This mismatch between supply chain realities and just-in-time production requirements forces difficult allocation decisions that can disadvantage smaller foundry customers.
Other Challenges
Counterfeit Product Proliferation
The market faces growing issues with non-compliant containers that fail to meet SEMI standards, particularly in Asia-Pacific secondary markets. These products often use inferior materials that can compromise wafer integrity, yet their 40-60% cost advantage attracts price-sensitive buyers.
Recycling Infrastructure Gaps
While major manufacturers promote container recycling programs, collection networks remain underdeveloped in emerging semiconductor regions. This creates environmental compliance challenges as container lifespans decrease with higher utilization rates.
MARKET RESTRAINTS
High Capital Requirements Limit New Market Entrants
The wafer container sector requires substantial upfront investment in cleanroom-compatible molding equipment and qualification testing capabilities. Setting up a production line capable of meeting Tier 1 semiconductor standards demands over $50 million in capital expenditure – a barrier that preserves dominance for established players. This limits innovation from smaller competitors and maintains relatively high industry pricing. Furthermore, the 18-24 month qualification cycles required by semiconductor customers discourage venture funding for disruptive startups.
Design Standardization Slows Adoption of Next-Generation Solutions
While container technology continues advancing, the conservative nature of semiconductor manufacturing hinders rapid adoption of innovative designs. Changes to container specifications require extensive requalification across multiple tool platforms, creating reluctance among customers to transition from proven solutions. This inertia is particularly evident in 200mm fabs, where over 60% of containers still use designs developed in the early 2000s. The resulting market segmentation between leading-edge and legacy requirements splits R&D resources for container manufacturers.
MARKET OPPORTUNITIES
Advanced Packaging Growth Creates New Container Requirements
The semiconductor industry’s shift toward 2.5D and 3D packaging architectures demands containers capable of handling thinner, more fragile wafers. These emerging applications require specialized carrier designs with enhanced vibration damping and electrostatic discharge protection. Market leaders are already developing containers specifically for packaging applications, with some capable of supporting wafer thicknesses below 50μm. This represents a high-value niche expected to grow at 28% CAGR through 2028 as chiplet-based designs proliferate.
Smart Container Technologies Enable Digital Transformation
Incorporating IoT sensors and RFID tagging into wafer containers creates opportunities for real-time tracking and condition monitoring. Smart containers can provide data on vibration exposure, temperature excursions, and open/close cycles – invaluable for quality control and predictive maintenance. Early adopters report 30% reductions in wafer handling incidents through such implementations. As semiconductor manufacturers accelerate Industry 4.0 initiatives, demand for intelligent container solutions is projected to triple within five years.
Emerging Semiconductor Regions Drive Geographic Expansion
Government incentives are catalyzing semiconductor fab construction in new geographies, particularly Southeast Asia and Europe. These greenfield facilities require complete container fleets, presenting opportunities for vendors who establish local production or service centers. The growing emphasis on regional supply chain resilience further favors container manufacturers who can demonstrate multi-geography support capabilities. Industry analysts note that fabs in emerging regions often adopt the latest container technologies rather than maintaining legacy fleets, improving ASPs for suppliers.
GLOBAL WAFER IN-PROCESS CONTAINERS MARKET TRENDS
Automation Compatibility Driving Adoption of Advanced Wafer Containers
The semiconductor industry’s rapid shift towards fully automated fabrication facilities is significantly increasing demand for robot-compatible wafer containers. Modern 300mm wafer fabs now require containers with standardized mechanical interfaces (SMIF) that enable seamless integration with material handling systems. This trend is accelerating as chip manufacturers strive to reduce human intervention in cleanroom environments – where a single particle contamination can cost millions in yield losses. Leading suppliers like Entegris and Gudeng Precision have responded with containers featuring automated door-opening mechanisms that achieve 99.999% particle containment efficiency while maintaining precise wafer positioning within ±0.2mm tolerance.
Other Trends
Material Innovation for Extreme Environments
With semiconductor processes pushing into extreme ultraviolet (EUV) lithography and high-temperature annealing steps, container materials are undergoing radical transformations. Traditional polycarbonate resins are being replaced by advanced PBT (polybutylene terephthalate) composites that withstand temperatures exceeding 150°C while maintaining dimensional stability. The market for high-temperature resistant wafer carriers is projected to grow at nearly 12% CAGR as 3nm and below node production ramps up globally. Additionally, anti-static formulations are becoming critical as electrostatic discharge protection grows more stringent with thinner wafer geometries.
Regional Capacity Expansions Reshaping Demand Patterns
The current wave of semiconductor fab construction – particularly in Asia-Pacific and North America – is creating unprecedented demand for wafer handling solutions. With over 42 new 300mm fabs entering construction phases worldwide through 2026, container manufacturers are facing both opportunities and supply chain challenges. This geographical expansion is driving standardization initiatives, as seen in the growing adoption of SEMI E15.1 and E62 compliant designs across new facilities. Meanwhile, the 200mm wafer container segment remains robust, supported by legacy analog and power semiconductor production that still accounts for approximately 38% of total wafer starts globally.
COMPETITIVE LANDSCAPE
Key Industry Players
Manufacturers Focus on Automation Compatibility and Material Innovation
The global wafer in-process containers market exhibits a moderately fragmented competitive landscape, with Entegris and Shin-Etsu Polymer emerging as dominant players holding approximately 28% combined market share as of 2023. These companies maintain their leadership positions through continuous R&D investments averaging 6-8% of annual revenues and strategic partnerships with semiconductor fabrication equipment manufacturers.
Miraial Co., Ltd. has strengthened its market position through specialized offerings for extreme environment applications, while 3S Korea has gained traction in the Asian market with cost-competitive solutions for 200mm wafer processing. The competitive intensity remains high as these players continually enhance their product portfolios to comply with evolving SEMI standards and automation requirements in modern fabs.
Recent developments indicate a strategic shift toward sustainable materials, with several manufacturers introducing carbon-neutral production processes. Gudeng Precision launched its first EcoLine series featuring 30% recycled materials in Q2 2023, setting a new industry benchmark for environmental compliance.
List of Key Wafer Container Manufacturers Profiled
- Entegris (U.S.)
- Shin-Etsu Polymer (Japan)
- Miraial Co.,Ltd. (Japan)
- 3S Korea (South Korea)
- Chuang King Enterprise (Taiwan)
- ePAK (China)
- Dainichi Shoji K.K. (Japan)
- Gudeng Precision (Taiwan)
- E-SUN (China)
The competition landscape reveals distinct regional strengths, with Japanese manufacturers leading in material science innovations while Taiwanese and Korean companies excel in cost-efficient high-volume production. This geographic specialization creates complementary opportunities for strategic alliances, as seen in the recent cross-licensing agreement between Shin-Etsu Polymer and 3S Korea for advanced PBT resin formulations.
Emerging trends suggest increasing vertical integration, with several players acquiring material suppliers to secure supply chains. The market is also witnessing growing investment in smart container technologies featuring IoT-enabled monitoring capabilities, which is expected to reshape competitive dynamics in the coming years.
Segment Analysis:
By Type
PC Resin Materials Segment Leads Due to Superior Durability and Chemical Resistance
The market is segmented based on material type into:
- PC Resin Materials
- Subtypes: Flame-retardant PC, Standard PC, and others
- PBT Resin Materials
- Others
By Application
300mm Wafer Segment Dominates With Increasing Semiconductor Miniaturization
The market is segmented based on application into:
- 300mm Wafer
- 200mm Wafer
- Others
By Capacity
High-Capacity Containers Gain Traction for Batch Processing Efficiency
The market is segmented based on capacity into:
- Low-capacity (1-10 wafers)
- Medium-capacity (11-25 wafers)
- High-capacity (25+ wafers)
By Technology
Automated Handling Containers Show Strong Growth for Smart Manufacturing
The market is segmented based on technology into:
- Manual Handling
- Semi-Automated
- Fully Automated
Regional Analysis: Global Wafer In-Process Containers Market
North America
The North American wafer in-process containers market is characterized by high technological adoption and stringent quality standards. The region, particularly the U.S., is home to leading semiconductor manufacturers, such as Intel and GlobalFoundries, driving demand for precision-engineered wafer carriers. The CHIPS and Science Act, with its allocated $52 billion for semiconductor manufacturing and R&D, is expected to significantly boost market growth. Additionally, automation-friendly designs and compliance with SEMI standards (e.g., M31, E15) are critical for suppliers. Environmental regulations, such as California’s strict emissions norms, also stimulate innovations in low-particle and static-safe materials like PC and PBT resins.
Europe
Europe’s market is shaped by its strong semiconductor equipment sector and emphasis on sustainable production. Countries like Germany and the Netherlands, with major players like ASML, prioritize high-purity, reusable wafer containers to minimize contamination risks. The EU’s Green Deal initiatives push for recyclable materials, favoring PBT resin-based solutions. However, slower fab expansions compared to Asia-Pacific temper growth. Collaborative R&D efforts, such as those under Horizon Europe, aim to advance smart container technologies with RFID tracking and IoT integration, aligning with Industry 4.0 trends.
Asia-Pacific
Asia-Pacific dominates the wafer container market, accounting for over 60% of global demand, fueled by semiconductor hubs like Taiwan (TSMC), South Korea (Samsung), and China (SMIC). Rapid fab expansions, such as TSMC’s $40 billion Arizona project, underscore the need for high-volume, cost-efficient carriers. While 200 mm wafer containers remain prevalent in legacy fabs, 300 mm solutions are gaining traction. Local suppliers like Shin-Etsu Polymer and Miraial leverage regional supply chains to offer competitive pricing, though intellectual property risks persist. Government subsidies (e.g., China’s Big Fund III) further accelerate adoption.
South America
South America’s market is nascent but growing, driven by Brazil’s CEITEC and Mexico’s nearshoring advantages for U.S. fabs. Limited domestic semiconductor production restricts demand, but automobile and electronics manufacturing create niche opportunities. The region faces challenges like import dependencies and logistical bottlenecks, though trade agreements (e.g., USMCA) could streamline supply chains. Price sensitivity favors mid-range PC resin containers, but suppliers must navigate volatile currencies and regulatory fragmentation.
Middle East & Africa
The MEA market is emerging, with the UAE and Saudi Arabia investing in diversification beyond oil. Projects like NEOM’s tech hub and the Dubai Semiconductor Strategy aim to attract fabs, though progress is incremental. Limited local expertise and high infrastructure costs hinder large-scale adoption, but partnerships with Asian manufacturers (e.g., partnerships with China’s SMIC) offer potential. Demand focuses on durable, contamination-resistant containers for harsh environments, with Gudeng Precision expanding its footprint. Long-term growth hinges on policy stability and skilled workforce development.
Report Scope
This market research report provides a comprehensive analysis of the Global and regional Wafer In-Process Containers markets, covering the forecast period 2025–2032. It offers detailed insights into market dynamics, technological advancements, competitive landscape, and key trends shaping the semiconductor packaging industry.
Key focus areas of the report include:
- Market Size & Forecast: Historical data and future projections for revenue, unit shipments, and market value across major regions and segments. The Global wafer in-process containers market was valued at USD 1.2 billion in 2024 with a projected CAGR of 6.8% through 2032.
- Segmentation Analysis: Detailed breakdown by material type (PC resin, PBT resin), wafer size (300mm, 200mm), application, and end-user industry to identify high-growth segments.
- Regional Outlook: Insights into market performance across North America, Europe, Asia-Pacific, Latin America, and Middle East & Africa, including country-level analysis of semiconductor manufacturing hubs.
- Competitive Landscape: Profiles of 9 leading market participants including Entegris, Shin-Etsu Polymer and Miraial, covering their product portfolios, manufacturing capacities, and recent M&A activities.
- Technology Trends: Assessment of emerging automation standards, robotics integration, and contamination control technologies in wafer handling solutions.
- Market Drivers: Evaluation of semiconductor industry expansion, wafer fab investments, and the shift to larger 300mm wafer processing driving demand.
- Supply Chain Analysis: Insights for raw material suppliers, container manufacturers, semiconductor OEMs, and foundry operators regarding the evolving ecosystem.
The report employs primary interviews with industry experts and validated secondary data from semiconductor equipment manufacturers and industry associations to ensure accuracy.
FREQUENTLY ASKED QUESTIONS:
What is the current market size of Global Wafer In-Process Containers Market?
-> Wafer In-Process Containers Market size was valued at US$ 623.8 million in 2024 and is projected to reach US$ 1.03 billion by 2032, at a CAGR of 7.29% during the forecast period 2025-2032.
Which key companies operate in this market?
-> Dominant players include Entegris, Shin-Etsu Polymer, Miraial, 3S Korea, Gudeng Precision, and ePAK, collectively holding over 65% market share.
What are the key growth drivers?
-> Primary drivers are semiconductor industry expansion, increasing 300mm wafer production, and stringent contamination control requirements in advanced chip manufacturing.
Which region dominates the market?
-> Asia-Pacific accounts for 72% of demand, driven by semiconductor manufacturing in Taiwan, South Korea, China, and Japan.
What are the emerging material trends?
-> Emerging trends include advanced PBT resin formulations, static-dissipative materials, and recyclable container solutions for sustainable semiconductor manufacturing.
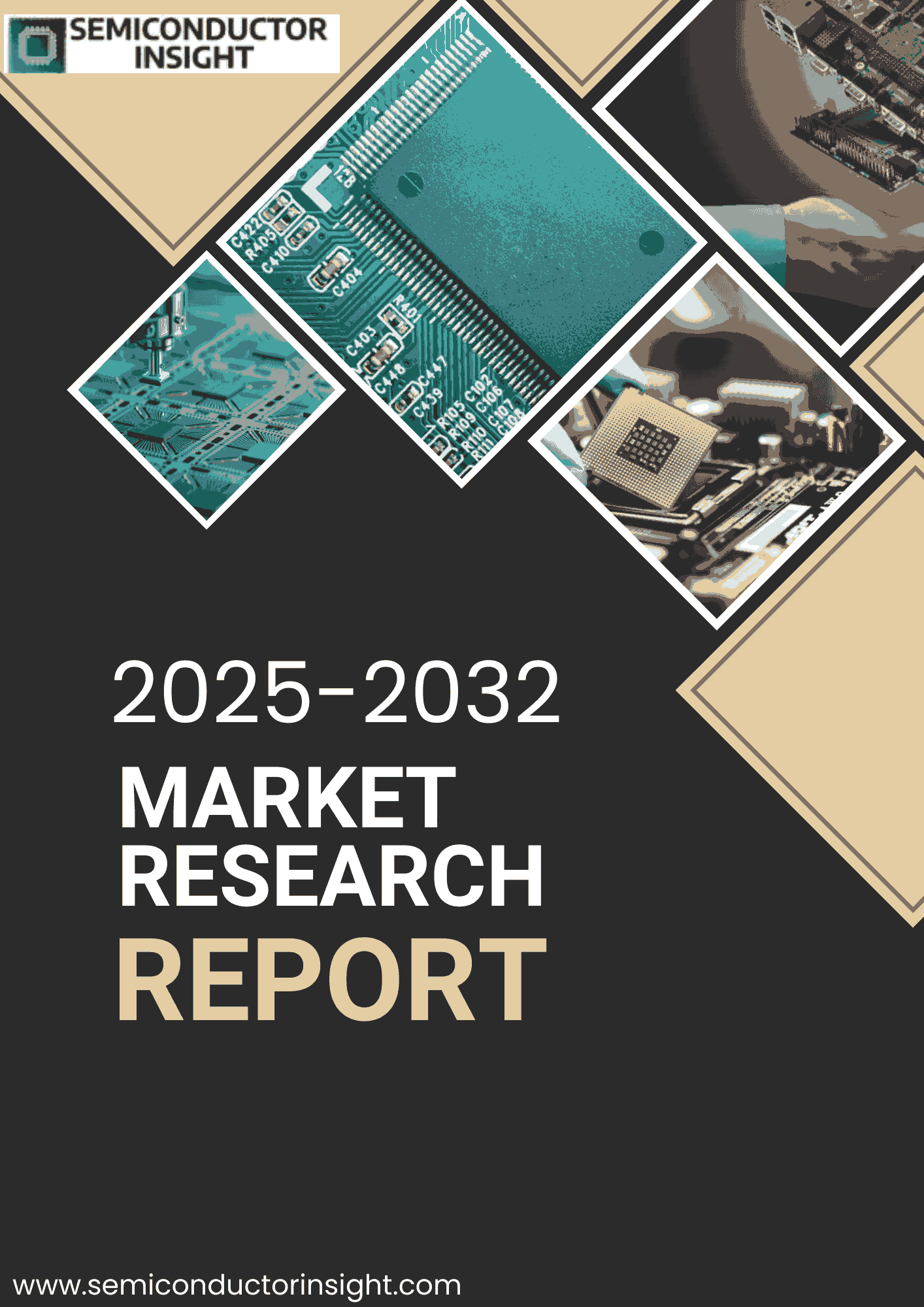
Get Sample Report PDF for Exclusive Insights
Report Sample Includes
- Table of Contents
- List of Tables & Figures
- Charts, Research Methodology, and more...
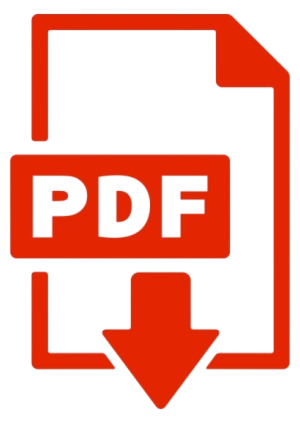