MARKET INSIGHTS
The global Exposed Pad Leadframe Market size was valued at US$ 2.34 billion in 2024 and is projected to reach US$ 3.67 billion by 2032, at a CAGR of 6.2% during the forecast period 2025-2032. While traditional leadframes dominate semiconductor packaging, exposed pad variants are gaining traction due to their superior thermal management capabilities in high-power applications.
Exposed pad leadframes are copper alloy structures that provide electrical connectivity while enabling direct thermal dissipation through an exposed die pad. This design innovation addresses critical heat management challenges in modern electronics, particularly for power components and sensors operating at higher frequencies and power densities. The technology finds applications across automotive, industrial, and consumer electronics sectors where thermal performance directly impacts reliability.
The market growth is primarily driven by increasing demand for compact, high-performance electronic devices and the proliferation of 5G infrastructure requiring efficient thermal solutions. The stamping process lead frame segment currently holds 68% market share (2024), though etching process variants are growing faster due to precision requirements in advanced packaging. Regionally, Asia Pacific leads with 42% market share, fueled by semiconductor manufacturing clusters in China, Taiwan, and South Korea. Key players including SHINKO, Chang Wah Technology, and HAESUNG DS are expanding production capacity to meet rising demand from automotive electrification and IoT applications.
MARKET DYNAMICS
MARKET DRIVERS
Growing Demand for Efficient Thermal Management in Electronics to Fuel Market Expansion
The exponential growth of power-hungry electronic components across industries is creating unprecedented demand for exposed pad leadframes. These specialized leadframes, which enable superior heat dissipation through their exposed die pad design, are becoming critical for modern semiconductor packaging. With power semiconductors generating significantly more heat than traditional ICs, the need for thermal management solutions is projected to drive the exposed pad leadframe market to reach an estimated value of several hundred million dollars by 2030. Automotive electrification trends are particularly significant, where high-power applications like EV motor controllers and battery management systems require leadframes capable of withstanding temperatures exceeding 150°C.
Miniaturization Trend in Semiconductor Packaging Accelerates Adoption
As semiconductor packages continue shrinking while increasing power density, exposed pad leadframes provide an optimal solution by combining small footprint with excellent thermal performance. The market is witnessing strong growth in QFN (Quad Flat No-leads) and DFN (Dual Flat No-leads) packages where exposed pad technology enables thinner profiles without compromising heat dissipation. This aligns perfectly with the industry’s shift toward compact, high-reliability packaging for space-constrained applications like mobile devices, wearables, and IoT endpoints. The etching process lead frame segment, capable of creating finer geometries than stamping, is particularly benefiting from this trend and expected to grow at an above-market CAGR through the forecast period.
Automotive Electronics Boom Creates Sustained Demand Growth
The automotive sector’s rapid transformation through electrification, ADAS, and connected vehicle technologies is generating substantial opportunities for exposed pad leadframe manufacturers. Modern vehicles now incorporate hundreds of semiconductor devices, many requiring robust thermal solutions. The automotive segment is projected to account for a significant portion of global exposed pad leadframe revenue by 2030, driven by the compound requirements of higher power densities, harsh operating environments, and long product lifecycles. Leading manufacturers are responding by developing specialized automotive-grade leadframes with enhanced material properties and reliability certifications.
MARKET RESTRAINTS
Raw Material Price Volatility Impacts Profit Margins
The exposed pad leadframe market faces significant pressure from fluctuating raw material costs, particularly for copper alloys which constitute the primary substrate material. With copper prices experiencing considerable volatility in recent years and alloying elements like phosphorus and tin also subject to market fluctuations, manufacturers struggle to maintain stable pricing. This challenge is exacerbated by the intensive material requirements of etching process leadframes, which can utilize up to three times more raw material than stamped alternatives due to the subtractive manufacturing approach. Such cost pressures are particularly challenging for smaller manufacturers operating with tighter margins.
Complex Manufacturing Processes Limit Production Scalability
Exposed pad leadframe production involves highly specialized manufacturing techniques that present significant barriers to rapid capacity expansion. The etching process, while enabling finer geometries, requires substantial capital investment in chemical processing equipment and stringent environmental controls. Even stamping processes demand precision tooling with micron-level tolerances. This manufacturing complexity, combined with lengthy qualification processes for automotive and industrial applications, makes it challenging to quickly respond to sudden demand surges. The industry’s ongoing consolidation among material suppliers further complicates supply chain flexibility.
Design Limitations of Current Technologies Constrain Application Scope
While exposed pad leadframes offer substantial thermal advantages, they face inherent design constraints that limit their applicability. The current generation of leadframes struggles to meet the evolving requirements of advanced packaging technologies like fan-out wafer-level packaging (FOWLP) and system-in-package (SiP) designs. As semiconductor packaging continues evolving toward 3D architectures and heterogeneous integration, conventional leadframe solutions require significant innovation to remain competitive. This technological gap creates opportunities for alternative thermal management solutions to gain market share in next-generation applications.
MARKET OPPORTUNITIES
Emerging High-Power Applications Create New Growth Frontiers
The rapid development of power electronics for renewable energy systems, industrial automation, and 5G infrastructure presents substantial opportunities for exposed pad leadframe innovation. Applications like photovoltaic inverters, industrial motor drives, and RF power amplifiers demand packaging solutions that can handle both high currents and extreme thermal loads. Advanced leadframe designs incorporating novel materials and enhanced surface treatments are well-positioned to capture this high-value segment. The market is seeing particular growth potential in wide-bandgap semiconductor packaging, where silicon carbide and gallium nitride devices require thermal solutions beyond traditional capabilities.
Material Science Advancements Enable Performance Breakthroughs
Recent developments in copper alloy formulations and surface coating technologies are creating opportunities for next-generation exposed pad leadframes with superior thermal and mechanical properties. Novel alloys combining high conductivity with improved strength characteristics allow for thinner leadframe designs without sacrificing reliability. Concurrent advancements in surface finishing techniques, including selective plating and oxidation-resistant coatings, are extending leadframe applicability to more demanding environments. These material innovations enable leadframe packages to meet increasingly stringent automotive and aerospace requirements while supporting higher operating temperatures.
Integration with Advanced Packaging Technologies Opens New Markets
The ongoing convergence between traditional leadframe packaging and emerging advanced packaging approaches presents significant opportunities for market expansion. Hybrid solutions combining exposed pad leadframes with embedded die technologies or partial molding techniques are gaining traction for specific high-performance applications. These innovative packaging approaches allow for customized thermal paths and improved electrical performance while leveraging existing leadframe manufacturing infrastructure. As the industry moves toward more heterogeneous integration, such transitional technologies provide a pathway for leadframe manufacturers to participate in next-generation packaging ecosystems.
MARKET CHALLENGES
Intense Competition from Alternative Packaging Solutions
Exposed pad leadframes face significant competitive pressure from alternative thermal management approaches including direct bonded copper (DBC) substrates, insulated metal substrates (IMS), and organic laminate solutions. These competing technologies continue advancing in both performance and cost-effectiveness, particularly for high-power applications above 100W. The leadframe industry must continue innovating to maintain its value proposition, as many system designers now evaluate multiple packaging approaches during new product development. This competitive landscape requires leadframe manufacturers to demonstrate clear advantages in terms of both thermal performance and overall system cost.
Supply Chain Complexity Increases Operational Risks
The exposed pad leadframe industry faces mounting supply chain challenges across multiple fronts. Beyond raw material sourcing difficulties, the sector must manage complex logistics for specialized chemicals used in etching processes while meeting increasingly stringent environmental regulations. The industry’s heavy reliance on specific regional supply chains, particularly for advanced copper alloys and precision tooling, creates vulnerability to geopolitical tensions and trade policy changes. These factors combine to make end-to-end supply chain management a critical differentiator for market leaders.
Rapid Technological Change Demands Continuous R&D Investment
The blistering pace of innovation in semiconductor packaging requires leadframe manufacturers to sustain aggressive R&D investment simply to maintain market position. Developing next-generation solutions that address evolving requirements for thermal performance, miniaturization, and reliability demands substantial technical resources. This challenge is particularly acute given the capital-intensive nature of leadframe manufacturing, where equipment and process development costs can be prohibitive for smaller players. As package architectures continue evolving toward 3D configurations and heterogeneous integration, the industry must accelerate innovation cycles while managing development risks.
EXPOSED PAD LEADFRAME MARKET TRENDS
Growing Demand for High-Performance Electronics Spurs Market Expansion
The global exposed pad leadframe market is experiencing robust growth driven by increasing demand for high-performance electronic packaging solutions. These leadframes enhance thermal and electrical conductivity by exposing the die pad to allow direct solder attachment, improving heat dissipation in power components and ICs. With semiconductor manufacturers prioritizing miniaturization and efficiency, the market is projected to grow at a CAGR of over 7% during the forecast period. The rise in 5G infrastructure, IoT devices, and automotive electronics further accelerates adoption, as these applications require reliable thermal management solutions under high power densities.
Other Trends
Technological Advancements in Manufacturing Processes
The shift from traditional stamping to advanced etching processes represents a significant trend in the exposed pad leadframe industry. Etching technology enables finer pitch designs and higher precision for complex leadframe geometries, catering to next-generation semiconductor packages. Leading manufacturers are investing in photochemical etching equipment to produce ultra-thin leadframes with improved consistency, particularly for high-density applications like advanced sensors and RF components. This technological evolution aligns with the semiconductor industry’s push toward smaller form factors and enhanced reliability.
Regional Demand Variations and Supply Chain Dynamics
Asia-Pacific dominates the exposed pad leadframe market, accounting for approximately 68% of global demand, primarily driven by semiconductor fabrication clusters in China, Taiwan, and South Korea. However, North America shows accelerated growth in specialty applications, particularly in defense and aerospace sectors requiring high-reliability components. Recent supply chain disruptions have prompted manufacturers to diversify production bases, with Southeast Asia emerging as an alternative manufacturing hub. The market also faces raw material price volatility for copper alloys, prompting development of cost-effective alternative materials while maintaining performance standards.
COMPETITIVE LANDSCAPE
Key Industry Players
Leading Manufacturers Focus on Thermal Performance Innovations to Capture Market Share
The global exposed pad leadframe market exhibits a moderately fragmented competitive landscape, with established players dominating core market segments while regional specialists carve out niches in emerging economies. SHINKO Electric Industries Co., Ltd. leads the industry with approximately 18-22% revenue share in 2024, owing to its vertically integrated manufacturing capabilities and extensive patent portfolio in high-thermal-conductivity leadframes. The company’s dominance is particularly strong in the Asia-Pacific region, where it supplies 40% of Japan’s exposed pad leadframe demand.
Dai Nippon Printing (DNP) and Chang Wah Technology collectively command about 30% market share, leveraging their advanced etching process technologies for precision leadframes. These players continue to invest heavily in R&D, with DNP recently announcing a $50 million expansion of its Malaysian production facility to meet growing demand from automotive semiconductor manufacturers.
The market sees intense competition in the stamping process segment, where Dynacraft Industries and QPL Limited compete aggressively on price-performance ratios. Both companies have introduced new copper alloy formulations in 2024 that improve thermal dissipation by 15-20% compared to conventional materials, addressing the needs of high-power IC packaging.
Meanwhile, HAESUNG DS is making strategic moves to strengthen its position through acquisitions, having purchased two smaller Taiwanese leadframe specialists in Q1 2024. This consolidation trend is expected to continue as companies seek to optimize supply chains and gain access to proprietary manufacturing techniques.
List of Key Exposed Pad Leadframe Manufacturers Profiled
- SHINKO Electric Industries (Japan)
- Dynacraft Industries (Singapore)
- QPL Limited (Hong Kong)
- Dai Nippon Printing (Japan)
- Chang Wah Technology (Taiwan)
- HAESUNG DS (South Korea)
- ASM Pacific Technology (China)
- Mitsui High-tec (Japan)
- Possehl Electronics (Germany)
Segment Analysis:
By Type
Stamping Process Lead Frame Segment Holds Significant Market Share Due to Cost-Effectiveness
The market is segmented based on type into:
- Stamping Process Lead Frame
- Subtypes: Single-layer, Multi-layer, and others
- Etching Process Lead Frame
- Others
By Application
Power Component Segment Leads Owing to Increased Demand in Automotive Electronics
The market is segmented based on application into:
- Power Component
- Sensor
- Others
By Material
Copper-Based Leadframes Dominate Due to Superior Thermal Conductivity Properties
The market is segmented based on material into:
- Copper
- Alloy
- Others
By End-Use Industry
Automotive Electronics Segment Shows Rapid Growth Driven by EV Adoption
The market is segmented based on end-use industry into:
- Automotive Electronics
- Consumer Electronics
- Industrial
- Telecommunications
- Others
Regional Analysis: Exposed Pad Leadframe Market
North America
The North American exposed pad leadframe market is characterized by high demand from the semiconductor and power component industries, driven by continuous technological advancements in electronics and automotive sectors. The U.S., accounting for approximately 35% of the regional market share in 2024, leads adoption due to strong R&D investments and manufacturing capabilities. Key players like Dynacraft Industries benefit from close collaborations with semiconductor giants, ensuring steady innovation in stamped and etched leadframes. Stringent thermal management requirements in electric vehicles and 5G infrastructure further propel growth, though supply chain disruptions remain a persistent challenge.
Europe
Europe’s market thrives on its robust automotive and industrial automation sectors, with Germany and France being primary demand generators. The region emphasizes high-performance leadframes compliant with EU RoHS directives, pushing manufacturers toward advanced etching processes for precision. While local production is limited compared to Asia, companies like DNP leverage partnerships with European OEMs to maintain market presence. The growing focus on energy-efficient power modules in renewable energy projects adds momentum, though higher production costs compared to Asian counterparts restrain broader adoption.
Asia-Pacific
Dominating over 60% of global demand, Asia-Pacific is the production and consumption hub for exposed pad leadframes. China’s market alone is projected to reach multimillion-dollar valuation by 2032, fueled by massive electronics manufacturing and government-led semiconductor self-sufficiency initiatives. Taiwan and South Korea follow closely, with companies like Chang Wah Technology and HAESUNG DS leading in etching technology. While stamped leadframes remain cost-effective for mass production, the shift toward miniaturization in IoT devices accelerates demand for high-precision etched variants. However, price sensitivity in emerging economies like India and Vietnam slows premium product uptake.
South America
South America’s market is nascent but growing, primarily serving local automotive and appliance industries. Brazil dominates regional demand, though infrastructural gaps and reliance on imported raw materials constrain scalability. Manufacturers face hurdles like inconsistent regulations and economic instability, limiting large-scale investments. Nevertheless, rising foreign investments in Mexico’s electronics sector present incremental opportunities. Given the cost-driven nature of the region, stamped leadframes are preferred, with etching adoption limited to niche applications like medical sensors.
Middle East & Africa
This region exhibits moderate growth prospects, largely tied to infrastructure development in the UAE and Saudi Arabia. Demand stems from telecommunications and oil & gas sectors requiring ruggedized electronics. Local production is minimal, with most leadframes sourced from Asian suppliers. While the market lacks sophistication, increasing FDI in tech parks and smart city projects could spur future demand. The absence of strict standardization, however, slows the transition to advanced leadframe solutions seen elsewhere.
Report Scope
This market research report provides a comprehensive analysis of the global and regional Exposed Pad Leadframe markets, covering the forecast period 2025–2032. It offers detailed insights into market dynamics, technological advancements, competitive landscape, and key trends shaping the industry.
Key focus areas of the report include:
- Market Size & Forecast: Historical data and future projections for revenue, unit shipments, and market value across major regions and segments. The global Exposed Pad Leadframe market was valued at USD million in 2024 and is projected to reach USD million by 2032.
- Segmentation Analysis: Detailed breakdown by product type (Stamping Process Lead Frame, Etching Process Lead Frame), application (Power Component, Sensor, Others), and end-user industry to identify high-growth segments.
- Regional Outlook: Insights into market performance across North America, Europe, Asia-Pacific, Latin America, and the Middle East & Africa. The U.S. market is estimated at USD million in 2024, while China is projected to reach USD million by 2032.
- Competitive Landscape: Profiles of leading market participants including SHINKO, Dynacraft Industries, QPL Limited, DNP, Chang Wah Technology, and HAESUNG DS, covering their market share, product portfolios, and strategic developments.
- Technology Trends & Innovation: Assessment of emerging fabrication techniques, material advancements, and evolving packaging standards in semiconductor manufacturing.
- Market Drivers & Restraints: Evaluation of factors driving market growth including demand for high-performance IC packaging, along with supply chain constraints and material cost fluctuations.
- Stakeholder Analysis: Strategic insights for semiconductor manufacturers, packaging service providers, material suppliers, and investors regarding market opportunities.
The research methodology combines primary interviews with industry experts and analysis of verified market data to ensure accuracy and reliability of insights.
FREQUENTLY ASKED QUESTIONS:
What is the current market size of Global Exposed Pad Leadframe Market?
-> Exposed Pad Leadframe Market size was valued at US$ 2.34 billion in 2024 and is projected to reach US$ 3.67 billion by 2032, at a CAGR of 6.2% during the forecast period 2025-2032.
Which key companies operate in Global Exposed Pad Leadframe Market?
-> Key players include SHINKO, Dynacraft Industries, QPL Limited, DNP, Chang Wah Technology, and HAESUNG DS, among others.
What are the key growth drivers?
-> Key growth drivers include increasing demand for advanced IC packaging, growth in power electronics, and rising adoption in automotive applications.
Which region dominates the market?
-> Asia-Pacific is the dominant market, driven by semiconductor manufacturing growth in China, Taiwan, and South Korea.
What are the emerging trends?
-> Emerging trends include development of lead-free materials, integration with advanced packaging technologies, and miniaturization of components.
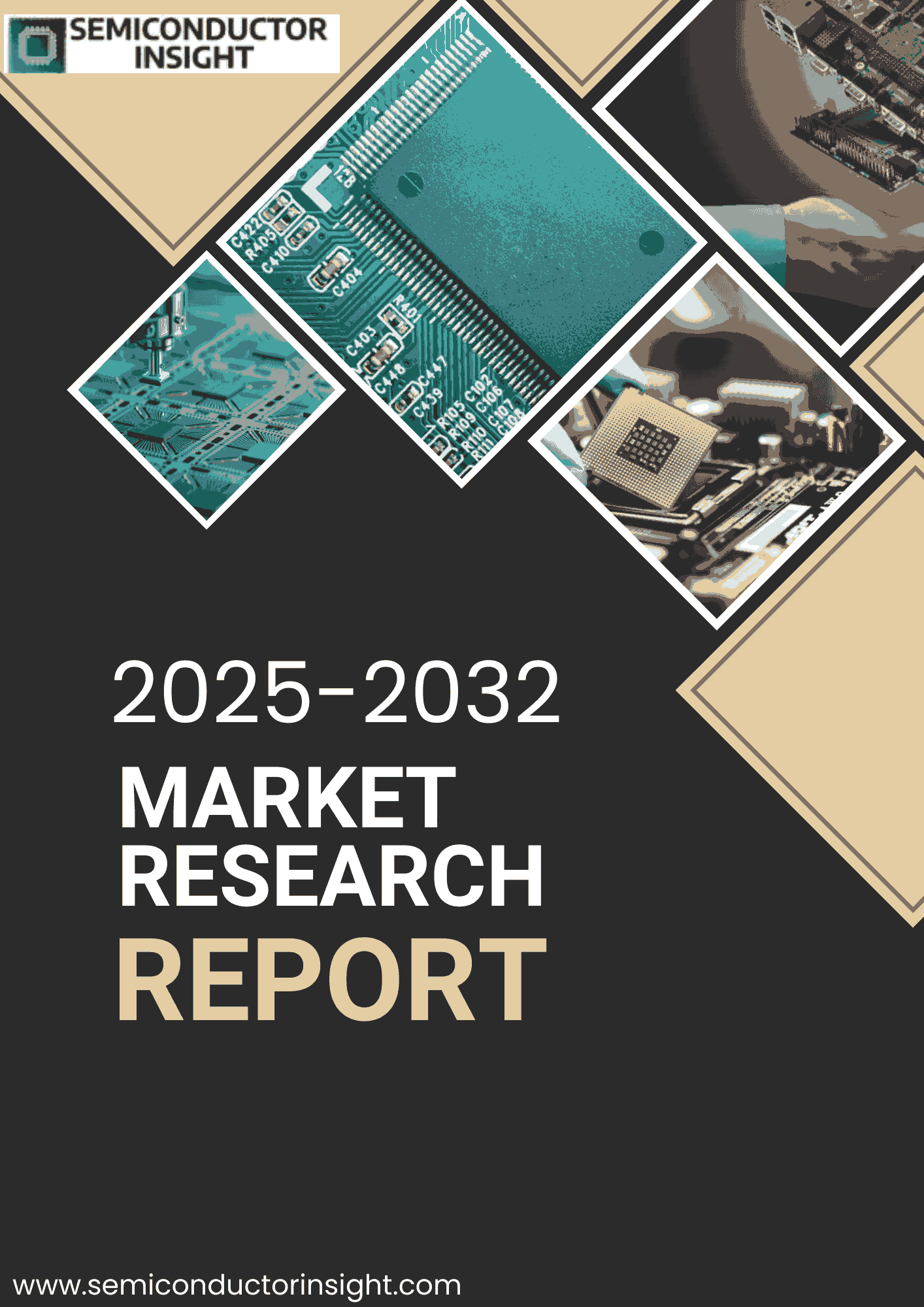
Get Sample Report PDF for Exclusive Insights
Report Sample Includes
- Table of Contents
- List of Tables & Figures
- Charts, Research Methodology, and more...
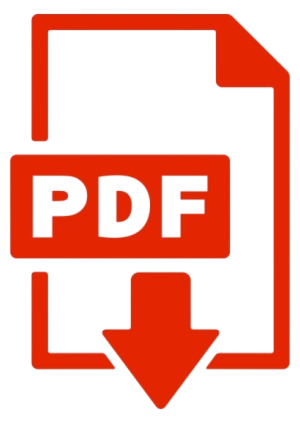