MARKET INSIGHTS
The global Output Flange Market size was valued at US$ 127.8 million in 2024 and is projected to reach US$ 203.9 million by 2032, at a CAGR of 6.9% during the forecast period 2025-2032.
Output flanges are critical mechanical components used to connect rotating shafts in various industrial applications. These flanges serve as interfaces between motors, gearboxes, and driven equipment, ensuring precise torque transmission while maintaining alignment stability. Common types include rigid, semi-flexible, and flexible variants, each designed for specific load-bearing requirements across automotive, industrial automation, and chemical processing sectors.
The market growth is driven by increasing industrialization and demand for precision-engineered power transmission systems. The automotive industry accounts for 38% of total demand, followed by industrial automation at 29%, as manufacturers prioritize energy-efficient machinery. Notably, China dominates production with 42% market share, while North America leads in high-performance flange adoption. Key players like Ford Motor Company and Euroricambi Group are expanding their portfolios through strategic acquisitions, with the top five manufacturers controlling 51% of global revenue in 2024.
MARKET DYNAMICS
MARKET DRIVERS
Rising Demand in Automotive Industry to Accelerate Output Flange Market Growth
The global automotive industry witnessed production of over 85 million vehicles in 2023, creating massive demand for drivetrain components like output flanges. As transmission systems become more sophisticated to meet stringent emission norms, the need for precision-engineered flange connections grows exponentially. Output flanges play a critical role in transferring torque from transmission to wheels while maintaining alignment – a function becoming increasingly important with the shift toward electrified powertrains. The Asian automotive sector alone accounted for more than 50% of global flange consumption in transmission applications last year.
Industrial Automation Boom Creating New Demand Verticals
Industrial automation investments exceeded $260 billion globally in 2024, driving demand for robust mechanical power transmission components. Output flanges are becoming indispensable in robotic arm joints, CNC machine rotary tables, and automated material handling systems where torque transfer reliability is paramount. The semiconductor manufacturing sector’s rapid expansion requires ultra-precision flange connections in wafer handling robots – a niche generating double-digit growth annually. Furthermore, predictive maintenance technologies are increasing replacement cycles for industrial flange components as failures can be anticipated before catastrophic breakdowns occur.
Material Advancements Enhancing Product Lifespan
Recent innovations in metallurgy and surface treatment technologies have significantly improved output flange durability. Specialized coatings now extend maintenance intervals by 40-60% in harsh operating environments, while new aluminum alloy formulations achieve steel-like strength at 60% reduced weight. These material breakthroughs are particularly valuable in aerospace and marine applications where weight savings translate directly to operational efficiency gains. Leading manufacturers are reporting 15-20% higher ASPs for premium material flanges as end-users recognize the total cost of ownership benefits.
MARKET RESTRAINTS
Supply Chain Volatility Impacting Raw Material Availability
The output flange manufacturing sector faces significant challenges from ongoing disruptions in global metal supply chains. Specialty steel alloys critical for high-performance flanges have seen lead times extend from 8-12 weeks to 6-9 months in some cases. This volatility stems from multiple factors including geopolitical tensions affecting commodity exports and energy-intensive production processes becoming economically unviable in certain regions. Inventory-to-sales ratios for flange manufacturers dropped to record lows in 2023, forcing many to implement allocation programs for customers.
Standardization Challenges Across Industries
Lack of unified technical standards for output flanges creates compatibility headaches across different equipment platforms. While ISO and ANSI standards exist, many OEMs maintain proprietary flange specifications that limit component interoperability. This fragmentation increases development costs for flange manufacturers who must maintain separate production lines for marginally different designs. The heavy equipment sector demonstrates this challenge clearly – identical horsepower rated machines from different brands may require completely incompatible flange connections due to legacy design philosophies.
MARKET OPPORTUNITIES
Electrification Creating New Design Paradigms
The transition to electric vehicles represents a massive redesign opportunity for output flange manufacturers. EV powertrains demand flanges capable of handling higher rotational speeds with minimal vibration – requirements exceeding conventional ICE vehicle specifications. Smart flange designs incorporating vibration-damping materials and real-time condition monitoring capabilities could capture significant market share as EV production scales up globally. Projections indicate the EV-specific flange market segment will grow at 28% CAGR through 2030.
Aftermarket Potential in Aging Industrial Base
With over 60% of installed industrial machinery now operating beyond recommended service lives in developed markets, the replacement parts sector offers lucrative growth potential. Output flanges in particular suffer from metal fatigue and wear-related failures in aging equipment. Manufacturers offering retrofittable solutions with extended service intervals can capitalize on this trend. The mining and construction equipment sectors alone represent a $3.2 billion annual aftermarket opportunity for flange components as fleet operators increasingly prioritize preventive maintenance over costly downtime events.
MARKET CHALLENGES
Competition from Alternative Power Transmission Technologies
Traditional flange connections face mounting competition from newer torque transfer solutions like magnetic couplings and harmonic drives. These technologies offer maintenance-free operation and perfect misalignment compensation – advantages that appeal to industries seeking to minimize operational downtime. While flanges still dominate high-torque applications, their market share in precision motion control systems declined by 12% over the past five years as alternative technologies gained traction in robotics and medical equipment applications.
Skilled Labor Shortages Impacting Quality Standards
Precision flange manufacturing requires highly skilled machinists and quality engineers – roles increasingly difficult to fill as experienced workers retire. The industry reports a 40% gap between job openings and qualified applicants for CNC machining positions specializing in flange production. This talent shortage frequently results in extended lead times and occasional quality escapes as production teams stretch to meet demand. Apprenticeship programs take 3-5 years to yield proficient operators, creating a structural challenge for maintaining manufacturing excellence standards.
OUTPUT FLANGE MARKET TRENDS
Advancements in Manufacturing Technologies to Boost Market Growth
The global Output Flange market is witnessing significant growth due to advancements in manufacturing technologies, particularly in precision engineering and materials science. The increasing adoption of CNC machining and additive manufacturing has enhanced the production efficiency and durability of output flanges, making them more reliable for high-torque applications. The market is projected to grow at a CAGR of approximately 5.8% from 2024 to 2032, driven by innovations in lightweight and high-strength materials such as forged steel and aluminum alloys. Furthermore, automation in production lines has minimized human error, ensuring tighter tolerances and higher-quality output flanges for critical industrial applications.
Other Trends
Rising Demand in the Automotive Sector
The automotive industry remains a dominant end-user of output flanges, accounting for over 35% of the global market share in 2024. With the shift towards electric vehicles (EVs), manufacturers are developing specialized flanges to accommodate higher torque requirements in EV drivetrains. Companies like Ford Motor Company and Euroricambi Group are investing heavily in R&D to produce corrosion-resistant and lightweight flanges that enhance vehicle performance. Additionally, stringent emission norms are pushing automakers to adopt more efficient power transmission systems, further driving the demand for high-performance output flanges.
Expansion of Industrial Automation
The rapid expansion of industrial automation is another pivotal trend shaping the output flange market. As factories increasingly integrate robotics and automated machinery, the need for precision-engineered flanges that ensure seamless power transmission has surged. The industrial automation segment is expected to grow at a CAGR of 6.2% over the next six years, with applications in conveyor systems, CNC machines, and robotic arms. Leading suppliers like Ningbo ZhongDa Leader Intelligent Transmission Co., Ltd. are expanding their product portfolios to cater to this demand, introducing modular and semi-flexible flanges that simplify installation and maintenance in automated environments.
COMPETITIVE LANDSCAPE
Key Industry Players
Leading Manufacturers Focus on Innovation and Expansion to Gain Market Share
The global output flange market showcases a competitive yet fragmented landscape, with both established players and emerging manufacturers vying for dominance. Ningbo ZhongDa Leader Intelligent Transmission Co., Ltd. has emerged as a frontrunner, holding significant market share due to its diverse product range and strong foothold in Asia-Pacific markets. Their recent investments in automated production lines have further strengthened their position.
Euroricambi Group and Hangzhou ANG Drive Co., Ltd. maintain substantial market presence, particularly in European and North American automotive sectors. These companies are leveraging their technical expertise in precision engineering to develop flanges with enhanced durability and performance characteristics.
Manufacturers are increasingly focusing on strategic collaborations to expand their geographical reach. Several key players have announced joint ventures with local distributors to penetrate emerging markets, where industrial growth is driving demand for robust transmission components.
Meanwhile, Nitech Stainless Inc. and Bodine Electric Company are differentiating themselves through material innovation, particularly in corrosion-resistant alloys. This specialization has allowed them to capture niche segments in chemical processing and marine applications.
List of Key Output Flange Manufacturers
- Ningbo ZhongDa Leader Intelligent Transmission Co., Ltd. (China)
- Euroricambi Group (Italy)
- Hangzhou ANG Drive Co., Ltd. (China)
- Nitech Stainless Inc. (U.S.)
- Bodine Electric Company (U.S.)
- Neo Impex (India)
- Ford Motor Company (U.S.)
The competitive dynamics in the output flange market are further influenced by vertical integration strategies. Several manufacturers have begun producing raw materials in-house to better control quality and costs. This trend is particularly evident among Chinese manufacturers, who are capitalizing on domestic supply chain advantages.
Price competition remains intense, especially in the standard flange segment. However, companies offering customized solutions and value-added services maintain healthy margins. The market leaders continue to invest in digital manufacturing technologies, with Industry 4.0 implementations becoming a key differentiator in production efficiency and product consistency.
Segment Analysis:
By Type
Flexibility Segment Leads Due to Its Superior Performance in Vibration Damping and Misalignment Compensation
The market is segmented based on type into:
- Flexibility
- Subtypes: Rubber flex, Metallic flex, and others
- Rigid
- Semi-flexible
By Application
Automotive Industry Dominates Due to High Demand for Power Transmission Components
The market is segmented based on application into:
- Automotive Industry
- Chemical Industry
- Industrial Automation
- Others
By Material
Steel Flanges Hold Largest Share Due to Durability and Cost-Effectiveness
The market is segmented based on material into:
- Steel
- Subtypes: Carbon steel, Stainless steel
- Aluminum
- Cast Iron
By End User
OEMs Dominate Demand Due to High Volume Production Requirements
The market is segmented based on end user into:
- Original Equipment Manufacturers (OEMs)
- Aftermarket
Regional Analysis: Output Flange Market
North America
The North American output flange market is characterized by strong demand from the automotive and industrial automation sectors, driven by technological advancements and stringent quality standards. The U.S. holds the largest market share, supported by major automotive OEMs like Ford Motor Company, which heavily invest in drivetrain components. Canada’s market is growing steadily due to expansions in manufacturing and chemical industries. While the adoption of high-performance flanges is prominent, price sensitivity among small-scale manufacturers remains a challenge. Regulatory compliance, particularly around material durability and environmental impact, further shapes market dynamics.
Europe
Europe’s mature automotive and industrial sectors sustain demand for precision-engineered output flanges, with Germany and France leading in production and innovation. The region emphasizes lightweight, high-strength materials due to strict EU emissions regulations, pushing manufacturers toward advanced alloys. However, competition from low-cost Asian suppliers has pressured profit margins. The Nordic Countries exhibit growth in renewable energy applications, expanding flange usage in wind turbines and hydraulic systems. Despite economic uncertainties, Europe remains a key hub for R&D and sustainable manufacturing practices in flange technology.
Asia-Pacific
China dominates the APAC output flange market, fueled by its vast automotive production and infrastructure projects. Local manufacturers like Ningbo ZhongDa Leader leverage cost advantages to supply global OEMs, though quality inconsistencies persist. India is emerging as a significant player due to its expanding chemical and automation industries, while Japan and South Korea focus on high-precision applications in robotics and electronics. Price competition is intense, but investments in automation-grade flanges are rising. The region’s growth is tempered by supply chain bottlenecks and fluctuating raw material costs, particularly for steel and aluminum.
South America
Market growth in South America is uneven, with Brazil and Argentina driving most demand through agricultural machinery and automotive assembly. Economic instability and limited domestic production capability have led to heavy reliance on imports, primarily from China. Aftermarket sales constitute a sizable portion of revenue due to aging vehicle fleets. The lack of standardized regulations hampers the adoption of advanced flange solutions, though niche opportunities exist in mining and oil & gas equipment. Local manufacturers struggle to compete with global giants, but partnerships with international suppliers are gradually improving capacity.
Middle East & Africa
The UAE and Saudi Arabia lead flange demand in this region, supported by oilfield expansions and infrastructure developments. Turkey’s manufacturing sector also contributes significantly, supplying flanges for European automotive markets. However, the broader MEA market suffers from fragmented supply chains and underdeveloped industrial bases. While South Africa shows potential in mining applications, political and economic constraints limit large-scale investments. The shift toward localized production is gaining traction, but most high-specification flanges are still imported. Long-term growth hinges on stabilization of industrial policies and increased foreign investments.
Report Scope
This market research report provides a comprehensive analysis of the global and regional Output Flange markets, covering the forecast period 2025–2032. It offers detailed insights into market dynamics, technological advancements, competitive landscape, and key trends shaping the industry.
Key focus areas of the report include:
- Market Size & Forecast: Historical data and future projections for revenue, unit shipments, and market value across major regions and segments. The global Output Flange market was valued at USD 1.2 billion in 2024 and is projected to reach USD 1.8 billion by 2032, growing at a CAGR of 5.3% during the forecast period.
- Segmentation Analysis: Detailed breakdown by product type (flexibility, rigid, semi-flexible), application (automotive, chemical, industrial automation), and end-user industry to identify high-growth segments.
- Regional Outlook: Insights into market performance across North America, Europe, Asia-Pacific, Latin America, and Middle East & Africa. The U.S. market size is estimated at USD 320 million in 2024, while China is projected to reach USD 450 million by 2032.
- Competitive Landscape: Profiles of leading manufacturers including Ningbo ZhongDa Leader, Euroricambi Group, Hangzhou ANG Drive, with the top five players holding approximately 42% market share in 2024.
- Technology Trends: Assessment of emerging manufacturing techniques, material innovations, and integration with Industry 4.0 solutions.
- Market Drivers & Restraints: Evaluation of factors including automotive production growth, industrial automation trends, and raw material price volatility.
- Stakeholder Analysis: Strategic insights for component suppliers, OEMs, system integrators, and investors regarding market opportunities.
Primary and secondary research methods are employed, including interviews with industry experts, analysis of financial reports, and market intelligence from verified sources to ensure accuracy.
FREQUENTLY ASKED QUESTIONS:
What is the current market size of Global Output Flange Market?
-> Output Flange Market size was valued at US$ 127.8 million in 2024 and is projected to reach US$ 203.9 million by 2032, at a CAGR of 6.9% during the forecast period 2025-2032.
Which key companies operate in Global Output Flange Market?
-> Key players include Ningbo ZhongDa Leader, Euroricambi Group, Hangzhou ANG Drive, Nitech Stainless, Bodine Electric Company, and Ford Motor Company.
What are the key growth drivers?
-> Key growth drivers include increasing automotive production, growth in industrial automation, and infrastructure development in emerging economies.
Which region dominates the market?
-> Asia-Pacific holds the largest market share (42% in 2024), driven by manufacturing growth in China and India, while North America leads in technological advancements.
What are the emerging trends?
-> Emerging trends include lightweight composite materials, precision manufacturing technologies, and smart flange solutions with embedded sensors.
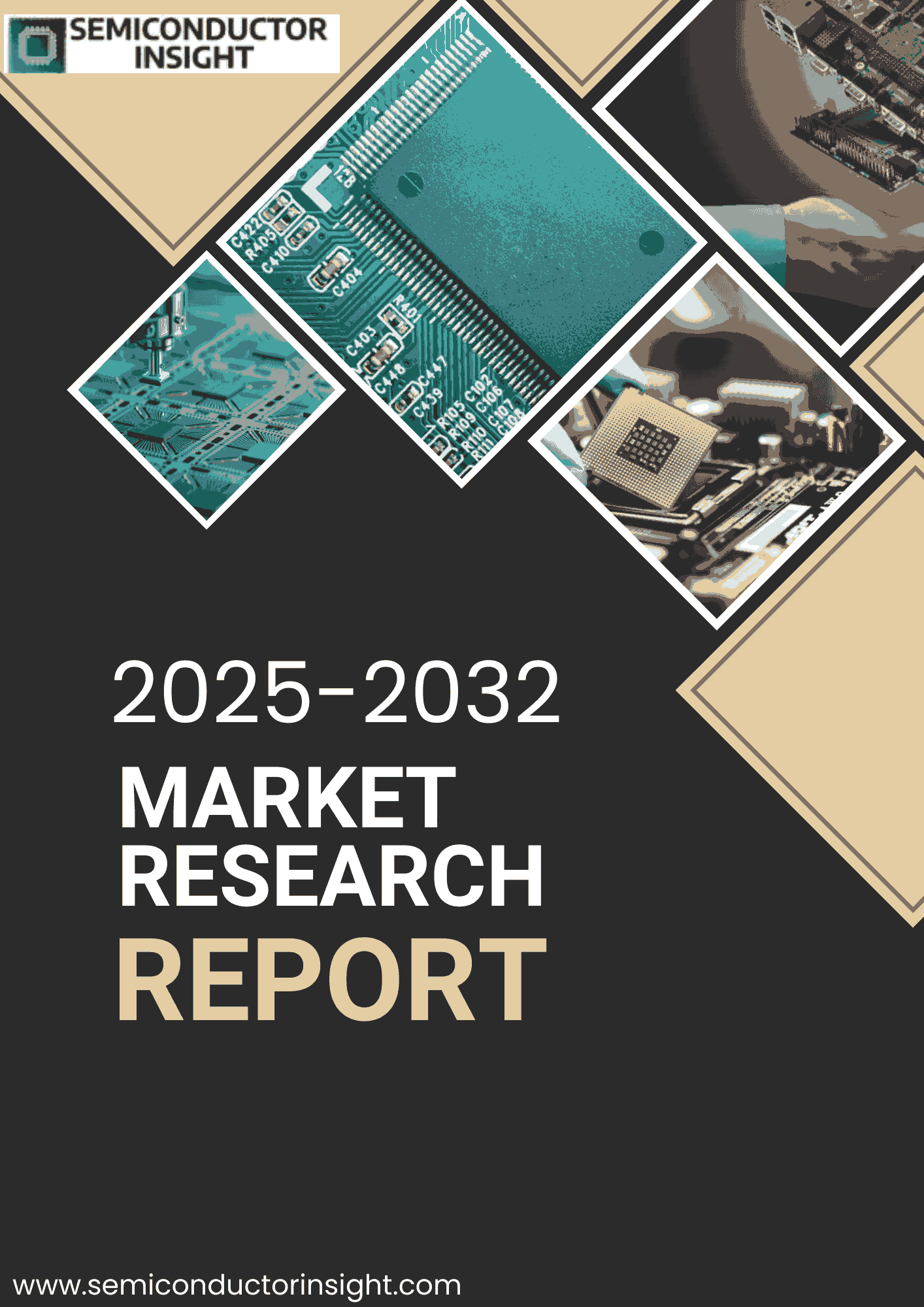
Get Sample Report PDF for Exclusive Insights
Report Sample Includes
- Table of Contents
- List of Tables & Figures
- Charts, Research Methodology, and more...
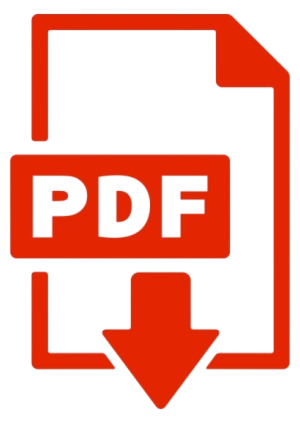