MARKET INSIGHTS
The global Dielectric Etch Device Market size was valued at US$ 456 million in 2024 and is projected to reach US$ 634 million by 2032, at a CAGR of 4.7% during the forecast period 2025-2032
Dielectric etch devices are critical equipment used in semiconductor manufacturing to selectively remove dielectric materials during chip fabrication. These devices enable precise patterning of insulating layers through plasma-based etching techniques, which are essential for advanced logic, memory, and power device production. The technology encompasses two main types: capacitively coupled plasma (CCP) etchers and inductively coupled plasma (ICP) etchers, each offering distinct advantages for different semiconductor applications.
The market growth is driven by increasing demand for semiconductor devices across consumer electronics, automotive, and AI applications. While the CCP etch device segment currently holds majority share due to its cost-effectiveness in bulk dielectric removal, the ICP segment is gaining traction for high-aspect-ratio etching in advanced nodes. Key players like TEL (Tokyo Electron Ltd), Lam Research, and Applied Materials dominate the competitive landscape, collectively holding over 65% market share as of 2024. Recent technological advancements in atomic layer etching and selective material removal are further expanding the market potential.
MARKET DYNAMICS
MARKET DRIVERS
Surge in Semiconductor Demand Strengthens Dielectric Etch Device Market Growth
The global semiconductor industry’s rapid expansion is driving substantial demand for dielectric etch devices, with wafer fabrication plants requiring increasingly sophisticated etching solutions. The semiconductor market has demonstrated resilience despite economic fluctuations, maintaining steady growth projections above 7% annually. This expansion is further amplified by the rising complexity of semiconductor designs, including advanced nodes below 7nm, which demand precision etching with atomic-layer accuracy. The transition to three-dimensional chip architectures like FinFET and GAA (Gate-All-Around) technologies has doubled the required etching steps per wafer compared to planar transistors, directly benefiting dielectric etch equipment providers.
Advanced Packaging Technologies Create New Application Horizons
Emerging advanced packaging techniques including 2.5D/3D IC integration, fan-out wafer-level packaging (FOWLP), and chiplet architectures are generating new growth avenues for dielectric etch systems. The heterogeneous integration trend in packaging requires precise dielectric material patterning for through-silicon vias (TSVs), redistribution layers, and micro-bump formation. The advanced packaging market is projected to grow at a 14% CAGR through 2030, creating parallel demand for specialized etching solutions. Leading foundries have increased their capital expenditure allocations for packaging technologies from 12% to over 20% of total equipment spending, indicating strong market potential for dielectric etch solution providers.
Furthermore, the increasing adoption of compound semiconductors for power electronics and RF applications necessitates tailored dielectric etch solutions. Materials like silicon carbide and gallium nitride present unique etching challenges that conventional silicon processes cannot address, prompting equipment manufacturers to develop specialized systems. The power device market is expected to account for nearly 18% of dielectric etch tool shipments by 2026, compared to just 9% in previous years.
MARKET RESTRAINTS
High Capital Requirements Limit Market Penetration
Dielectric etch systems represent one of the most capital-intensive segments in semiconductor manufacturing, with average tool prices ranging between $4-7 million depending on configuration and capabilities. This creates significant barriers to entry for smaller semiconductor manufacturers and research institutions. The total cost of ownership extends beyond equipment purchase, including facility modifications, maintenance contracts, and specialized operator training that can add 30-40% to initial investment costs. While the industry is transitioning to more flexible multi-chamber cluster tools, the high price points continue to limit market adoption outside leading-edge foundries and memory manufacturers.
Additional Constraints
Process Complexity and Yield Challenges
Advanced node development below 7nm has introduced unprecedented challenges in dielectric etch process control, particularly for high-aspect-ratio features. Maintaining critical dimension uniformity while achieving desired etch profiles requires sophisticated process monitoring and control systems that add to operational complexity. The transition to EUV lithography has further complicated etch processes, as pattern transfer fidelity becomes more challenging with smaller features. These technical hurdles contribute to longer equipment qualification cycles and reduced tool productivity during development phases.
Geopolitical Tensions and Supply Chain Vulnerability
Recent trade restrictions on semiconductor equipment have created uncertainty in the dielectric etch device market, particularly affecting technology transfers between regions. The concentration of critical component suppliers in specific geographic locations increases supply chain risks, with lead times for certain subsystems extending beyond 12 months in some cases. This situation is prompting manufacturers to reevaluate their supplier networks, potentially increasing costs and delaying product introductions.
MARKET CHALLENGES
Technology Transition Periods Create Adoption Hurdles
The semiconductor industry’s cyclic nature presents ongoing challenges for dielectric etch equipment providers, particularly during technology node transitions. The shift from FinFET to GAA transistor architectures requires significant etch process redevelopment, with equipment manufacturers facing extended evaluation periods before volume adoption. Foundries typically undertake 12-18 months of intensive testing for new node qualifications, during which equipment utilization rates may drop below 50% for development tools. This lengthens the return on investment period and creates cash flow challenges for smaller suppliers.
Process Integration Complexities
Modern semiconductor manufacturing requires tight integration between lithography, deposition, and etch processes. Variations in one step can significantly impact subsequent processing, requiring etch equipment to accommodate increasing process variability. The need for adaptive process control and real-time metrology adds system complexity and cost. Additionally, hybrid bonding technologies for 3D IC applications demand exceptional etch uniformity across entire wafers, pushing the limits of current tool capabilities.
Talent Shortage Impacts Innovation Pace
The specialized nature of dielectric etch process development has created an acute shortage of qualified engineers, particularly those with expertise in both plasma physics and semiconductor device integration. The industry requires approximately 25% more process engineers than currently available, with that gap expected to widen as technology advances. This talent shortage is slowing innovation cycles and making it difficult for companies to fully capitalize on emerging market opportunities.
MARKET OPPORTUNITIES
Emerging Memory Technologies Open New Frontiers
The rapid development of next-generation memory technologies including MRAM, ReRAM, and FeRAM presents significant opportunities for dielectric etch equipment providers. These emerging memory types require specialized etch processes for magnetic tunnel junctions and resistive switching materials that differ substantially from conventional NAND or DRAM processes. The memory market is projected to account for nearly 35% of all dielectric etch tool shipments within five years, with emerging memories representing the fastest-growing segment. Equipment manufacturers developing solutions tailored to these unique requirements stand to gain substantial market share as volume production ramps.
AI-Driven Process Optimization Creates Value-Added Services
Artificial intelligence and machine learning implementations for etch process optimization are creating new revenue streams for equipment providers. Advanced process control systems utilizing real-time sensor data and predictive algorithms can improve yield by 2-3 percentage points—a significant margin in high-volume production. Leading manufacturers are transitioning to service-based business models offering performance guarantees backed by AI-driven analytics. This not only improves customer economics but also creates recurring revenue opportunities through software subscriptions and predictive maintenance services.
Furthermore, the push toward sustainable semiconductor manufacturing is driving demand for etch systems with reduced environmental impact. Next-generation tools achieving 30-40% reductions in greenhouse gas emissions per processed wafer are commanding premium prices and gaining preferential selection in new fab constructions. Regulatory pressures combined with corporate sustainability initiatives make this a key differentiator for equipment suppliers in competitive bidding situations.
DIELECTRIC ETCH DEVICE MARKET TRENDS
Advancements in Semiconductor Fabrication Driving Market Growth
The dielectric etch device market is experiencing significant growth as semiconductor manufacturers transition to more advanced process nodes. With the increasing adoption of 3D NAND flash memory and FinFET transistors, the demand for precise dielectric etching solutions has surged exponentially. The market is projected to grow at a CAGR of approximately 8.5% from 2024 to 2032, reflecting the critical role of etch processes in modern chip manufacturing. Leading foundries are investing heavily in next-generation etching equipment capable of handling sub-5nm geometries, with particular emphasis on achieving higher selectivity and anisotropy in dielectric removal processes. Furthermore, the integration of artificial intelligence for process control is enabling real-time adjustments during etching operations, significantly improving yield rates in wafer fabrication.
Other Trends
Expansion in Memory Chip Production
The memory sector currently accounts for over 35% of dielectric etch equipment deployments, driven by surging demand for high-density storage solutions. Manufacturers are increasingly adopting hybrid bonding techniques that require sophisticated dielectric etching capabilities for both oxide and nitride layers. The transition to 200+ layer 3D NAND architectures has particularly intensified the need for deep-etched through-silicon via (TSV) formations with aspect ratios exceeding 60:1. This trend is complemented by the growing integration of novel low-k dielectric materials in DRAM production, necessitating specialized etching chemistries that prevent damage to delicate interconnect structures.
Geopolitical Factors Influencing Supply Chains
The semiconductor equipment market is experiencing notable shifts due to changing trade policies and regional investment strategies. Governments worldwide are implementing substantial incentives for local semiconductor manufacturing, with the U.S. CHIPS Act allocating $39 billion for facility construction and equipment purchases. This has led to accelerated adoption of dielectric etch tools in emerging production clusters, particularly in North America and Southeast Asia. Meanwhile, export controls on advanced fabrication equipment have prompted Chinese manufacturers to accelerate domestic equipment development, with local players now commanding nearly 15% of the mid-range dielectric etch market segment. These developments are reshaping competitive dynamics and pricing strategies across the industry value chain.
COMPETITIVE LANDSCAPE
Key Industry Players
Semiconductor Giants Vie for Market Dominance Through Technological Advancements
The dielectric etch device market exhibits a consolidated competitive landscape, dominated by established semiconductor equipment manufacturers with strong R&D capabilities and global footprints. Tokyo Electron Limited (TEL) captured the largest market share in 2024, leveraging its comprehensive portfolio of CCP and ICP etch systems specifically optimized for advanced node semiconductor manufacturing.
Lam Research and Applied Materials collectively accounted for over 45% of the global revenue share, owing to their entrenched positions in foundry and memory markets. These companies continue to capitalize on the transition to 3D NAND and EUV patterning requirements, with Lam’s Kiyo® series particularly gaining traction in high-aspect-ratio dielectric etching applications.
Emerging Chinese players like Naura and AMEC are rapidly expanding their market presence through competitive pricing and government-supported semiconductor independence initiatives. Naura’s recent breakthrough in atomic layer etching technology positions it as a credible alternative for mature node applications in domestic Chinese fabs.
Market leaders are aggressively pursuing capacity expansions and partnerships to address the surging demand from logic and memory manufacturers. TEL’s recent $150 million investment in enhanced production facilities for its etch systems directly responds to the 30% year-over-year demand increase from leading foundries like TSMC and Samsung.
List of Key Dielectric Etch Device Manufacturers
- Tokyo Electron Limited (TEL) (Japan)
- Lam Research Corporation (U.S.)
- Applied Materials, Inc. (U.S.)
- Advanced Micro-Fabrication Equipment (AMEC) (China)
- Naura Technology Group Co., Ltd. (China)
- GigaLane Corporation (South Korea)
Industry competition is intensifying as manufacturers focus on developing solutions for next-generation challenges including high-k/metal gate stacks, low-k dielectric etching, and through-silicon via (TSV) applications. The top five players continue to invest 18-22% of their revenues in R&D annually to maintain technological leadership in this rapidly evolving segment.
Recent strategic initiatives include Applied Materials’ collaboration with leading IDMs to develop selective etch technologies targeting gate-all-around transistor architectures, while Lam Research has strengthened its position in 3D NAND manufacturing through continuous refinements to its Syndion® platform. These developments underscore the critical importance of etch process control in enabling continued semiconductor scaling.
Segment Analysis:
By Type
CCP Etch Device Segment Dominates Due to High Precision in Semiconductor Manufacturing
The market is segmented based on type into:
- CCP Etch Device
- ICP Etch Device
By Application
Logic and Memory Segment Leads Owing to Expanding Semiconductor Industry
The market is segmented based on application into:
- Logic and Memory
- MEMS
- Power Device
- Others
By Technology Node
Advanced Nodes (Below 10nm) Gaining Traction for High-Performance Chips
The market is segmented based on technology node into:
- Above 28nm
- 10nm to 28nm
- Below 10nm
By End User
Foundries Show Strong Adoption for Volume Production Needs
The market is segmented based on end user into:
- Foundries
- IDMs (Integrated Device Manufacturers)
- Research Institutes
Regional Analysis: Dielectric Etch Device Market
North America
The North American dielectric etch device market is characterized by strong semiconductor R&D investments and major fab expansions, particularly in the United States. Driven by the CHIPS Act’s $52 billion funding and increasing demand for advanced logic/memory chips, the region favors high-precision etching systems from leaders like Lam Research and Applied Materials. However, export controls on advanced semiconductor equipment to China present both challenges and opportunities for domestic suppliers. The market exhibits particular strength in 3D NAND and advanced logic node applications, with Texas and Arizona emerging as key hubs due to new fab constructions.
Europe
Europe maintains specialize in niche applications like MEMS and power devices, with Germany and France leading in equipment adoption. While the region lacks leading-edge logic fabs, it compensates through strengths in specialty semiconductors demanded by automotive and industrial sectors. The EU Chips Act’s €43 billion investment is beginning to stimulate domestic equipment demand, though the market remains constrained by fewer mega-fabs compared to Asia. European research institutes continue driving innovation in etch process control and new material applications, creating opportunities for equipment upgrades.
Asia-Pacific
As the dominant force in semiconductor manufacturing, Asia-Pacific represents over 60% of global dielectric etch demand, concentrated in China, South Korea, and Taiwan. China’s aggressive fab expansion, including SMIC’s new facilities, drives substantial equipment purchases despite U.S. export restrictions. This region shows the strongest demand for advanced high-aspect ratio etching capabilities for 3D NAND and logic scaling below 7nm. While geopolitical factors complicate the landscape, local vendors like Naura are gaining share in mature nodes. Southeast Asia is emerging as a secondary hub with Singapore and Malaysia attracting investments in specialty semiconductor production.
South America
The South American market remains in early development stages, with Brazil showing the most activity through initiatives supporting local semiconductor packaging and analog chip production. While lacking advanced etching requirements, the region presents opportunities for refurbished equipment and entry-level systems. Economic instability and limited government support continue to restrain meaningful market expansion despite the growing importance of electronics manufacturing in countries like Argentina and Chile.
Middle East & Africa
This region represents an emerging opportunity as countries like Saudi Arabia invest heavily in technology diversification strategies. The recent establishment of semiconductor initiatives in NEOM and Abu Dhabi has generated initial demand for basic etch capabilities, primarily targeting power electronics and sensors. While currently negligible in global terms, strategic investments in infrastructure and education could establish localized demand centers over the next decade. Key challenges include limited technical expertise and competition from established Asian supply chains.
Report Scope
This market research report provides a comprehensive analysis of the global and regional Dielectric Etch Device markets, covering the forecast period 2025–2032. It offers detailed insights into market dynamics, technological advancements, competitive landscape, and key trends shaping the industry.
Key focus areas of the report include:
- Market Size & Forecast: Historical data and future projections for revenue, unit shipments, and market value across major regions and segments.
- Segmentation Analysis: Detailed breakdown by product type (CCP Etch Device, ICP Etch Device), application (Logic and Memory, MEMS, Power Device, Others), and end-user industry to identify high-growth segments.
- Regional Outlook: Insights into market performance across North America, Europe, Asia-Pacific, Latin America, and Middle East & Africa, with country-level analysis for key markets.
- Competitive Landscape: Profiles of leading market participants including TEL (Tokyo Electron Ltd), Lam Research, Applied Materials, AMEC, Naura, and GigaLane, covering their market share, product portfolios, and strategic initiatives.
- Technology Trends & Innovation: Assessment of emerging fabrication techniques, integration of AI in semiconductor manufacturing, and evolving industry standards.
- Market Drivers & Restraints: Evaluation of factors driving market growth including semiconductor industry expansion, along with challenges like supply chain constraints and geopolitical factors.
- Stakeholder Analysis: Strategic insights for semiconductor manufacturers, equipment suppliers, foundries, and investors regarding market opportunities.
The research methodology combines primary interviews with industry experts and analysis of verified market data to ensure accuracy and reliability of insights.
FREQUENTLY ASKED QUESTIONS:
What is the current market size of Global Dielectric Etch Device Market?
-> Dielectric Etch Device Market size was valued at US$ 456 million in 2024 and is projected to reach US$ 634 million by 2032, at a CAGR of 4.7% .
Which key companies operate in Global Dielectric Etch Device Market?
-> Key players include TEL (Tokyo Electron Ltd), Lam Research, Applied Materials, AMEC, Naura, and GigaLane, with the top five companies holding approximately 75% market share in 2024.
What are the key growth drivers?
-> Key growth drivers include increasing demand for advanced semiconductor devices, expansion of foundry capacity, and adoption of new fabrication technologies for next-generation chips.
Which region dominates the market?
-> Asia-Pacific dominates the market with over 60% share, driven by semiconductor manufacturing hubs in China, Taiwan, South Korea, and Japan.
What are the emerging trends?
-> Emerging trends include development of atomic-level etching technologies, integration of AI for process optimization, and increasing adoption of high-aspect-ratio dielectric etching for advanced packaging applications.
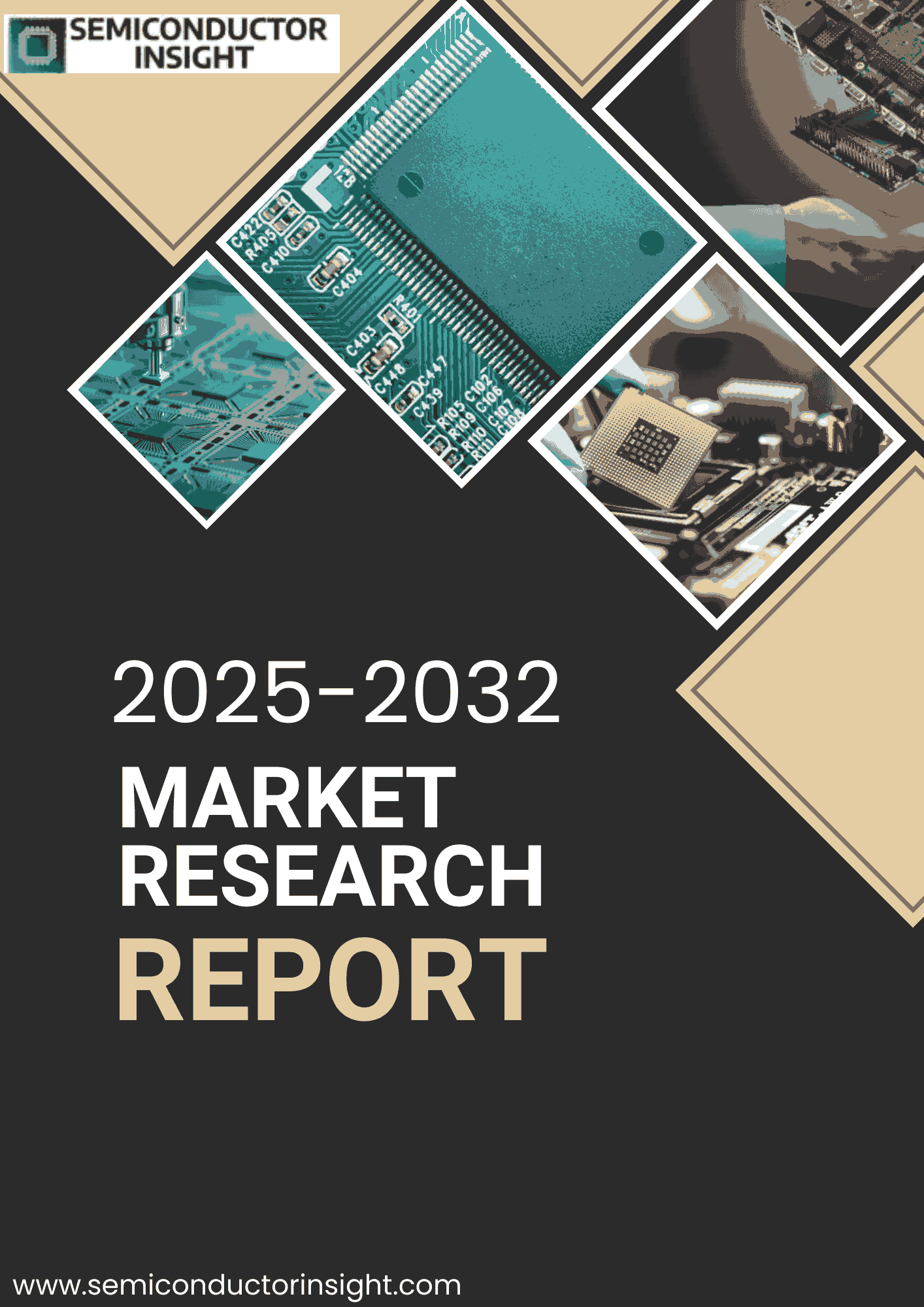
Get Sample Report PDF for Exclusive Insights
Report Sample Includes
- Table of Contents
- List of Tables & Figures
- Charts, Research Methodology, and more...
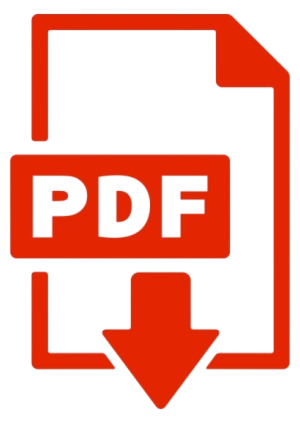