MARKET INSIGHTS
The global Consumer Electronics Printed Circuit Board Market size was valued at US$ 18.4 billion in 2024 and is projected to reach US$ 26.7 billion by 2032, at a CAGR of 5.4% during the forecast period 2025-2032.
Printed circuit boards are essential components in electronic devices that provide mechanical support and electrical connections using conductive pathways. These boards come in three primary types: single-layer (basic circuitry), double-layer (increased complexity), and multi-layer (high-density interconnects for advanced applications). PCBs serve as the backbone for devices ranging from smartphones to industrial equipment, with consumer electronics accounting for a significant portion of demand.
The market growth is driven by several factors including the proliferation of smart devices, miniaturization trends in electronics, and increasing adoption of IoT-enabled products. While demand remains strong, manufacturers face challenges from raw material price volatility and stringent environmental regulations. The industry is responding with innovations in flexible PCBs and high-frequency materials to meet evolving technological requirements. Key players like Nippon Mektron, Unimicron Technology, and Zhen Ding Technology hold significant market share through continuous R&D investments and strategic partnerships.
MARKET DYNAMICS
MARKET DRIVERS
Proliferation of Smart Devices to Accelerate PCB Demand
The global consumer electronics market continues to expand rapidly, with smart devices driving significant growth in PCB adoption. Smartphones alone account for over 35% of PCB consumption in consumer electronics, with approximately 1.5 billion units shipped annually requiring increasingly sophisticated multi-layer boards. The integration of 5G technology has further increased PCB complexity, as these boards must handle higher frequencies while minimizing signal loss. Manufacturers are responding with innovations like high-density interconnect (HDI) PCBs that enable smaller form factors without compromising performance.
Additionally, the Internet of Things (IoT) ecosystem expansion continues to create new demand vectors. Smart home devices, wearable technologies, and connected appliances – projected to exceed 30 billion installed units globally by 2025 – all utilize specialized PCBs that balance durability with compact designs. This proliferation across multiple product categories provides manufacturers with diverse revenue streams while pushing technological boundaries in PCB development.
Advancements in Flexible and Miniaturized PCBs Fuel Market Expansion
Recent breakthroughs in flexible PCB technology are transforming product design paradigms across the consumer electronics sector. Flexible PCBs enable innovative form factors in foldable smartphones, rollable displays, and compact wearable devices – all high-growth market segments demonstrating 15-20% annual expansion rates. These advanced substrates offer superior durability against bending and vibration compared to traditional rigid boards, addressing critical reliability concerns in portable electronics.
The miniaturization trend poses both challenges and opportunities for PCB manufacturers. While component footprints shrink by approximately 10% annually according to industry benchmarks, this drives innovation in microvia drilling and ultra-fine line printing techniques. Successful manufacturers are investing heavily in laser direct imaging (LDI) systems and automated optical inspection (AOI) equipment to maintain quality standards while meeting these demanding technical specifications. These technological investments are paying dividends as premium consumer electronics increasingly demand such advanced capabilities.
MARKET RESTRAINTS
Supply Chain Volatility and Material Shortages Constrain Growth
The PCB industry faces significant headwinds from ongoing supply chain disruptions and raw material scarcity. Copper prices, constituting approximately 20-30% of PCB manufacturing costs, have shown 40% volatility over recent years according to commodity indices. Specialty substrates like polyimide for flexible circuits and high-frequency laminates face similar availability challenges, with lead times extending beyond twelve weeks for some formulations.
Geopolitical tensions have further exacerbated these supply chain issues, with strategic materials like rare earth elements becoming subject to export controls in key producing nations. Manufacturers report component shortages increasing production cycle times by 15-25%, forcing difficult trade-offs between inventory carrying costs and order fulfillment capacity. These constraints are particularly acute for small-to-midsize PCB fabricators lacking the purchasing power of larger competitors.
Environmental Regulations Increase Compliance Costs
Stringent environmental regulations governing PCB manufacturing present another significant market restraint. Restrictions on hazardous substances (RoHS) and waste electrical and electronic equipment (WEEE) directives require substantial capital investment in alternative materials and recycling infrastructure. Compliance costs for these regulations can increase production expenses by 8-12% according to industry studies, eroding already thin profit margins.
Emerging regulations targeting per- and polyfluoroalkyl substances (PFAS) in circuit board coatings and solder masks pose additional challenges. These “forever chemicals” have become regulatory targets worldwide, requiring manufacturers to redesign processes and qualify alternative materials – a transition estimated to take 18-24 months per product line. Such regulatory pressures disproportionately affect manufacturers serving price-sensitive market segments where cost increases prove difficult to pass through to customers.
MARKET CHALLENGES
Skilled Labor Shortage Imperils Technological Advancement
The PCB industry faces a critical shortage of skilled technicians and engineers capable of operating increasingly sophisticated manufacturing equipment. Workforce analytics indicate approximately 25% of current PCB manufacturing personnel will reach retirement age within the next five years, while technical education pipelines show declining enrollment in relevant programs. This generational knowledge gap threatens to slow innovation cycles precisely when product complexity demands more specialized expertise.
Training new employees presents substantial challenges, as mastering advanced processes like automated optical inspection (AOI) programming or impedance control typically requires 12-18 months of hands-on experience. Many manufacturers report spending 30-40% more on training and retention programs compared to pre-pandemic levels, yet still struggle to maintain adequate staffing levels for high-mix production environments.
Price Erosion in Commoditized Segments Squeezes Margins
Intense competition in standard PCB product categories continues to exert downward pressure on pricing. Basic double-sided boards have seen average selling prices decline by 3-5% annually in recent years, forcing manufacturers to either pursue higher-value market segments or accept diminishing returns. This pricing pressure originates from both domestic competitors and international manufacturers benefiting from regional subsidies and lower labor costs.
The situation is particularly challenging for manufacturers focused on consumer electronics applications, where product lifecycles continue to shorten while quality expectations rise. Quarterly price renegotiations with major OEMs have become commonplace, leaving little room for material cost increases to be offset. Companies unable to differentiate through technological superiority or value-added services find themselves trapped in margin-eroding competition for high-volume, low-margin contracts.
MARKET OPPORTUNITIES
High-Performance Computing Drives Next-Gen PCB Demand
The exponential growth of artificial intelligence, machine learning, and edge computing applications presents substantial opportunities for advanced PCB manufacturers. High-performance computing (HPC) applications require PCBs capable of handling unprecedented signal speeds and thermal loads, driving demand for specialized materials and innovative thermal management solutions. The HPC segment is projected to grow at nearly double the rate of conventional computing markets, creating premium opportunities for manufacturers with relevant expertise.
These advanced applications particularly value substrates with superior dielectric properties and dimensional stability. Low-loss laminates, while currently representing less than 15% of the overall PCB market, demonstrate growth rates exceeding 12% annually as HPC adoption expands. Manufacturers investing in these high-value segments can command pricing premiums of 25-40% compared to standard FR-4 boards while securing longer-term customer commitments.
Regional Manufacturing Shifts Create Strategic Advantages
Changing geopolitical landscapes and supply chain diversification strategies are reshaping global PCB production patterns. Recent government incentives like the CHIPS Act in the United States and similar initiatives in Europe provide compelling business cases for regional PCB manufacturing expansion. Early adopters of these regionalization strategies report 15-20% reductions in logistics costs and lead times compared to traditional Asia-centric supply chains.
The near-shoring trend extends beyond simple cost considerations, as OEMs increasingly value supply chain resilience and intellectual property protection. Contract manufacturers serving defense, medical, and automotive sectors particularly benefit from these shifts, with certifications like ITAR compliance becoming key differentiators. Strategic positioning in these developing manufacturing hubs allows PCB producers to capture first-mover advantages in emerging technology clusters while mitigating risks associated with single-region dependencies.
CONSUMER ELECTRONICS PRINTED CIRCUIT BOARD MARKET TRENDS
Miniaturization and High-Density Interconnect Technology Driving Market Innovation
The relentless demand for smaller, more powerful consumer electronics is propelling innovations in printed circuit board (PCB) technology. High-density interconnect (HDI) PCBs are gaining significant traction, with adoption rates growing at approximately 8.7% annually to meet the needs of compact devices like smartphones and wearables. Advanced manufacturing techniques such as laser drilling and sequential lamination enable PCB manufacturers to achieve trace widths as narrow as 25 microns, allowing for greater component density without compromising performance. Furthermore, the shift toward flexible and rigid-flex PCBs is accelerating, particularly in wearable devices where bendable circuits improve durability and space utilization. This trend aligns with industry forecasts predicting that flexible PCBs will account for over 22% of the consumer electronics PCB market by 2027.
Other Trends
Sustainability and Lead-Free Materials
Environmental regulations and consumer preferences are reshaping PCB material selection, with the European Union’s Restriction of Hazardous Substances (RoHS) directive driving adoption of halogen-free laminates and lead-free soldering processes. Manufacturers are increasingly investing in bio-based solder masks and recyclable substrates, reducing the carbon footprint of PCB production by an estimated 15-20% per unit. Additionally, water-efficient fabrication methods are being implemented across facilities in water-scarce regions, addressing both regulatory pressures and operational costs. The push toward sustainability is also opening new opportunities for closed-loop recycling systems, where end-of-life PCBs are recovered and reprocessed into new boards.
5G and IoT Integration Demanding Advanced PCB Architectures
The rollout of 5G networks and proliferation of IoT devices are creating unprecedented demand for high-frequency PCBs capable of handling millimeter-wave signals. Materials like PTFE (Teflon) and ceramic-filled hydrocarbons are replacing traditional FR-4 substrates in RF applications, offering signal loss reductions of up to 40%. Meanwhile, embedded component technology—where passive components are integrated directly into the PCB layers—is gaining momentum, reducing form factors by 30% in devices like 5G routers. The industrial IoT segment alone is expected to require 280 million specialized PCBs annually by 2030, with multi-layer designs incorporating 12+ layers becoming standard for edge computing devices. This evolution necessitates tighter tolerances in impedance control, with leading manufacturers now achieving ±5% consistency across production batches.
COMPETITIVE LANDSCAPE
Key Industry Players
Market Leaders Accelerate Product Innovation to Capture Growth in Evolving PCB Sector
The global Consumer Electronics Printed Circuit Board (PCB) market exhibits a fragmented competitive landscape, with established multinational corporations competing alongside agile regional players. Leading companies like AT&S and Sumitomo Electric Industries dominate the market through their technological expertise in high-density interconnect (HDI) PCBs and flexible circuits, which are increasingly demanded for compact wearable devices and advanced tablets. These players collectively accounted for approximately 28% of the global PCB revenue in 2024.
Asian manufacturers such as Unimicron Technology Corporation and Shenzhen Kinwong Electronic are expanding their influence through cost-competitive mass production capabilities. Their growth is further propelled by the concentration of electronics manufacturing in China and Southeast Asia, where approximately 68% of global consumer electronics are assembled.
Meanwhile, European and American players like Wurth Elektronik and Amphenol are differentiating through specialized PCB solutions for premium appliances and mission-critical computer components. These companies are investing heavily in Industry 4.0 automation and sustainable manufacturing processes to maintain margins while meeting stringent environmental regulations.
Recent developments indicate an industry shift toward organic substrate PCBs and embedded component technologies, with multiple players announcing R&D partnerships during 2023-2024. Nippon Mektron’s recent collaboration with a major semiconductor firm to develop chip-embedded PCBs exemplifies this trend toward higher integration.
List of Key Consumer Electronics PCB Manufacturers Profiled
- AT&S (Austria)
- Sumitomo Electric Industries, Ltd (Japan)
- MEIKO Electronics Co.,Ltd (Japan)
- Nippon Mektron,Ltd (Japan)
- Wurth Elektronik (Germany)
- Unimicron Technology Corporation (Taiwan)
- Shenzhen Kinwong Electronic Co.,Ltd (China)
- Amphenol Corporation (U.S.)
- GulTech (Singapore)
- Victory Giant Technology (Huizhou) Co., Ltd (China)
Segment Analysis:
By Type
Multi-Layer Printed Circuit Board Segment Dominates Due to Increasing Demand for High-Performance Electronics
The market is segmented based on type into:
- Single Layer Printed Circuit Board
- Double Layer Printed Circuit Board
- Multi-Layer Printed Circuit Board
By Application
Computers and Tablets Segment Leads Owing to Expanding Digitalization Trends
The market is segmented based on application into:
- Ear Buds
- Dishwashers
- Radios
- Tablets
- Computers
- Wearable Devices
By Material
FR-4 Segment Holds Major Share for Its Excellent Mechanical and Electrical Properties
The market is segmented based on material into:
- FR-4
- Polyimide
- Rigid-Flex
- Others
By End User
OEMs Lead in Market Adoption for Direct Manufacturing Requirements
The market is segmented based on end user into:
- Original Equipment Manufacturers (OEMs)
- Contract Manufacturers
- Electric Component Suppliers
Regional Analysis: Consumer Electronics Printed Circuit Board Market
North America
The North American market is driven by strong demand for high-performance multi-layer PCBs in advanced consumer electronics such as wearables, IoT devices, and 5G-enabled products. The U.S., accounting for over 65% of the regional market share, leads in innovation with companies like Amphenol and Summit Interconnect focusing on miniaturization and flexible PCB solutions. However, supply chain disruptions and rising material costs pose challenges, reflecting broader industry trends. Sustainability initiatives are gaining traction, with manufacturers exploring halogen-free and lead-free PCB materials to comply with EPA and RoHS regulations.
Europe
Europe’s market emphasizes eco-friendly PCB manufacturing, aligning with the EU Circular Economy Action Plan. Germany and France dominate, leveraging their automotive and industrial electronics sectors to drive demand for high-reliability PCBs. The region shows increasing adoption of HDI (High-Density Interconnect) boards for compact devices, though growth is tempered by energy cost volatility and reliance on Asian suppliers for raw materials. Companies like AT&S and Würth Elektronik are investing in automation to offset labor costs, while REACH compliance remains a critical factor for PCB material selection.
Asia-Pacific
As the largest PCB production hub globally, the Asia-Pacific region (led by China, Japan, and South Korea) contributes over 70% of global PCB output. China’s Shenzhen cluster (home to Shengyi Technology and Kinwong Electronic) thrives on cost-efficient mass production, while Japan excels in high-end substrates for electronics giants like Sony and Panasonic. India emerges as a growth hotspot, with PCB demand rising 12% annually due to smartphone and appliance manufacturing. However, overcapacity in China and trade tensions create pricing pressures, pushing suppliers to diversify into automotive and medical electronics segments.
South America
The region remains a niche market, with Brazil accounting for 50% of regional PCB demand—primarily for single-layer and double-layer boards in consumer appliances. Limited local manufacturing forces reliance on imports, though tariffs on Chinese PCBs have spurred partnerships with Mexican and U.S. suppliers. Economic instability and currency fluctuations hinder investment in advanced PCB technologies, but the gaming console and audio equipment markets offer incremental growth opportunities.
Middle East & Africa
This emerging market focuses on basic PCB applications (radios, dishwashers) due to lower electronics penetration. The UAE and Turkey are key import hubs, with 15-20% annual growth in PCB demand linked to smart home device adoption. Lack of local fabrication units and dependence on Asian imports constrain market expansion, though Saudi Arabia’s Vision 2030 is attracting PCB suppliers for regional electronics assembly. Low-cost labor could eventually position North Africa as a PCB assembly destination, pending infrastructure improvements.
Report Scope
This market research report provides a comprehensive analysis of the global and regional Consumer Electronics Printed Circuit Board (PCB) markets, covering the forecast period 2025–2032. It offers detailed insights into market dynamics, technological advancements, competitive landscape, and key trends shaping the industry.
Key focus areas of the report include:
- Market Size & Forecast: Historical data and future projections for revenue, unit shipments, and market value across major regions and segments. The Global Consumer Electronics PCB market was valued at USD 5049 million in 2024 and is projected to reach USD 6060 million by 2032, growing at a CAGR of 2.7%.
- Segmentation Analysis: Detailed breakdown by product type (Single Layer, Double Layer, Multi-Layer PCBs), application (Ear Buds, Dishwashers, Tablets, Computers, Wearable Devices), and end-user industry to identify high-growth segments.
- Regional Outlook: Insights into market performance across North America (U.S., Canada, Mexico), Europe (Germany, France, U.K.), Asia-Pacific (China, Japan, South Korea), and other regions, with country-level analysis.
- Competitive Landscape: Profiles of leading market participants including MEIKO Electronics, Nippon Mektron, Sumitomo Electric, AT&S, and Unimicron Technology, covering their product portfolios, manufacturing capacities, and strategic developments.
- Technology Trends & Innovation: Assessment of emerging PCB technologies, miniaturization trends, high-density interconnects, flexible PCBs, and integration with IoT devices.
- Market Drivers & Restraints: Evaluation of factors such as growing consumer electronics demand, 5G adoption, and supply chain challenges impacting the PCB industry.
- Stakeholder Analysis: Strategic insights for PCB manufacturers, OEMs, raw material suppliers, and investors regarding market opportunities and challenges.
The research employs both primary and secondary methodologies, including interviews with industry experts, manufacturer surveys, and analysis of verified market data to ensure accuracy and reliability.
FREQUENTLY ASKED QUESTIONS:
What is the current market size of Global Consumer Electronics PCB Market?
-> Consumer Electronics Printed Circuit Board Market size was valued at US$ 18.4 billion in 2024 and is projected to reach US$ 26.7 billion by 2032, at a CAGR of 5.4% .
Which key companies operate in this market?
-> Leading players include MEIKO Electronics, Nippon Mektron, Sumitomo Electric, AT&S, Unimicron Technology, Shenzhen Kinwong, and Victory Giant Technology.
What are the key growth drivers?
-> Key drivers include rising demand for smart devices, 5G technology adoption, and increasing electronics miniaturization.
Which region dominates the market?
-> Asia-Pacific dominates with over 60% market share, driven by electronics manufacturing in China, Japan, and South Korea.
What are the emerging technology trends?
-> Emerging trends include flexible PCBs for wearables, high-density interconnect technology, and eco-friendly PCB materials.
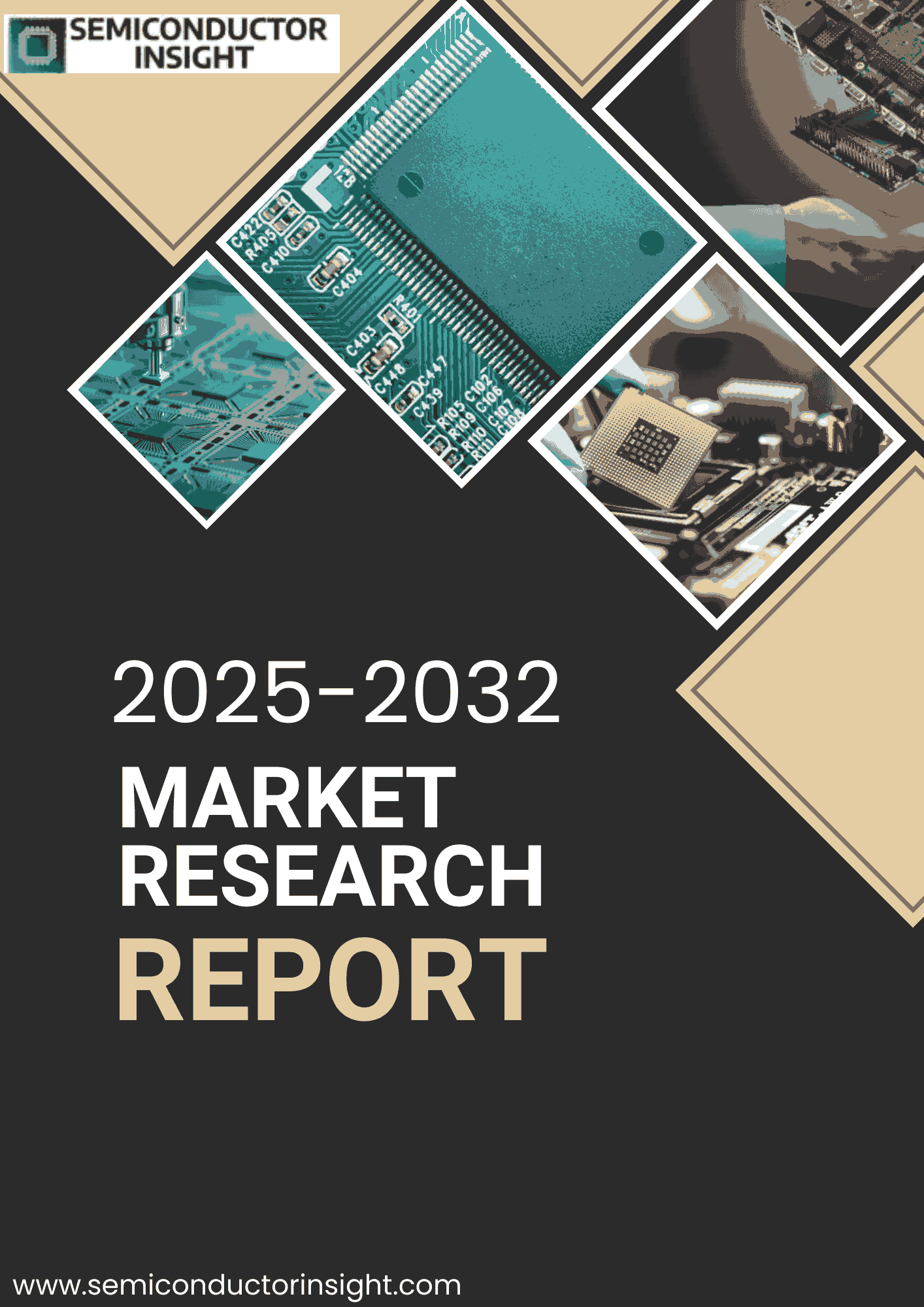
Get Sample Report PDF for Exclusive Insights
Report Sample Includes
- Table of Contents
- List of Tables & Figures
- Charts, Research Methodology, and more...
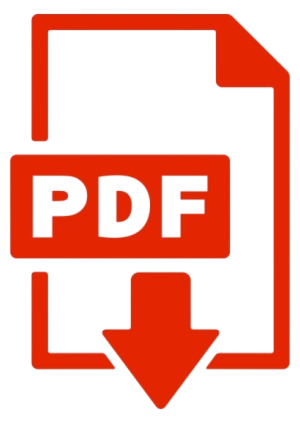