MARKET INSIGHTS
The global Chip Multilayer Inductor Market size was valued at US$ 987 million in 2024 and is projected to reach US$ 1.4 billion by 2032, at a CAGR of 5.1% during the forecast period 2025-2032.
Chip multilayer inductors are miniaturized passive electronic components constructed by layering multiple magnetic materials, offering high inductance with low DC resistance. These surface-mount devices play a critical role in power management circuits, RF applications, and electromagnetic interference (EMI) suppression across modern electronics. Their compact size and superior performance make them essential for smartphones, wearables, IoT devices, and automotive electronics where space optimization is crucial.
Market growth is primarily driven by the booming consumer electronics sector and rapid adoption of 5G technology, which requires high-frequency inductors for signal processing. The automotive industry’s shift toward electric vehicles has further accelerated demand, as these vehicles utilize 30-40% more inductors than conventional cars for power conversion systems. Additionally, advancements in material science have enabled manufacturers to develop inductors with higher current ratings and better thermal stability, expanding their applications in industrial automation and renewable energy systems.
MARKET DYNAMICS
MARKET DRIVERS
Expansion of 5G Infrastructure and IoT Devices Accelerates Demand for Miniaturized Components
The global rollout of 5G networks is creating unprecedented demand for chip multilayer inductors, with telecom infrastructure requiring high-frequency components that offer superior EMI suppression and power efficiency. Network operators worldwide are projected to invest over $600 billion in 5G capital expenditures by 2025, necessitating dense deployments of base stations and small cells. These components are critical for power management in massive MIMO antennas and RF front-end modules. Simultaneously, the IoT ecosystem continues its explosive growth, with active connections expected to surpass 30 billion by 2027. From smart home devices to industrial sensors, these connected endpoints rely on compact power solutions where chip multilayer inductors deliver optimal performance in limited board space.
Electric Vehicle Revolution Creates New Application Verticals
Automotive electrification represents a paradigm shift for passive component manufacturers, with electric vehicle production forecast to grow at a CAGR of 24% through 2030. Modern EVs contain approximately 3,000 chip multilayer inductors per vehicle – four times more than conventional automobiles – for critical functions including battery management systems, DC-DC converters, and onboard charging modules. Premium vehicle manufacturers are specifically demanding high-temperature stable inductors with >150°C operating ranges, pushing material science innovations in ferrite and ceramic formulations. Recent supply agreements between leading inductor suppliers and major automakers demonstrate this sector’s strategic importance, with contract values frequently exceeding $100 million annually for specialized automotive-grade components.
Consumer Electronics Miniaturization Trends Favor Advanced Inductor Solutions
Smartphone OEMs continue driving innovation in component integration, with high-end models now incorporating over 120 chip multilayer inductors for functions ranging from RF filtering to voltage regulation. The push for thinner form factors and higher component density has accelerated adoption of 0201 and 01005 package sizes, which now represent over 45% of mobile device inductor shipments. Wearable technology presents another high-growth segment, with smartwatch shipments growing 24% year-over-year as health monitoring capabilities become standard features. These space-constrained applications demand inductors with exceptional current handling capabilities in packages smaller than 0.6mm × 0.3mm, creating new technical challenges and premium pricing opportunities for manufacturers.
MARKET RESTRAINTS
Material Supply Chain Volatility Impacts Production Stability
The chip multilayer inductor industry faces significant headwinds from raw material availability, particularly for rare earth elements used in advanced ferrite formulations. Over 85% of global rare earth production originates from a single geographic region, creating concentration risks that became acutely apparent during recent trade disputes. Nickel-zinc ferrite prices have fluctuated by ±35% annually since 2020, forcing manufacturers to either absorb cost increases or renegotiate customer contracts. Lead times for ceramic substrates have similarly extended to 26+ weeks for some formulations, disrupting just-in-time production models. These material constraints are particularly challenging for manufacturers serving automotive and industrial markets, where qualification processes make rapid supplier switching impractical.
Technological Saturation in Mature Applications Limits Premium Pricing
While high-growth sectors command premium pricing, standard consumer electronics inductors face intensifying cost pressure as the technology matures. Benchmark pricing for mainstream 0402-sized power inductors has declined by 18% since 2021 due to manufacturing process optimizations and increased competition from regional suppliers. This commoditization is particularly evident in entry-level smartphones and IoT devices, where OEM procurement teams routinely demand year-over-year cost reductions. The situation creates margin compression for suppliers lacking differentiated technology, with gross margins for standard inductors now averaging 22-25% compared to 35-40% for automotive and specialty RF components.
Thermal Management Challenges in High-Power Applications
As power densities increase across all applications, managing heat dissipation becomes a critical limitation for chip multilayer inductor design. Server power supplies now demand inductors capable of handling 100A+ currents while maintaining core losses below 3%. These requirements push materials to their physical limits, with temperature coefficients becoming a key differentiator between suppliers. Some automotive applications experience ambient temperatures exceeding 125°C near engines and transmissions, requiring novel cooling solutions that add cost and complexity. The industry continues investing in composite materials and advanced via structures to address these challenges, but thermal constraints remain a fundamental limitation for next-generation designs.
MARKET OPPORTUNITIES
Advanced Packaging Technologies Enable Next-Generation Performance
Emergent embedded component technologies create compelling opportunities for inductor suppliers to increase value capture. Fan-out wafer-level packaging (FOWLP) now allows inductors to be integrated directly into semiconductor packages, reducing board space by up to 40% while improving electrical performance. Major foundries report design wins for these solutions in premium smartphones and networking equipment, with average selling prices 3-5× higher than discrete components. Similarly, 3D printed inductors using additive manufacturing techniques demonstrate exceptional high-frequency characteristics, opening new possibilities for millimeter-wave and THz applications. These advanced integration approaches position inductors as enablers of next-generation electronic systems rather than commoditized passives.
Renewable Energy Infrastructure Buildout Drives Specialty Demand
The global transition to renewable energy creates strong demand for specialized inductors in solar microinverters, wind turbine converters, and energy storage systems. Central inverter designs now incorporate over 200 high-current inductors per unit, with string inverter counts exceeding 50 components per kilowatt. These applications require inductors with exceptional reliability under cyclic loading, with design lifetimes exceeding 25 years. The solar microinverter market alone is projected to grow at 15% CAGR through 2030, creating a substantial addressable market for suppliers who can meet stringent durability requirements. Recent product certifications for -40°C to +85°C operation with <1% parameter drift are becoming baseline requirements rather than differentiators in this space.
Medical Electronics Miniaturization Opens New Frontiers
Implantable medical devices and portable diagnostic equipment represent high-value opportunities for inductor suppliers. Modern pacemakers require inductors with unprecedented reliability (0.1 FIT rates) in packages smaller than 1mm², while MRI-compatible materials add another layer of technical complexity. The endoscopic capsule market has similarly stringent requirements, demanding components that maintain performance after sterilization cycles while consuming minimal power. These medical applications command price premiums of 7-10× compared to consumer equivalents, with gross margins often exceeding 60%. Regulatory documentation and traceability requirements create significant barriers to entry, protecting established suppliers in this high-margin niche.
MARKET CHALLENGES
Precision Manufacturing Requirements Limit Production Scalability
Chip multilayer inductor fabrication demands extraordinary process control, with layer-to-layer alignment tolerances below 5μm for high-density designs. Maintaining these tolerances across high-volume production runs requires specialized equipment and rigorous process monitoring, creating substantial capital expenditure requirements. New production lines for advanced inductors now require investments exceeding $50 million, with equipment lead times stretching beyond 18 months. This limits the industry’s ability to rapidly scale capacity in response to demand surges, as evidenced by allocation conditions persisting through 2023. Even established manufacturers report yield challenges when transitioning to next-generation designs, with initial production yields for novel materials sometimes below 60%.
Standardization Gaps Complicate Cross-Platform Adoption
The lack of universal performance metrics for next-generation inductors creates integration challenges for OEMs. While basic parameters like inductance and DC resistance follow industry standards, emerging characteristics such as harmonic distortion under load and intermodulation effects lack standardized measurement protocols. This issue is particularly acute for RF inductors above 6GHz, where different test methodologies can produce variation exceeding 15% in reported Q factors. Automotive customers increasingly demand application-specific qualification standards, with some OEMs maintaining over 20 unique test profiles for inductors used in different vehicle subsystems. These fragmented requirements increase design-in complexity and slow time-to-market for innovative products.
Talent Shortages Constrain Innovation Pipeline
Developing advanced inductor technologies requires rare combinations of material science expertise, RF engineering knowledge, and semiconductor packaging experience. The global talent pool for these multidisciplinary specialists remains extremely limited, with top researchers commanding compensation packages exceeding $300,000 annually. University programs struggle to produce graduates with the necessary cross-disciplinary training, creating fierce competition for qualified personnel. This talent crunch is particularly evident in magnetic material development, where the average age of principal researchers exceeds 50 years. Without significant investments in workforce development, the industry risks hitting innovation bottlenecks just as application demands become most stringent.
CHIP MULTILAYER INDUCTOR MARKET TRENDS
Miniaturization and High-Frequency Performance Drive Market Expansion
The global chip multilayer inductor market is experiencing robust growth, largely driven by the increasing demand for miniaturized electronic components with superior high-frequency performance. As smartphones, wearables, and IoT devices continue to shrink in size while requiring enhanced functionality, manufacturers are prioritizing components that offer space-saving designs without compromising electrical performance. Leading manufacturers have responded by developing inductors with ultra-thin profiles measuring less than 0.4mm, achieving inductance values up to 10μH while maintaining stable operation in frequency ranges exceeding 100MHz. The proliferation of 5G networks further accelerates this trend, as these next-generation communication systems demand components capable of handling GHz-range frequencies with minimal signal loss.
Other Trends
Automotive Electrification Creates New Opportunities
The rapid electrification of vehicles represents one of the most significant growth drivers for chip multilayer inductors. Modern electric vehicles contain over 3,700 inductor components on average, with usage spanning power conversion systems, battery management, and advanced driver assistance systems (ADAS). Automotive-grade inductors now feature enhanced thermal stability, with operational temperature ranges extending beyond 150°C to withstand harsh under-hood environments. Furthermore, the growing adoption of 48V mild hybrid systems requires inductors capable of handling higher power densities than conventional 12V systems, prompting manufacturers to develop specialized product lines.
Technological Advancements in Materials and Manufacturing
Recent breakthroughs in magnetic material science are enabling significant performance improvements in chip multilayer inductors. The development of nano-crystalline and amorphous magnetic materials has resulted in components with 30-40% lower core losses compared to traditional ferrite-based solutions. Concurrently, advancements in multilayer ceramic fabrication techniques allow for more precise control over layer thickness and conductor patterns, enabling better Q factors and higher self-resonant frequencies. Some manufacturers have adopted 3D printing technologies for prototyping and small-scale production, reducing development cycles from months to weeks for customized inductor solutions.
Supply Chain Localization Gains Momentum
In response to global supply chain disruptions, many electronics manufacturers are pursuing regionalization strategies for critical components including chip multilayer inductors. This trend has led to increased production capacity expansions in multiple geographic markets, with several leading suppliers establishing new fabrication facilities in North America and Southeast Asia. The localization movement is particularly noticeable in the automotive sector, where just-in-time manufacturing requirements and supply security concerns drive demand for locally-sourced electronic components. Notably, this shift coincides with growing investments in domestic semiconductor ecosystems across major economies.
COMPETITIVE LANDSCAPE
Key Industry Players
Innovation and Miniaturization Drive Competition in Chip Inductor Market
The global chip multilayer inductor market features a semi-consolidated competitive landscape, with Japanese manufacturers maintaining technological dominance while Chinese players rapidly expand production capacity. TDK Corporation leads the market with approximately 22% revenue share in 2024, owing to its advanced ferrite material technology and strong partnerships with automotive OEMs. The company’s recent development of ultra-thin 0.25mm height inductors for 5G smartphones exemplifies its innovation leadership.
Murata Manufacturing follows closely with an 18% market share, having made significant strides in high-frequency inductance solutions for IoT applications. Their proprietary multilayer ceramic technology enables superior performance in compact form factors – a critical advantage as device miniaturization accelerates across industries.
Market dynamics reveal an interesting bifurcation where Taiyo Yuden and Vishay Intertechnology are gaining traction in the mid-range segment through cost-optimized solutions, particularly for consumer electronics. Meanwhile, Sunlord Electronics and Fenghua Advanced Technology represent the growing influence of Chinese manufacturers, leveraging domestic supply chains to offer competitive pricing while gradually improving technical specifications.
Recent strategic movements indicate increased vertical integration, with Kyocera AVX acquiring specialty material suppliers to secure critical raw materials. The industry is also witnessing a surge in patent filings around low-loss magnetic composites, reflecting intensifying R&D competition to achieve better thermal performance and higher current handling capabilities.
List of Key Chip Multilayer Inductor Companies Profiled
- TDK Corporation (Japan)
- Murata Manufacturing Co., Ltd. (Japan)
- Taiyo Yuden Co., Ltd. (Japan)
- Vishay Intertechnology, Inc. (U.S.)
- Sunlord Electronics (China)
- Chilisin Electronics (Taiwan)
- Fenghua Advanced Technology (China)
- Kyocera AVX (Japan)
- Shenzhen Zhenhua Fu Electronics (China)
- Laird Technologies (U.K.)
- INPAQ Technology (Taiwan)
- Darfon Electronics (Taiwan)
Segment Analysis:
By Type
Ferrite Inductor Segment Leads Due to High Performance in Power Electronics Applications
The market is segmented based on type into:
- Ferrite Inductor
- Ceramic Inductor
- Others
By Application
Consumer Electronics Segment Dominates with Growing Demand for Compact Power Solutions
The market is segmented based on application into:
- Consumer Electronics
- Energy
- Industrial
- Medical
- Others
By Material
Nickel-Zinc Ferrite Segment Leads with Superior High-Frequency Performance
The market is segmented based on material into:
- Nickel-Zinc Ferrite
- Manganese-Zinc Ferrite
- Iron-based Material
By End User
Automotive Electronics Segment Shows Strong Growth with EV Market Expansion
The market is segmented based on end user into:
- Consumer Electronics Manufacturers
- Automotive Electronics
- Industrial Equipment Manufacturers
- Telecommunication Companies
Regional Analysis: Chip Multilayer Inductor Market
North America
North America remains a critical hub for the Chip Multilayer Inductor (MLI) market, driven by robust demand from the consumer electronics, automotive, and telecommunications sectors. The region benefits from strong R&D investments in 5G infrastructure, advanced driver-assistance systems (ADAS), and IoT devices, which require high-performance MLIs for efficient power management. The U.S. leads in adoption, with semiconductor giants and tech firms integrating MLIs into smartphones, wearables, and electric vehicle charging systems. However, supply chain disruptions and fluctuating raw material costs pose challenges. Regulatory pressures, particularly regarding lead-free and RoHS-compliant components, further influence manufacturing strategies.
Europe
Europe’s MLI market thrives on stringent quality standards and a growing emphasis on energy-efficient solutions. Countries like Germany and France dominate due to their strong automotive and industrial automation sectors, where MLIs are essential for power converters and EMI suppression. The EU’s Green Deal and Circular Economy Action Plan push manufacturers toward sustainable materials and miniaturized designs. Despite steady demand, the region faces competition from Asian suppliers, compelling local players to focus on high-value niche applications, such as medical devices and renewable energy systems. Brexit-related trade complexities also introduce logistical hurdles for UK-based operations.
Asia-Pacific
Asia-Pacific is the largest and fastest-growing MLI market, accounting for over 60% of global consumption. China, Japan, and South Korea lead production, leveraging their established electronics manufacturing ecosystems. The proliferation of 5G smartphones, coupled with government-backed initiatives like China’s “Made in China 2025,” fuels demand. India and Southeast Asia emerge as promising markets due to expanding electronics assembly hubs and rising EV adoption. However, price sensitivity and overcapacity in low-end MLIs create margin pressures. Regional players, such as Murata and TDK, dominate through vertical integration, while smaller firms compete on customization for consumer electronics.
South America
South America’s MLI market is nascent but evolving, supported by gradual industrialization and increasing electronics imports. Brazil and Argentina show potential, particularly in automotive electronics and energy storage applications. However, economic instability, currency volatility, and underdeveloped semiconductor supply chains restrict growth. Local manufacturers rely heavily on imports for raw materials, making them vulnerable to global price fluctuations. Investments in telecom infrastructure and renewable energy projects could unlock opportunities, but progress remains slow compared to other regions.
Middle East & Africa
The Middle East & Africa exhibit modest MLI demand, primarily driven by telecom infrastructure upgrades and limited industrial diversification. The UAE and Saudi Arabia lead in technology adoption, with smart city projects and 5G rollouts creating niche opportunities. Africa’s growth is hindered by low electronics production capacity and reliance on imported components. While the region holds long-term potential, particularly for MLIs in solar energy systems, immediate market penetration is challenged by fragmented logistics and limited technical expertise. Strategic partnerships with global suppliers may catalyze future development.
Report Scope
This market research report provides a comprehensive analysis of the global and regional Chip Multilayer Inductor markets, covering the forecast period 2025–2032. It offers detailed insights into market dynamics, technological advancements, competitive landscape, and key trends shaping the industry.
Key focus areas of the report include:
- Market Size & Forecast: Historical data and future projections for revenue, unit shipments, and market value across major regions and segments.
- Segmentation Analysis: Detailed breakdown by product type (Ferrite Inductor, Ceramic Inductor, Others), application (Consumer Electronics, Energy, Industrial, Medical, Others), and end-user industry to identify high-growth segments.
- Regional Outlook: Insights into market performance across North America, Europe, Asia-Pacific, Latin America, and Middle East & Africa, including country-level analysis.
- Competitive Landscape: Profiles of leading market participants including TDK, Murata, Taiyo Yuden, Vishay, and others, covering product portfolios, market shares, and strategic developments.
- Technology Trends & Innovation: Assessment of emerging manufacturing techniques, miniaturization trends, and integration with 5G/IoT applications.
- Market Drivers & Restraints: Evaluation of factors like 5G adoption, EV proliferation, and supply chain challenges impacting market growth.
- Stakeholder Analysis: Strategic insights for component manufacturers, OEMs, and investors regarding market opportunities.
The analysis employs primary and secondary research methodologies, including industry interviews and verified market data, to ensure accuracy and reliability.
FREQUENTLY ASKED QUESTIONS:
What is the current market size of Global Chip Multilayer Inductor Market?
-> The global Chip Multilayer Inductor size was valued at US$ 987 million in 2024 and is projected to reach US$ 1.4 billion by 2032, at a CAGR of 5.1% during the forecast period 2025-2032.
Which key companies operate in Global Chip Multilayer Inductor Market?
-> Key players include TDK, Murata, Taiyo Yuden, Vishay, Sunlord Electronics, Chilisin Electronics (YAGEO), and Kyocera.
What are the key growth drivers?
-> Major drivers include 5G technology adoption, proliferation of IoT devices, electric vehicle production, and demand for miniaturized electronic components.
Which region dominates the market?
-> Asia-Pacific dominates with over 65% market share, led by China, Japan, and South Korea’s strong electronics manufacturing base.
What are the emerging trends?
-> Emerging trends include higher frequency inductors for 5G, automotive-grade components for EVs, and advanced materials for better thermal performance.
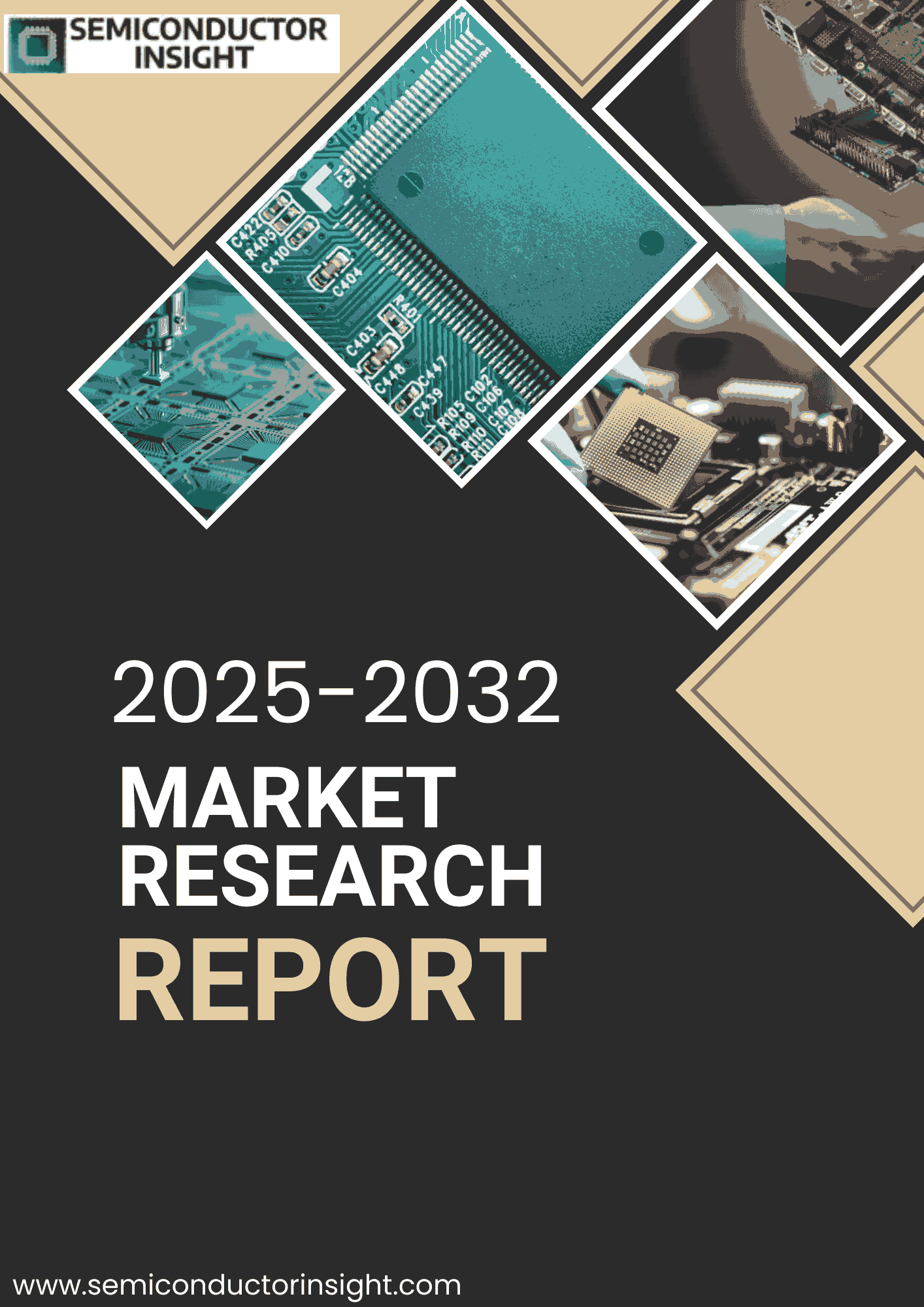
Get Sample Report PDF for Exclusive Insights
Report Sample Includes
- Table of Contents
- List of Tables & Figures
- Charts, Research Methodology, and more...
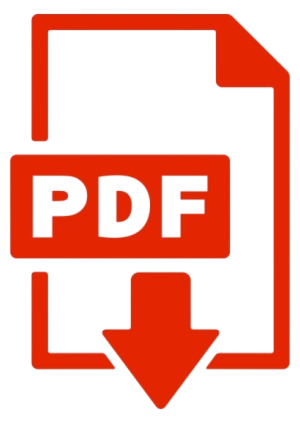